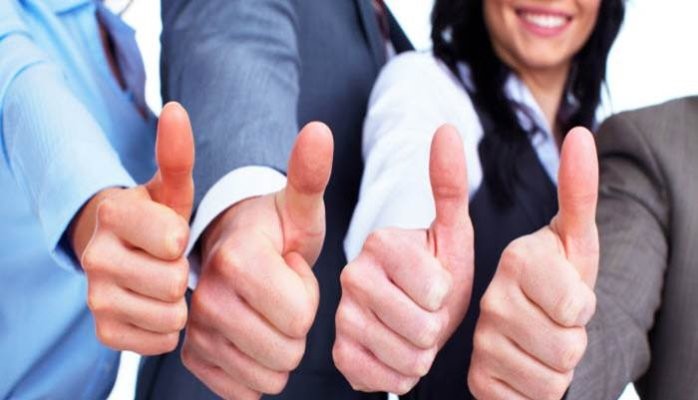
The process of industrial waste management involves the collection, transporting, and proper disposal of hazardous waste. Most hazardous waste is either removed from the site or disposed in a secure facility. This prevents contamination of the surrounding areas. This is a costly procedure that requires the construction of a new site as well as transportation of large quantities of waste. Another option is to do on-site remediation. This involves building a new facility and treating water pollution. Some plants employ full containment which means that the entire site is capped and groundwater flow cut.
Construction and demolition waste
Construction and demolition debris is an industrial waste generated during construction. Most construction waste can be legally disposed of in landfills. In some places, however, illegally dumped waste on land and in water bodies is possible. Furthermore, it can be hazardous for the environment and against regulations protecting commerce or human health. Each year, millions of tons worth of building-related debris are dumped in landfills across the United States. Construction waste management must adhere to strict regulations.
Manufacturing waste
The circular economy includes the management of manufacturing waste. As energy and resources are being conserved, so has the use of recycled material. Manufacturers have a wide range of options today to recycle and manage their waste. Some technologies allow manufacturers to reduce their production costs and increase their profits.
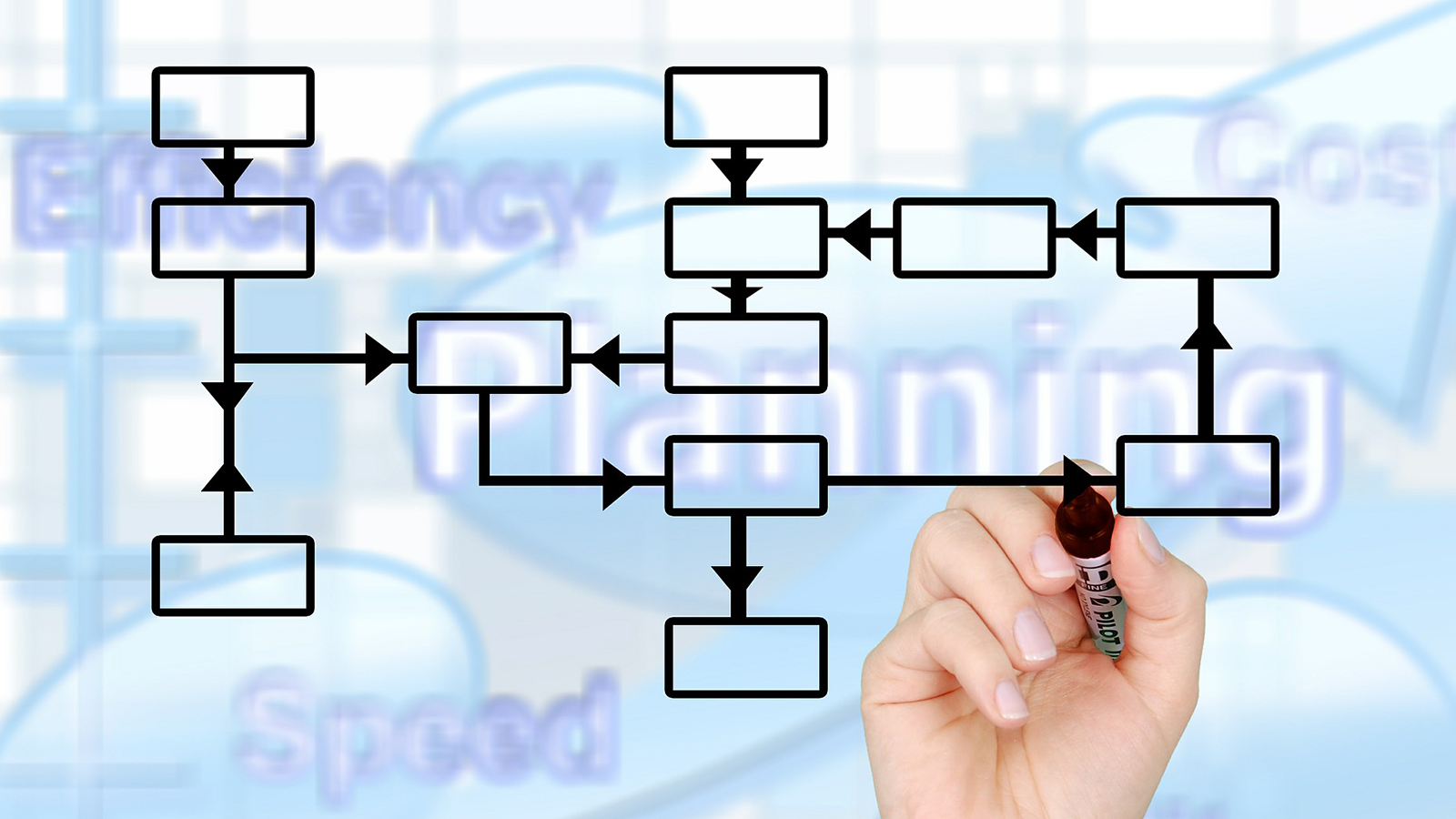
Agriculture waste
Agriculture waste is generated from the farming processes and includes solid wastes generated during animal production, crop production, and food and meat processing. The agricultural industry produces solid wastes from animal carcasses, crop residues, animal feeding waste, feathers, and hoofs.
