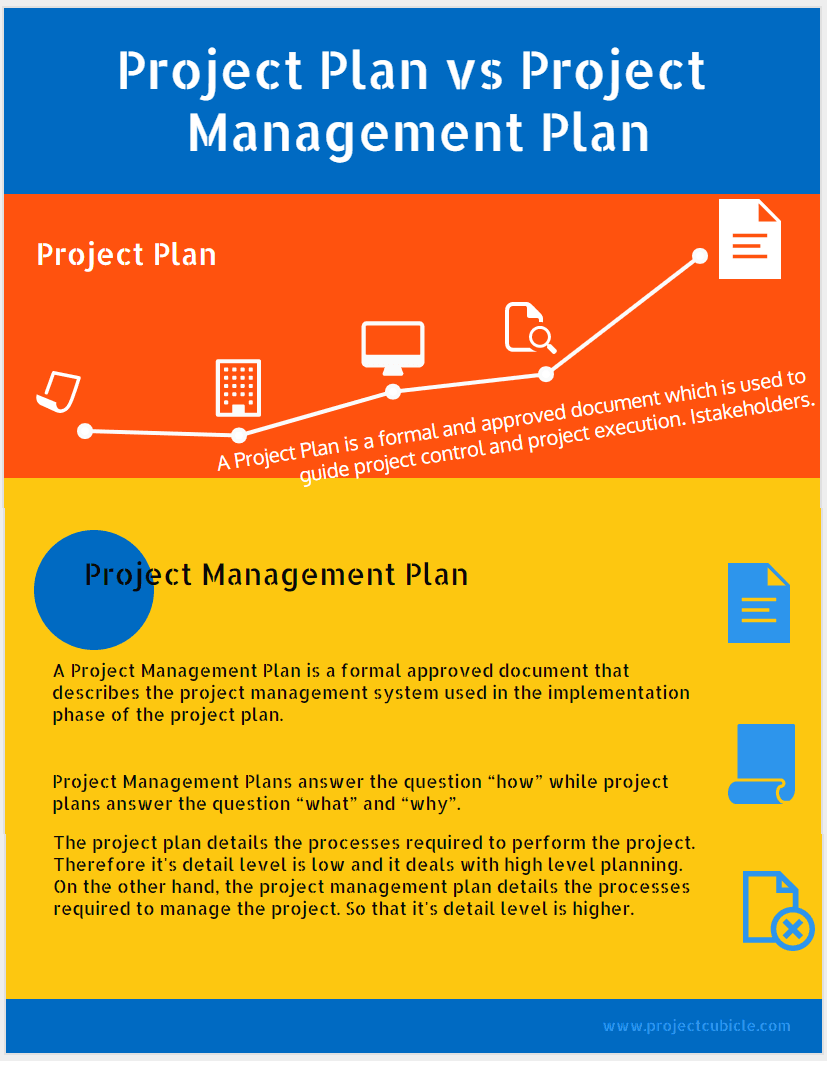
Last mile logistics are becoming more complicated as consumers are increasingly dependent on online channels to meet their needs. This article discusses the benefits and challenges of last-mile delivery, as well the costs. You'll find out how to improve your last mile delivery while maintaining operational excellence. Learn about new technologies, and how to leverage them to your benefit.
Last mile logistics challenges
Last-mile logistics can be difficult in rural areas. Delivery times can be slowened by traffic congestion and the distance between rural and urban delivery points may be many miles. With the increase in e-commerce, faster deliveries and free shipping have become more important than ever. Logistics companies have to adapt their delivery and fulfillment methods to meet the growing demands.
