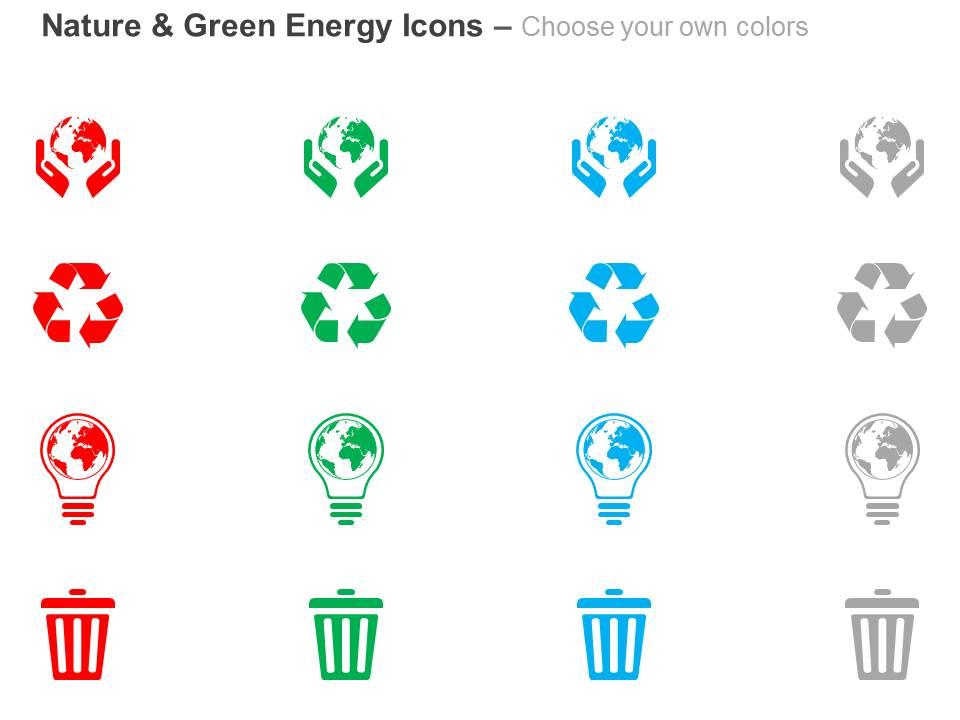
Athena Pro Core provides a comprehensive nutrition system for plants. It is suitable for all stages of growth. This solution is compatible with most dosing systems and provides strong nutrition for plants across all stages of growth. You can manage your application using the mobile app. For any question, you can also reach out to the customer support team.
Athena Pro Core can be used with all dosing systems
Athena Pro Core provides powerful nutrition for plants. It includes the essential microelements, nutrients and vitamins necessary for growth. Its proprietary blend contains small amounts of each element in order to make a uniform and effective mixture for any reservoir. It can be used to mix stock tanks and it is compatible with all dosing equipment. To provide the best plant nutrition, combine it with Athena Pro Grow (or Athena Pro Bloom).