Chemical waste
Most chemical waste is considered hazardous and poses a threat to the environment or human health. There are regulations in place that can help you safely dispose of hazardous materials. Incorrect disposal of hazardous materials can also lead to heavy environmental penalties. However, some types of waste are not considered hazardous and, thus, are not subject to the same regulations.
Mining waste
Mining creates huge amounts of waste. It is essential that miners know how to properly manage and dispose this waste. Erich Lawson is an environmentalist and freelance writer. Erich Lawson is a freelancer who writes about recycling topics such as compactors or balers as well managing industrial waste. He loves helping businesses reduce their garbage costs and increase their revenue through recycling.
Oil & gas waste
There are special requirements for oil and gas wastewater management. The most common types of oil & gas wastes include drilling wastes, production fluids, and produced waters. These wastes should be disposed of carefully to minimize their impact on the environment.
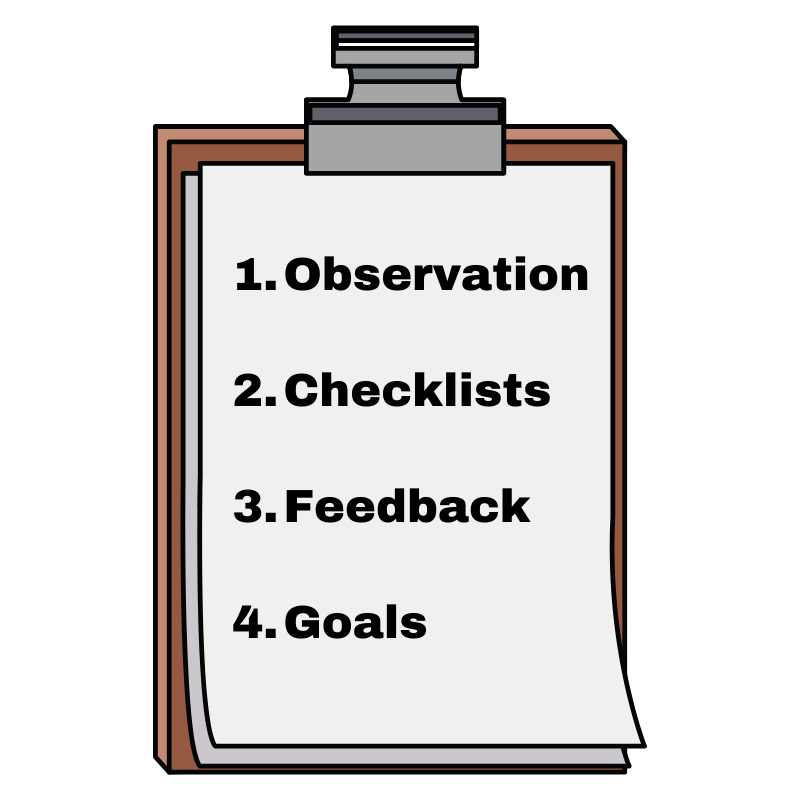
Nuclear waste
Solid waste disposal is essential for the health of the public and the environment. Specially constructed engineering modules can safely dispose of waste with a shorter half-life (less that 100 years), such as reinforced concrete trenches and tile holes or stone lined trenches. Near Surface Disposal Facility or NSDF is constructed below the ground. Here, the waste can be buried upto 500 metres below ground. Multi-barrier systems are used to stop radioactive waste from spreading.
