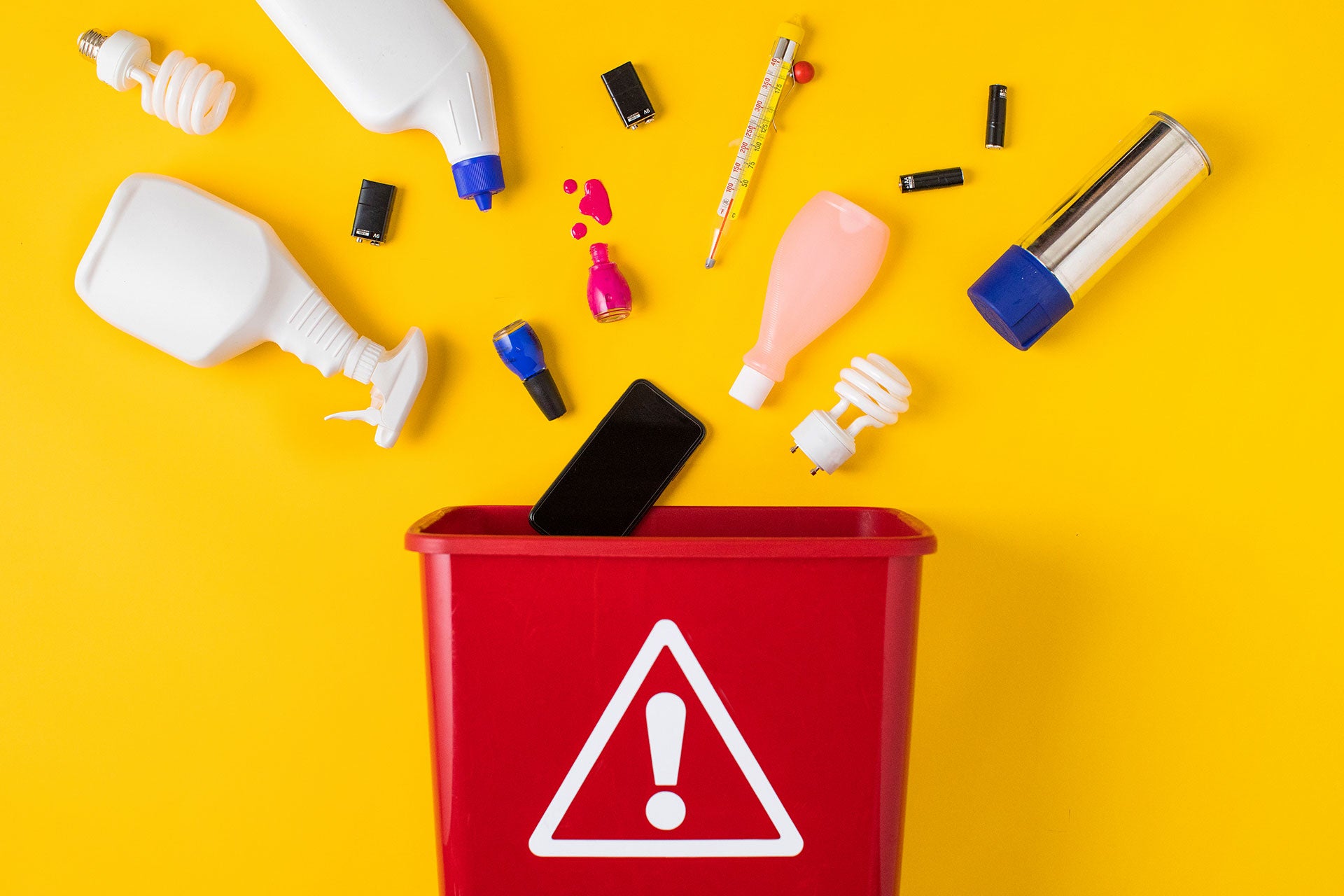
The fundamentals of management and organizations are the principles that govern how we plan, implement, and measure our efforts. These principles are based on the works of classic economists such as Adam Smith, John Stuart Mill and Eli Whitney. Matthew Boulton, Eli Watt, and Matthew Boulton were also technical innovators in this field.
Management
Management is responsible for ensuring that organizations run smoothly and that everyone knows what they do. Management is essential to ensure that businesses succeed, no matter how large or small they may be. This program is intended for middle-level and junior managers in large corporations, small businesses, nonprofits, government services, and other organizations.
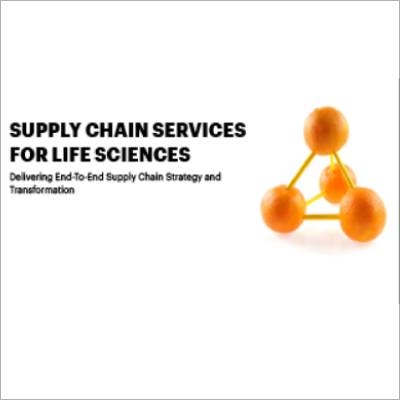
Monitoring
Monitoring is an important management technique that includes collecting, analysing, and reporting data in order to improve performance and measure progress. This involves identifying the activities and target audiences, and tracking the changes over time. This information allows managers and other stakeholders to make timely decisions about program effectiveness.
