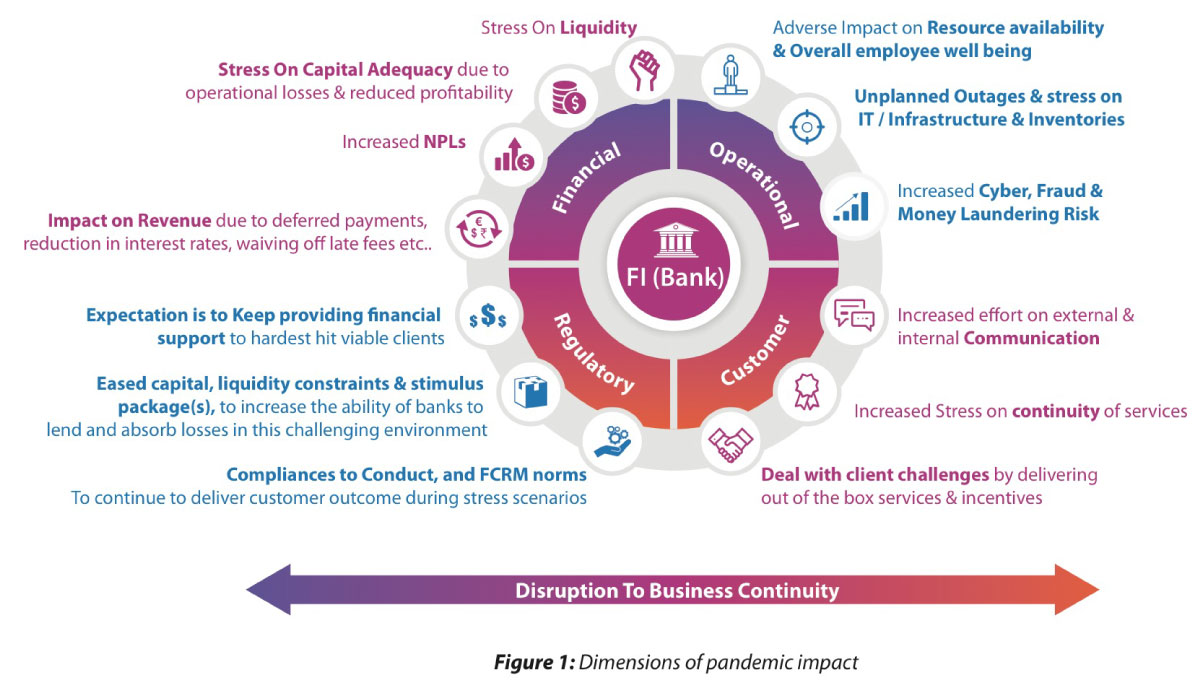
Employees should be included in the change process. Ask your employees to participate in the change process. You should consult your employees about decisions that may affect you or your department. Employees are given time to reflect on and develop new ideas in the process of change. Employees will be more inclined to accept changes if they have a say in it. It is also beneficial to include them in the design and implementation stages of the new policy. This article will focus on the four phases associated with employee change.
There are four phases to employee change
Separation is the initial phase of the change. This is a process that takes place in the 0 to three months prior to the employee leaving the company. Either the employee can initiate the separation process or the company can. The timing of the separation process will vary from company to company. However, most companies require employees to notify them at least two weeks before they intend to leave. This allows the company to prepare for the worst.
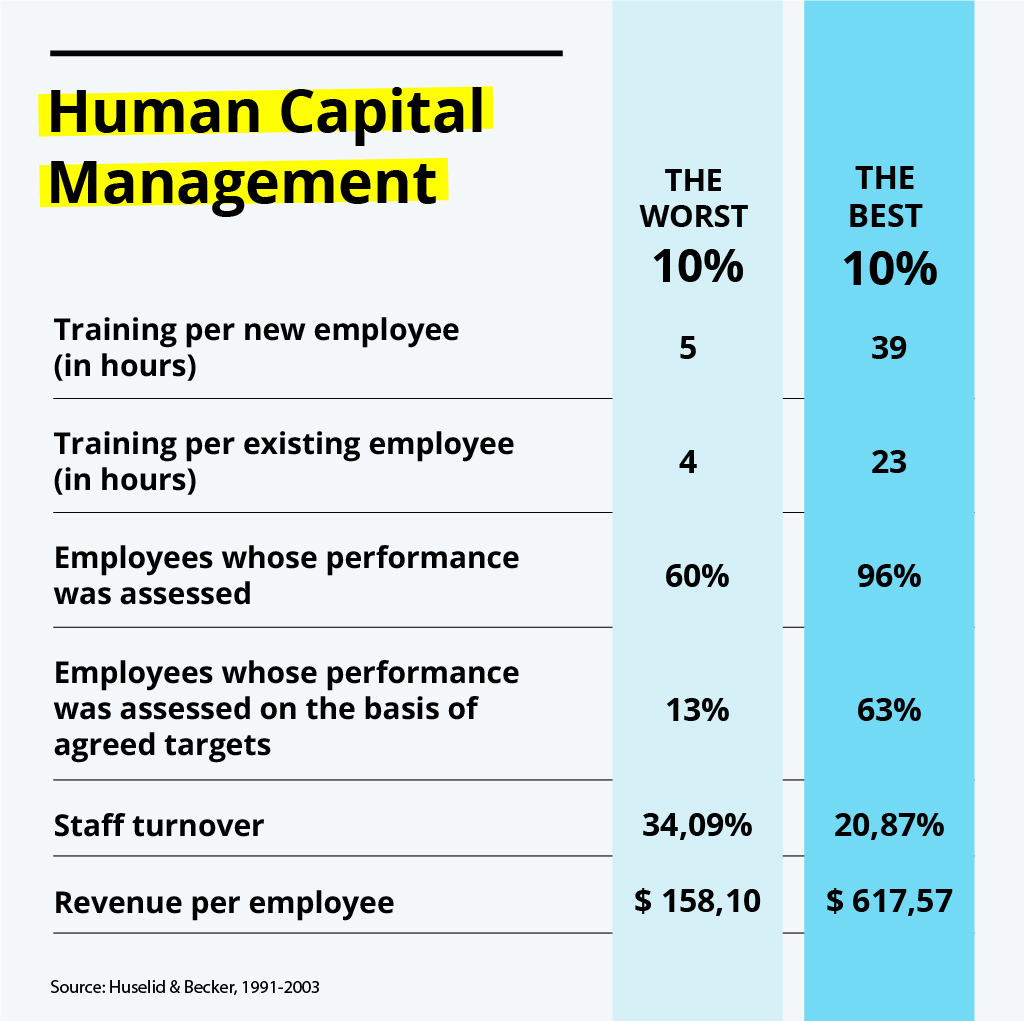
Communication
Communication of employee changes is an essential part of a successful management of change. Communicating the changes to employees in a way that encourages them to adopt new working methods is crucial. Communication must be based upon understanding employees' needs and changes. It should be a two-way process that involves frequent and consistent communication. It is also important that you communicate effectively with different audiences so that your message reaches everyone.