Other
Global industrial waste management is fragmented. There are many players both local and global. In terms of waste management, the key players are focused on product innovation. The industrial waste management market includes all types of solid, liquid, or gaseous waste from various industrial sectors. These wastes may contain hazardous and other non-hazardous substances. Many of these materials are either disposed in landfills or incinerated. These practices can be very harmful to wildlife and the environment.
FAQ
What is Six Sigma?
It is a way to improve quality that places emphasis on customer service and continuous learning. The goal is to eradicate defects through statistical techniques.
Motorola's 1986 efforts to improve manufacturing process efficiency led to the creation of Six Sigma.
It was quickly adopted by the industry and many companies are now using six-sigma to improve product design, production, delivery, customer service, and product design.
How can a manager motivate employees?
Motivation refers to the desire or need to succeed.
It is possible to be motivated by doing something you enjoy.
Another way to get motivated is to see yourself as a contributor to the success of the company.
For example: If you want to be a doctor, you might find it more motivating seeing patients than reading medical books all day.
Motivation comes from within.
One example is a strong sense that you are responsible for helping others.
You might even enjoy the work.
Ask yourself why you aren't feeling motivated.
You can then think of ways to improve your motivation.
What is Kaizen?
Kaizen, a Japanese term that means "continuous improvement," is a philosophy that encourages employees and other workers to continuously improve their work environment.
Kaizen is based upon the belief that each person should be capable of doing his or her job well.
Statistics
- As of 2020, personal bankers or tellers make an average of $32,620 per year, according to the BLS. (wgu.edu)
- Our program is 100% engineered for your success. (online.uc.edu)
- Hire the top business lawyers and save up to 60% on legal fees (upcounsel.com)
- This field is expected to grow about 7% by 2028, a bit faster than the national average for job growth. (wgu.edu)
- The profession is expected to grow 7% by 2028, a bit faster than the national average. (wgu.edu)
External Links
How To
How can Lean Manufacturing be done?
Lean Manufacturing processes are used to reduce waste and improve efficiency through structured methods. They were created by Toyota Motor Corporation in Japan in the 1980s. It was designed to produce high-quality products at lower prices while maintaining their quality. Lean manufacturing focuses on eliminating unnecessary steps and activities from the production process. It is made up of five elements: continuous improvement, continuous improvement, just in-time, continuous change, and 5S. Pull systems involve producing only what the customer wants without any extra work. Continuous improvement refers to continuously improving existing processes. Just-in-time refers to when components and materials are delivered directly to the point where they are needed. Kaizen stands for continuous improvement. Kaizen can be described as a process of making small improvements continuously. The 5S acronym stands for sort in order, shine standardize and maintain. These five elements are used together to ensure the best possible results.
The Lean Production System
Six key concepts make up the lean manufacturing system.
-
Flow - focus on moving material and information as close to customers as possible;
-
Value stream mapping: This is a way to break down each stage into separate tasks and create a flowchart for the entire process.
-
Five S's: Sort, Shine Standardize, Sustain, Set In Order, Shine and Shine
-
Kanban: Use visual signals such stickers, colored tape, or any other visual cues, to keep track your inventory.
-
Theory of constraints - identify bottlenecks during the process and eliminate them with lean tools like Kanban boards.
-
Just-in Time - Send components and material directly to the point-of-use;
-
Continuous improvement - incremental improvements are made to the process, not a complete overhaul.