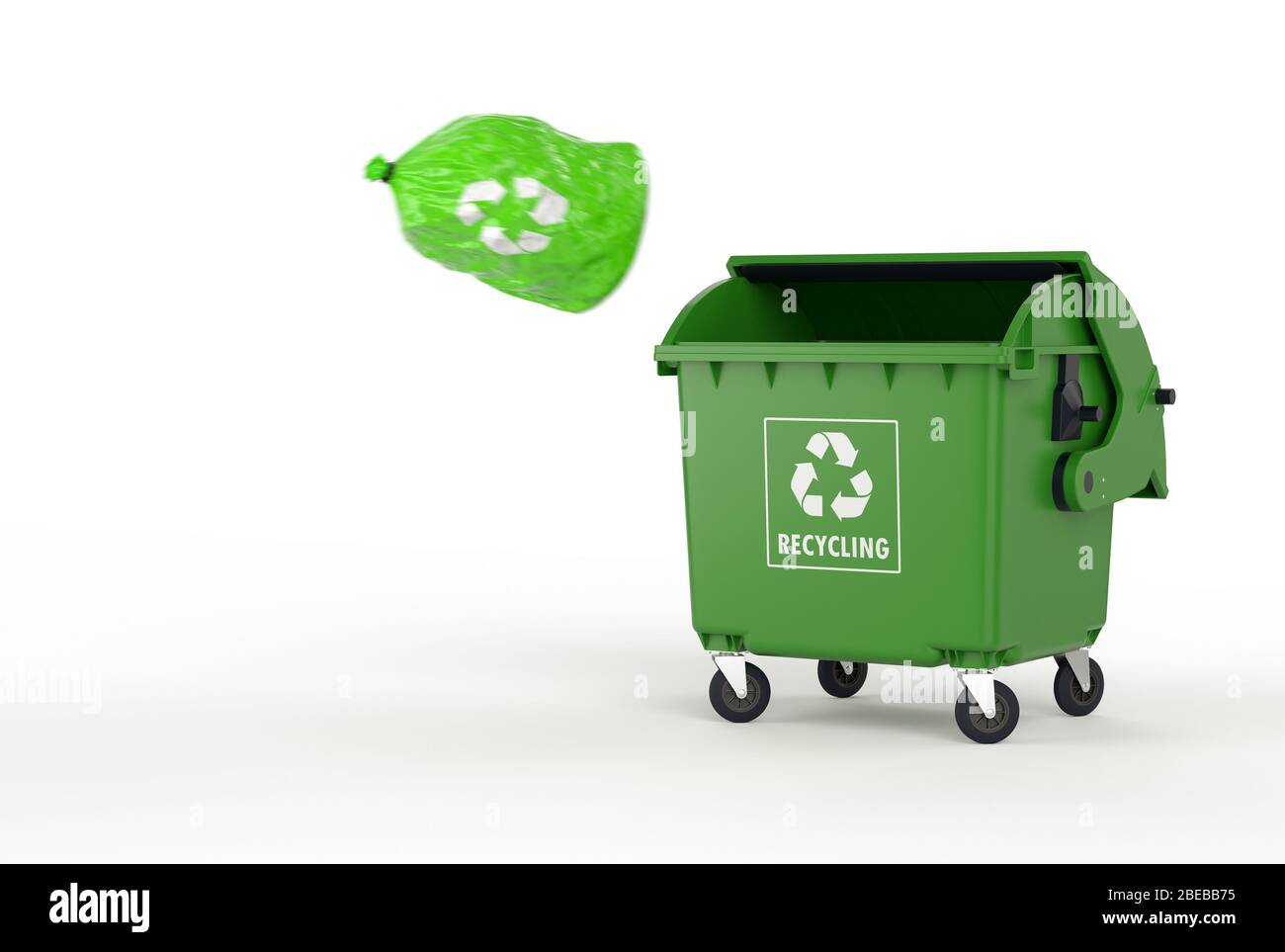
Also, the last mile distribution process is extremely unpredictable. This can lead to lengthy journeys and inadequate transportation. Companies must have contingency plans in place for any unexpected events. These factors can lead to increased costs and delays. If a driver is ill or unable deliver the product on schedule, operators must immediately dispatch a substitute driver.