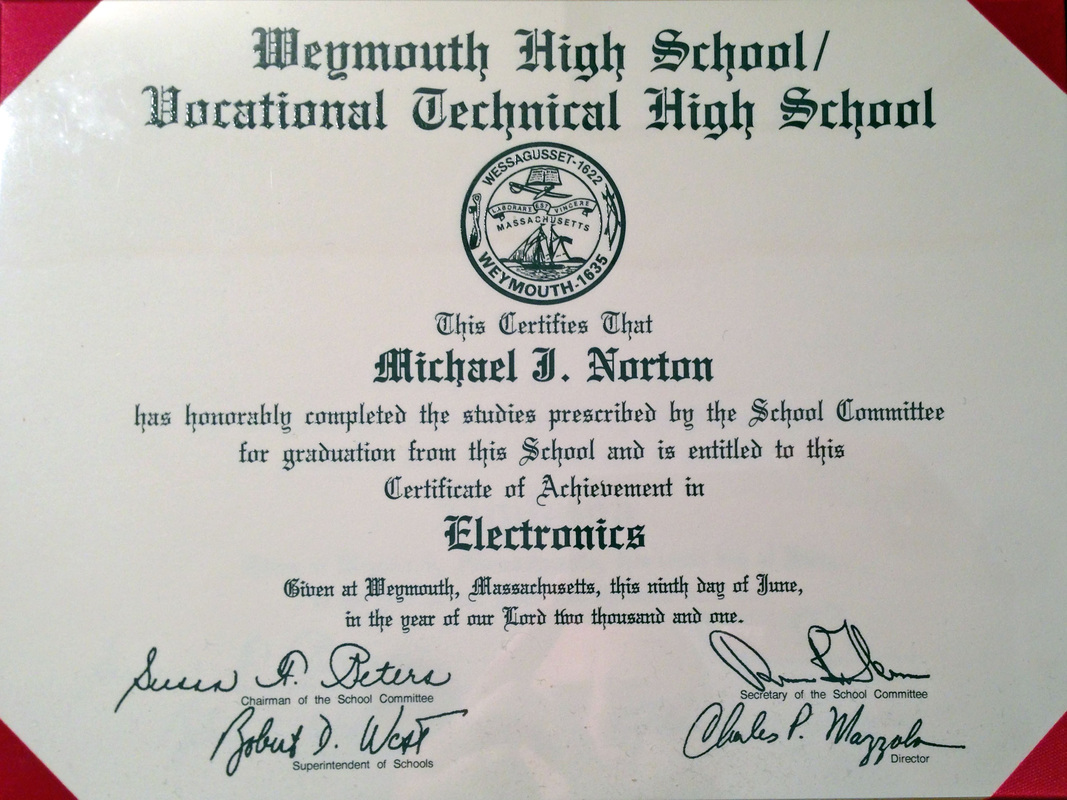
Athena Pro Core offers strong nutritional support for all stages of plant life
Athena Pro Core a highly concentrated fertilizer delivers the necessary microelements as well as nutrients to support plant growth. It can be used in stock tanks and compatible with all dosing systems. It is completely soluble so it won't clog irrigation system or create sediment in reservoirs. For best results, Athena Pro Core must be used together with Athena Pro Grow & Pro Bloom.
Athena Pro Core, a focus assessment system that assesses Ohio's Learning Standards, is called Athena Pro Core.
Senate Bill 2 was a 2004 Ohio law that created a state Educator Standards Board. This board established the Ohio Learning Standards for teachers and principals. It also required the creation of an Ohio Teacher Evaluation System in order to assess teachers in accordance the standards. This legislation was passed to improve teacher performance. The state of Ohio aims to achieve this goal through a comprehensive evaluation system that considers teacher strengths and weaknesses and supports their growth as educators.
Athena Pro Core is a mobile app
Athena Pro Core provides high-quality nutrition for plants, including microelements. It can be used with all dosing systems and is 100% soluble so it won't clog irrigation lines or cause sediment to build up in reservoirs. It should be used in conjunction With Athena Pro Grow. It is available both in dry and concentrated form.
Athena Pro Core integrates seamlessly with ERP software
Integration of Athena Pro Core with an ERP software such as QuickBooks is possible thanks to the software's built-in Electronic Document Management. This enables you to manage a wide variety of documents, such as invoices, claims, and more. The system also has a customizable user interface that helps you deal with different roles within your practice. You can see all your tasks and assign them as needed to different employees.