Implementation
This paper describes how to implement organizational change. Implementation can be difficult, even for small changes, but it can be successful if the changes are welcomed by the people involved. Youker's paper discusses the causes of resistance to change, and suggests ways to increase the likelihood of acceptance. It also provides an analytical model that can be used to study change resistance.
Controlling
Management has one of its primary functions. It controls management and the organizations. This function ensures that an organization's resources are efficiently used and that it meets its objectives. This function helps employees stay motivated by setting high performance standards and making sure that resources are used efficiently.
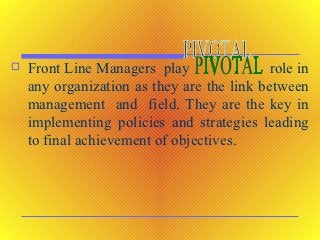
Resource optimization
Resource management refers to the balance of supply and demand in order to make a business more productive. Proper resource management will increase profitability and efficiency. This helps businesses operate more efficiently and consistently. Furthermore, resource management allows businesses to be more competitive.
FAQ
What are management concepts, you ask?
Management concepts are the principles and practices used by managers to manage people, resources. These include topics such as human resource policies and job descriptions, performance assessments, training programs and employee motivation.
What kind of people use Six Sigma?
Six Sigma is well-known to those who have worked in operations research and statistics. Anybody involved in any aspect or business can benefit.
It is a commitment-intensive task that requires strong leadership skills.
How can a manager motivate his/her staff?
Motivation refers to the desire to perform well.
Doing something that is enjoyable can help you get motivated.
You can also feel motivated by making a positive contribution to the success in the organization.
If you are a doctor and want to be one, it will likely be more rewarding to see patients than to read medical books every day.
Another source of motivation is within.
You may feel strongly that you are responsible to help others.
You might even enjoy the work.
Ask yourself why you feel so motivated.
You can then think of ways to improve your motivation.
What is Kaizen, exactly?
Kaizen is a Japanese term meaning "continuous improvement." It is a philosophy that encourages employees to constantly look for ways to improve their work environment.
Kaizen is based on the belief that every person should be able to do his or her job well.
How to manage employees effectively?
Achieving employee happiness and productivity is key to managing them effectively.
It also means having clear expectations of their behavior and keeping track of their performance.
Managers need to establish clear goals for their team and for themselves.
They should communicate clearly to staff members. They need to communicate clearly with their staff.
They will also need to keep records about their team's activities. These include:
-
What was accomplished?
-
How much work were you able to accomplish?
-
Who did it and why?
-
How did it get done?
-
Why was this done?
This information can be used for monitoring performance and evaluating results.
What is the difference between a project and a program?
A program is permanent while a project can be temporary.
A project usually has a specific goal and deadline.
It is often done in a team that reports to another.
A program will usually have a set number of goals and objectives.
It is usually done by one person.
Statistics
- This field is expected to grow about 7% by 2028, a bit faster than the national average for job growth. (wgu.edu)
- The average salary for financial advisors in 2021 is around $60,000 per year, with the top 10% of the profession making more than $111,000 per year. (wgu.edu)
- Hire the top business lawyers and save up to 60% on legal fees (upcounsel.com)
- Our program is 100% engineered for your success. (online.uc.edu)
- The BLS says that financial services jobs like banking are expected to grow 4% by 2030, about as fast as the national average. (wgu.edu)
External Links
How To
How do I do the Kaizen Method?
Kaizen means continuous improvement. This Japanese term refers to the Japanese philosophy of continuous improvement that emphasizes incremental improvements and constant improvement. It's where people work together in order to improve their processes constantly.
Kaizen is one of Lean Manufacturing's most efficient methods. Kaizen is a concept where employees in charge of the production line are required to spot problems during the manufacturing process before they become major issues. This increases the quality of products and reduces the cost.
Kaizen is an approach to making every worker aware and alert to what is happening around them. Correct any errors immediately to avoid future problems. If someone is aware of a problem at work, he/she should inform his/her manager immediately.
Kaizen is based on a few principles. Always start with the end product in mind and work our way back to the beginning. In order to improve our factory's production, we must first fix the machines producing the final product. Next, we repair the machines that make components. Then, the machines that make raw materials. Then we fix the workers, who directly work with these machines.
This approach is called 'kaizen' because it focuses on improving everything steps by step. Once we have finished fixing the factory, we return to the beginning and work until perfection.
You need to know how to measure the effectiveness of kaizen within your business. There are many ways to tell if kaizen is effective. One method is to inspect the finished products for defects. Another method is to determine how much productivity has improved since the implementation of kaizen.
If you want to find out if your kaizen is actually working, ask yourself why. You were trying to save money or obey the law? You really believed it would make you successful?
Congratulations! You're ready to start kaizen.