Although last mile logistics can be challenging, there are many technologies that make delivery easier and faster. For example, route optimization technology, which can detect the most cost-efficient routes, will save time and money. Advanced machine-learning systems analyze road conditions, weather patterns, and traffic congestion to determine the best route. Advanced software is also available to help drivers avoid collisions and manage their routes.
Third-party logistics service providers have benefits
Third-party logistics service providers offer a number of benefits for businesses. They can scale inventory to match demand, reduce overhead when demand is low, and expand into new markets when the time is right. This allows businesses to expand their reach and improve customer service. A reliable, consistent supply chain is much cheaper than running their own logistics.
Outsourcing logistics is a great alternative because it allows the company to focus on its core business. It also helps reduce stress when handling non-core logistics. Third-party logistics providers are able to create custom shipping labels and packaging for specific orders. These services can come at a cost so plan ahead and make sure you have shipping insurance. You can protect yourself against any shipping mishaps with this insurance.
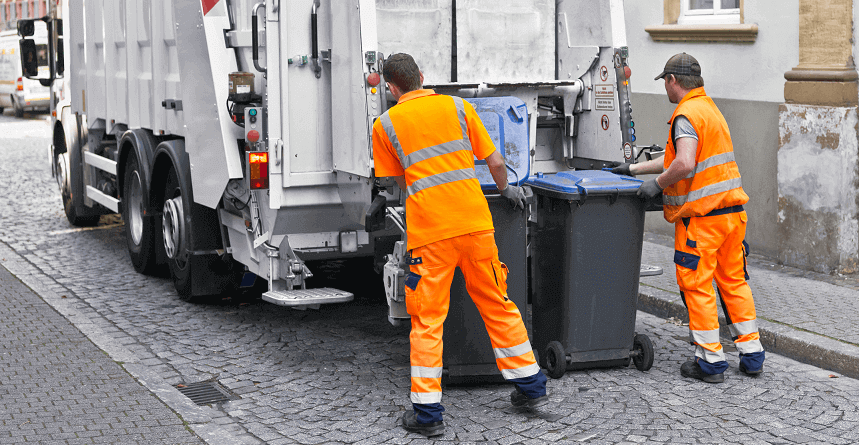
Third-party logistics companies also provide warehouse space, inventory control, and logistics technology to eCommerce businesses. These providers can also deliver goods quickly to customers, which is a huge benefit for eCommerce companies that are growing. A third-party logistics provider will also take care of stock management and replenish stock when needed. They can also update inventory if a customer returns an article.
FAQ
How does Six Sigma function?
Six Sigma uses statistical analyses to locate problems, measure them, analyze root cause, fix problems and learn from the experience.
The first step to solving the problem is to identify it.
Next, data are collected and analyzed in order to identify patterns and trends.
Then corrective actions are taken to solve the problem.
The data are then reanalyzed to see if the problem is solved.
This continues until you solve the problem.
Why does it sometimes seem so hard to make good business decisions
Businesses are complex systems, and they have many moving parts. The people who run them must juggle multiple priorities at once while also dealing with uncertainty and complexity.
The key to making good decisions is to understand how these factors affect the system as a whole.
You need to be clear about the roles and responsibilities of each system. Then, you need to think about how these pieces interact with one another.
Ask yourself if there are hidden assumptions that have influenced your behavior. If not, you might want to revisit them.
You can always ask someone for help if you still have questions after all of this. They might have different perspectives than you, and could offer insight that could help you solve your problem.
What is Kaizen?
Kaizen refers to a Japanese term that stands for "continuous improvements." It is a philosophy which encourages employees in continuously improving their work environment.
Kaizen is built on the belief that everyone should be able do their jobs well.
How can a manager enhance his/her leadership skills?
By practicing good management skills at all times.
Managers should monitor the performance and progress of their subordinates.
You should immediately take action if you see that your subordinate is not performing as well as you would like.