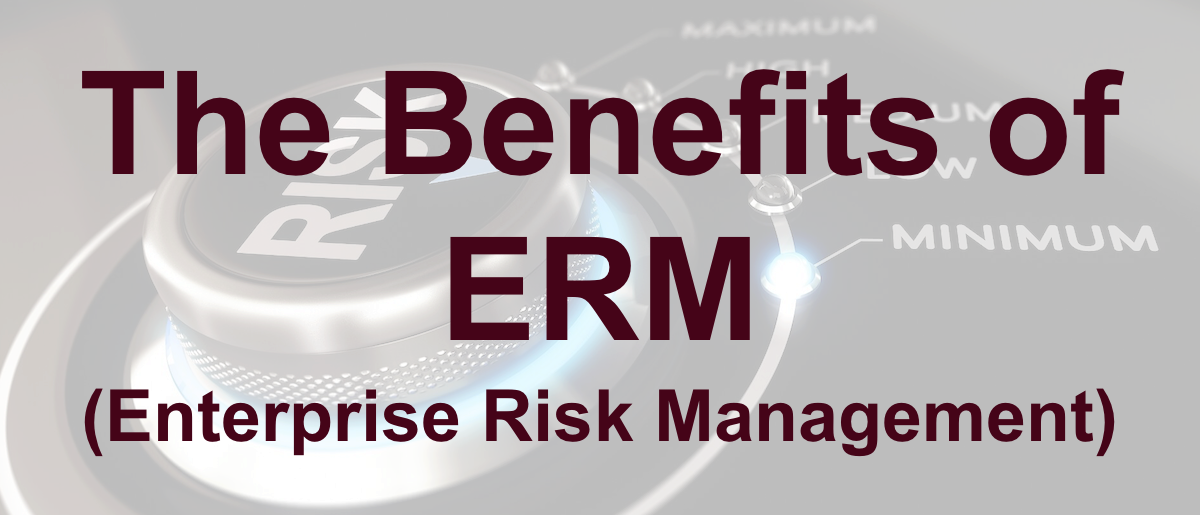
Athena Pro Core offers enterprise grade security
Athena's smart card platform is certified and accredited by leading global security standards bodies. It has been tested rigorously to ensure that it conforms to the security standards of leading US, European and Brazilian organisations. Athena solutions are flexible and cost effective.
FAQ
What is a basic management tool used in decision-making?
The decision matrix is a powerful tool that managers can use to help them make decisions. It helps them think systematically about all the options available to them.
A decision matrix allows you to represent alternatives as columns and rows. This makes it easy for you to see how each option affects other options.
The boxes on the left hand side of this matrix represent four possible choices. Each box represents one option. The top row represents the current state of affairs, and the bottom row is indicative of what would happen in the event that nothing were done.
The effect of choosing Option 1 can be seen in column middle. In this case, it would mean increasing sales from $2 million to $3 million.
The next two columns show the effects of choosing Options 2 and 3. These are good changes, they increase sales by $1million or $500,000. These positive changes have their downsides. Option 2 increases costs by $100 thousand, while Option 3 decreases profits to $200 thousand.
The last column shows you the results of Option 4. This involves decreasing sales by $1 million.
The best part about using a decision matrix to guide you is that you don’t need to keep track of which numbers go where. The best thing about a decision matrix is that you can simply look at the cells, and immediately know whether one option is better or not.
This is because the matrix has already taken care of the hard work for you. It's simply a matter of comparing the numbers in the relevant cells.
Here's an example showing how you might use a Decision Matrix in your business.
It is up to you to decide whether to spend more money on advertising. If you do this, you will be able to increase revenue by $5000 per month. You'll also have additional expenses up to $10,000.
The net result of advertising investment can be calculated by looking at the cell below that reads "Advertising." It is 15 thousand. Advertising is more valuable than its costs.
What are the steps in the decision-making process in management?
The decision-making process for managers is complex and multifaceted. It includes many factors such as analysis, strategy planning, implementation and measurement. Evaluation, feedback and feedback are just some of the other factors.
When managing people, the most important thing to remember is that they are just human beings like you and make mistakes. As such, there are always opportunities for improvement, especially when you put in the effort to improve yourself.
In this video, we explain what the decision-making process looks like in Management. We will explain the importance of different types decisions and how every manager can make them. These topics are covered in this course:
How can a manager motivate employees?
Motivation is the desire for success.
It is possible to be motivated by doing something you enjoy.
You can also feel motivated by making a positive contribution to the success in the organization.