Empowerment
Employee engagement can be enhanced by the use of technology and group-building activities. You can foster a collaborative environment by making employees feel valued and connected to their coworkers. You can also create mentoring circles and idea exchanges to help employees connect with other departments. Empowered employees are more likely than others to solve problems and contribute to the company's success. But how do you get workers to participate?
Communication up-front
Communication upfront is the key to successful change management. Explain the change and how it will impact employees. Employees must be able to comprehend the change so that they can accept it. Communication of the changes should be clear and simple to avoid any misunderstandings. You can target different audiences to convey the right message. Communicate about your new leadership if you're changing department heads. All departments should be notified if you're restructuring your business.
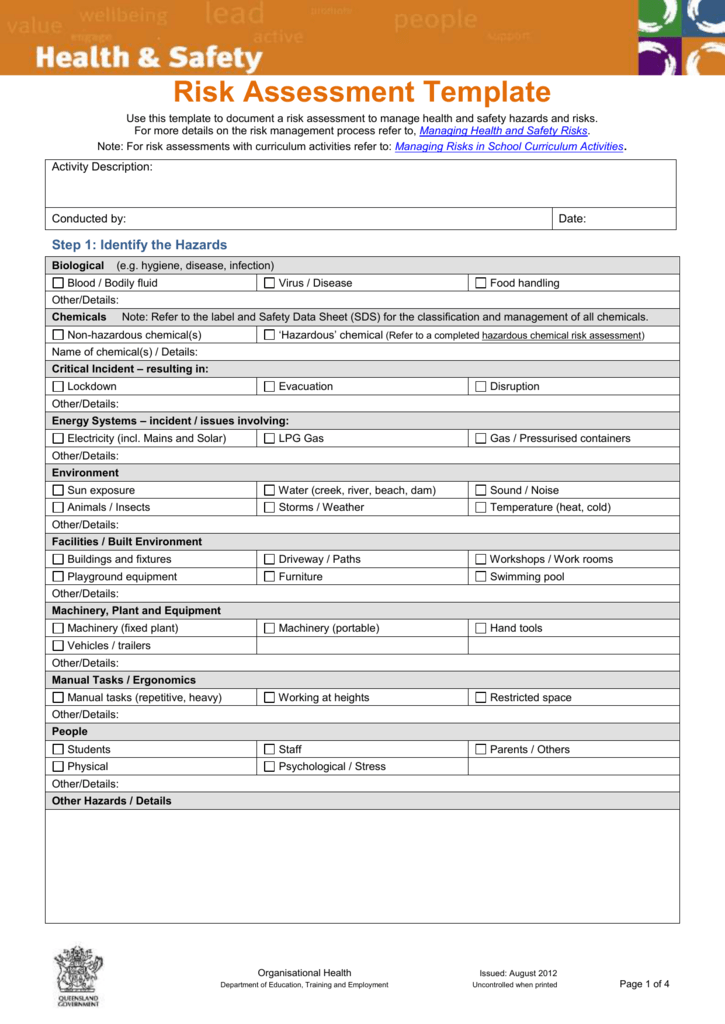
Creating a supportive work environment
Creating a supportive work environment for employee changes is one of the foundational elements of long-term employee satisfaction. It also improves the bottom line. Employees have human natures. Keeping them motivated can help them achieve their goals. However, support does not only focus on motivation. It is also about the employee’s overall health. Therefore, it is important to understand the motivations of people and how they can be supported.