It is important to be able identify areas that need improvement and what can be done to improve them.
What is a fundamental management tool for decision-making?
A decision matrix is a simple but powerful tool for helping managers make decisions. They can think about all options and make informed decisions.
A decision matrix is a way of representing alternatives as rows and columns. This allows one to see how each alternative impacts other options.
The boxes on the left hand side of this matrix represent four possible choices. Each box represents an option. The top row shows the status quo (the current situation), and the bottom row shows what would happen if nothing was done at all.
The effect of selecting Option 1 is shown in the middle column. It would increase sales by $2 million to 3 million in this instance.
These are the results of selecting Options 2 or 3. These are positive changes - they increase sales by $1 million and $500 thousand respectively. However, these also involve negative consequences. Option 2 increases the cost of goods by $100,000. Option 3 decreases profits and makes them less attractive by $200,000.
The final column shows results of choosing Option 4. This results in a decrease of sales by $1,000,000
The best part of using a decision-matrix is that it doesn't require you to know which numbers belong where. The best thing about a decision matrix is that you can simply look at the cells, and immediately know whether one option is better or not.
This is because the matrix has done all the hard work. It is as simple a matter of comparing all the numbers in each cell.
Here is an example how you might use the decision matrix in your company.
Advertising is a decision that you make. You'll be able increase your monthly revenue by $5000 if you do. You'll also have additional expenses up to $10,000.
Look at the cell immediately below the one that states "Advertising" to calculate the net investment in advertising. It's $15,000. Advertising is a worthwhile investment because it has a higher return than the costs.
What is the difference between project and program?
A program is permanent while a project can be temporary.
A project has usually a specified goal and a time limit.
It is often carried out by a team of people who report back to someone else.
A program is usually defined by a set or goals.
It is usually implemented by a single person.
Statistics
- Our program is 100% engineered for your success. (online.uc.edu)
- 100% of the courses are offered online, and no campus visits are required — a big time-saver for you. (online.uc.edu)
- The BLS says that financial services jobs like banking are expected to grow 4% by 2030, about as fast as the national average. (wgu.edu)
- The average salary for financial advisors in 2021 is around $60,000 per year, with the top 10% of the profession making more than $111,000 per year. (wgu.edu)
- This field is expected to grow about 7% by 2028, a bit faster than the national average for job growth. (wgu.edu)
External Links
How To
How do you do the Kaizen method?
Kaizen means continuous improvement. The Japanese philosophy emphasizes small, incremental improvements to achieve continuous improvement. This term was created by Toyota Motor Corporation in 1950. It's where people work together in order to improve their processes constantly.
Kaizen is one the most important methods of Lean Manufacturing. The concept involves employees responsible for manufacturing identifying problems and trying to fix them before they become serious issues. This is how you can improve the quality and lower the cost.
Kaizen is an approach to making every worker aware and alert to what is happening around them. To prevent problems from happening, any problem should be addressed immediately. If someone is aware of a problem at work, he/she should inform his/her manager immediately.
There are some basic principles that we follow when doing kaizen. Always start with the end product in mind and work our way back to the beginning. For example, if we want to improve our factory, we first fix the machines that produce the final product. Next, we repair the machines that make components. Then, the machines that make raw materials. Then we fix the workers, who directly work with these machines.
This method, called 'kaizen', focuses on improving each and every step of the process. Once we have finished fixing the factory, we return to the beginning and work until perfection.
It is important to understand how to measure the effectiveness and implementation of kaizen in your company. There are several ways that you can tell if your kaizen system is working. One way is to examine the amount of defects on the final products. Another method is to determine how much productivity has improved since the implementation of kaizen.
To determine if kaizen is effective, you should ask yourself why you chose to implement kaizen. Was it just because it was the law or because you wanted to save money? Did you really believe it would lead to success?
Suppose you answered yes to any of these questions, congratulations! Now you're ready for kaizen.