For example: If you want to be a doctor, you might find it more motivating seeing patients than reading medical books all day.
Another type of motivation comes from within.
You may feel strongly that you are responsible to help others.
You might even enjoy the work.
If you don't feel motivated, ask yourself why.
Then, consider ways you could improve your motivation.
What is Six Sigma?
It's a method for quality improvement that focuses on customer service as well as continuous learning. The goal is to eliminate defects by using statistical techniques.
Motorola developed Six Sigma in 1986 to help improve its manufacturing processes.
It was quickly adopted by the industry and many companies are now using six-sigma to improve product design, production, delivery, customer service, and product design.
What are the 5 management processes?
Planning, execution, monitoring and review are the five stages of any business.
Planning means setting goals for the long-term. It involves setting goals and making plans.
Execution occurs when you actually carry out the plans. These plans must be adhered to by everyone.
Monitoring is a way to track progress towards your objectives. Monitoring should include regular reviews of performance against goals and budgets.
Reviews take place at the end of each year. These reviews allow you to evaluate whether the year was successful. If not, changes may be made to improve the performance next time around.
After the annual review is complete, evaluations are conducted. It helps you identify the successes and failures. It also provides feedback on how well people performed.
How does Six Sigma function?
Six Sigma employs statistical analysis to identify problems, measure them and analyze root causes. Six Sigma also uses experience to correct problems.
The first step to solving the problem is to identify it.
Next, data will be collected and analyzed to determine trends and patterns.
Next, corrective steps are taken to fix the problem.
Final analysis of data is done to determine if the problem has been solved.
This cycle continues until there is a solution.
What is TQM exactly?
The industrial revolution was when companies realized that they couldn't compete on price alone. This is what sparked the quality movement. They had to improve efficiency and quality if they were to remain competitive.
In response to this need for improvement, management developed Total Quality Management (TQM), which focused on improving all aspects of an organization's performance. It involved continuous improvement, employee participation, and customer satisfaction.
Statistics
- As of 2020, personal bankers or tellers make an average of $32,620 per year, according to the BLS. (wgu.edu)
- The profession is expected to grow 7% by 2028, a bit faster than the national average. (wgu.edu)
- The average salary for financial advisors in 2021 is around $60,000 per year, with the top 10% of the profession making more than $111,000 per year. (wgu.edu)
- The BLS says that financial services jobs like banking are expected to grow 4% by 2030, about as fast as the national average. (wgu.edu)
- This field is expected to grow about 7% by 2028, a bit faster than the national average for job growth. (wgu.edu)
External Links
How To
How can Lean Manufacturing be done?
Lean Manufacturing uses structured methods to reduce waste, increase efficiency and reduce waste. They were developed in Japan by Toyota Motor Corporation (in the 1980s). The main goal was to produce products at lower costs while maintaining quality. Lean manufacturing emphasizes removing unnecessary steps from the production process. It is composed of five fundamental elements: continuous improvement; pull systems, continuous improvements, just-in–time, kaizen, continuous change, and 5S. Pull systems are able to produce exactly what the customer requires without extra work. Continuous improvement means continuously improving on existing processes. Just-in time refers to components and materials being delivered right at the place they are needed. Kaizen is continuous improvement. This can be achieved by making small, incremental changes every day. Fifth, the 5S stand for sort, set up in order to shine, standardize, maintain, and standardize. These five elements are combined to give you the best possible results.
The Lean Production System
Six key concepts are the basis of lean production:
-
Flow - focus on moving material and information as close to customers as possible;
-
Value stream mapping: This is a way to break down each stage into separate tasks and create a flowchart for the entire process.
-
Five S's – Sort, Put In Order Shine, Standardize and Sustain
-
Kanban - visual cues such as stickers or colored tape can be used to track inventory.
-
Theory of constraints - identify bottlenecks in the process and eliminate them using lean tools like kanban boards;
-
Just-intime - Order components and materials at your location right on the spot.
-
Continuous improvement - make incremental improvements to the process rather than overhauling it all at once.