FAQ
What is the difference between project and program?
A program is permanent while a project can be temporary.
A project is usually defined by a clear goal and a set deadline.
It is often carried out by a team of people who report back to someone else.
A program typically has a set goal and objective.
It is usually done by one person.
What is Kaizen?
Kaizen refers to a Japanese term that stands for "continuous improvements." It is a philosophy which encourages employees in continuously improving their work environment.
Kaizen is based on the belief that every person should be able to do his or her job well.
Why does it sometimes seem so difficult to make good business decisions?
Complex systems are often complex and have many moving parts. They require people to manage multiple priorities and deal with uncertainty and complexity.
The key to making good decisions is to understand how these factors affect the system as a whole.
You must first consider what each piece of the system does and why. You then need to consider how those individual pieces interact with each other.
It is also worth asking yourself if you have any unspoken assumptions about how you have been doing things. If they don't, you may want to reconsider them.
For help, ask someone else if you're still stumped after all the above. They may see things differently from you and have insights that could help you find a solution.
What are the 4 main functions of management?
Management is responsible to plan, organize, direct, and control people and resources. It includes the development of policies and procedures as well as setting goals.
Management assists an organization in achieving its goals by providing direction, coordination and control, leadership, motivation, supervision and training, as well as evaluation.
These are the four major functions of management:
Planning – Planning involves deciding what needs to happen.
Organizing: Organizing refers to deciding how things should work.
Directing - Directing means getting people to follow instructions.
Controlling - Controlling means ensuring that people carry out tasks according to plan.
What is the difference between Six Sigma Six Sigma and TQM?
The main difference between these two quality-management tools is that six-sigma concentrates on eliminating defects while total QM (TQM), focuses upon improving processes and reducing expenses.
Six Sigma is an approach for continuous improvement. This approach emphasizes eliminating defects through statistical methods like control charts, Pareto analysis, and p-charts.
This method has the goal to reduce variation of product output. This is achieved by identifying and addressing the root causes of problems.
Total quality management refers to the monitoring and measurement of all aspects in an organization. It also includes the training of employees to improve performance.
It is used to increase productivity.
What is the difference in leadership and management?
Leadership is about influence. Management is about controlling others.
A leader inspires his followers while a manager directs the workers.
A leader inspires others to succeed, while a manager helps workers stay on task.
A leader develops people; a manager manages people.
What are management principles?
Management concepts are the practices and principles managers use to manage people or resources. These topics include job descriptions, performance evaluations and training programs. They also cover human resource policies, job description, job descriptions, job descriptions, employee motivation, compensation systems, organizational structures, and many other topics.
Statistics
- The average salary for financial advisors in 2021 is around $60,000 per year, with the top 10% of the profession making more than $111,000 per year. (wgu.edu)
- Hire the top business lawyers and save up to 60% on legal fees (upcounsel.com)
- UpCounsel accepts only the top 5 percent of lawyers on its site. (upcounsel.com)
- As of 2020, personal bankers or tellers make an average of $32,620 per year, according to the BLS. (wgu.edu)
- Our program is 100% engineered for your success. (online.uc.edu)
External Links
How To
How is Lean Manufacturing done?
Lean Manufacturing techniques are used to reduce waste while increasing efficiency by using structured methods. They were developed in Japan by Toyota Motor Corporation (in the 1980s). The main goal was to produce products at lower costs while maintaining quality. Lean manufacturing eliminates unnecessary steps and activities from a production process. It is made up of five elements: continuous improvement, continuous improvement, just in-time, continuous change, and 5S. Pull systems involve producing only what the customer wants without any extra work. Continuous improvement refers to continuously improving existing processes. Just-in–time refers when components or materials are delivered immediately to their intended destination. Kaizen refers to continuous improvement. It is achieved through small changes that are made continuously. Finally, 5S stands for sort, set in order, shine, standardize, and sustain. These five elements are used together to ensure the best possible results.
The Lean Production System
The lean production system is based on six key concepts:
-
Flow - focuses on moving information and materials as close to customers as possible.
-
Value stream mapping- This allows you to break down each step of a process and create a flowchart detailing the entire process.
-
Five S's, Sort, Set in Order, Shine. Standardize. and Sustain.
-
Kanban - visual cues such as stickers or colored tape can be used to track inventory.
-
Theory of constraints: Identify bottlenecks and use lean tools such as kanban boards to eliminate them.
-
Just-in-time delivery - Deliver components and materials right to your point of use.
-
Continuous improvement: Make incremental improvements to the process instead of overhauling it completely.