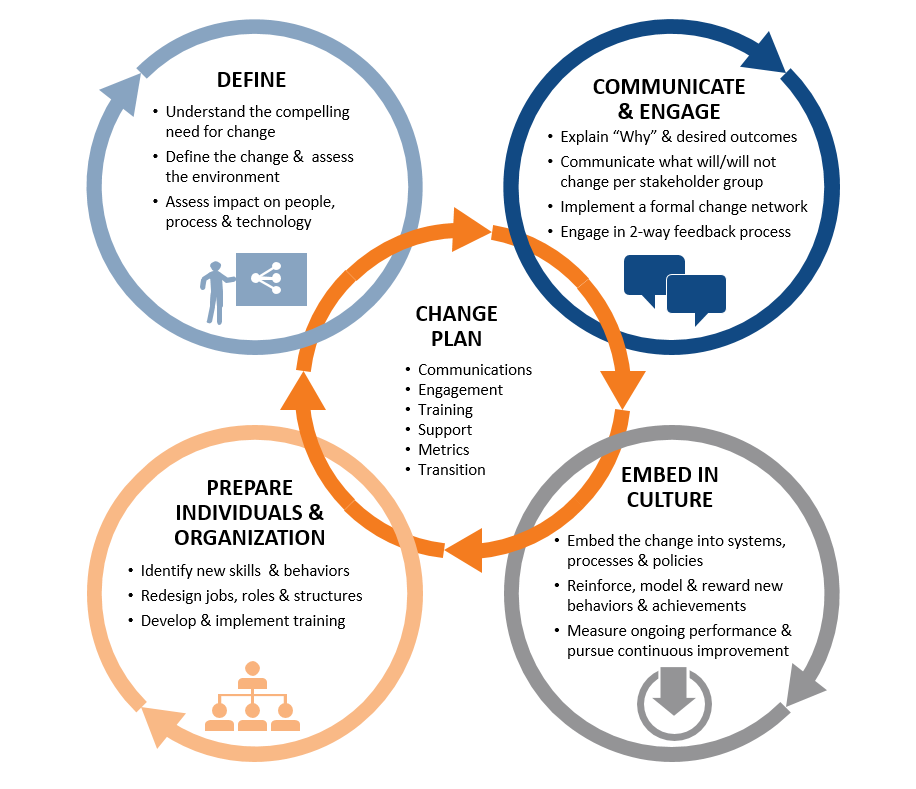
Companies are becoming more aware of the importance of supply diversity. Diverse supplier networks are becoming more important for companies. This is due to a number of factors, including competitiveness, customer sentiment, and cost control. It is more likely that smaller suppliers can tailor solutions to meet customer requirements faster than large suppliers. They can also customize solutions and lower costs.
Sources of supplier diversity
It is vital that companies seek out diverse suppliers to fulfill their needs as the number of minority-owned business grows. Companies are developing supplier diversity plans. These programs offer opportunities for minority-owned companies to supply their products or services. It is important for companies to find suppliers who share their commitment to diversity and values.
Both communities and businesses can benefit from diversity programs that focus on suppliers. Many large companies are actively promoting and requiring diversity initiatives. Target is an example. Target alone invested $1.4 billion in diversity suppliers in 2019. It has also encouraged first-tier suppliers to purchase contributions from second-tier diverse suppliers.
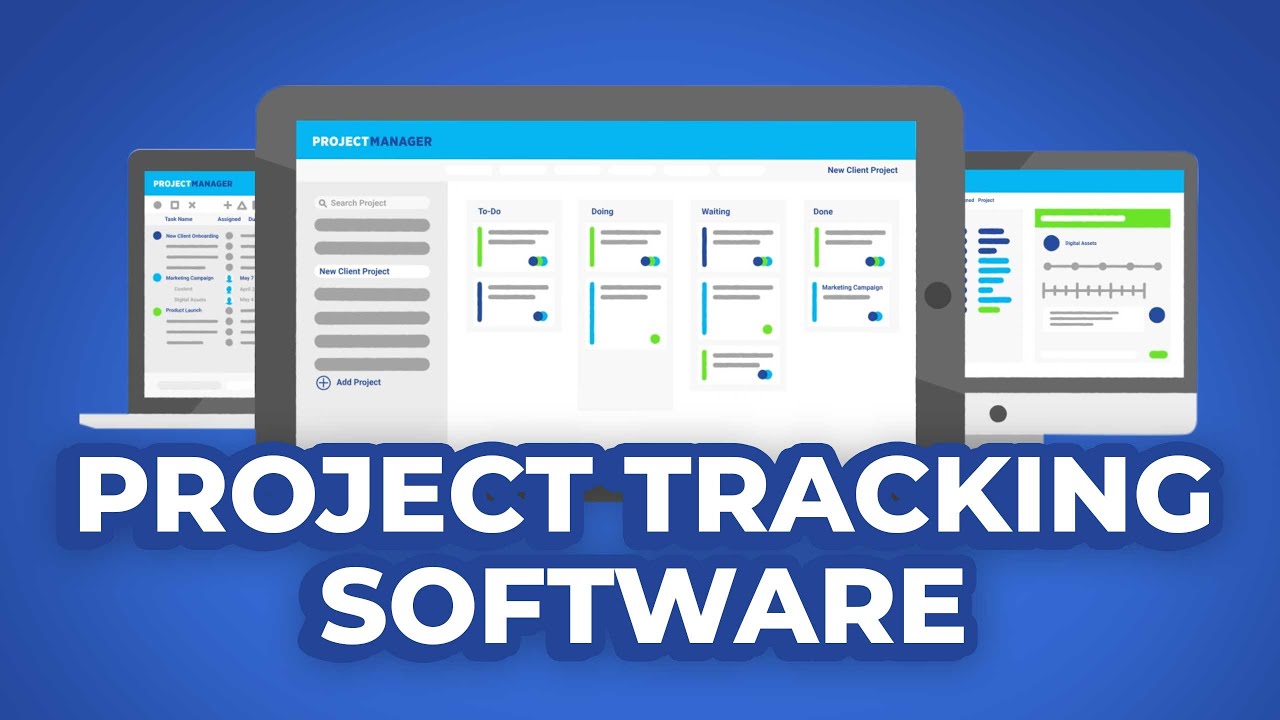
Best practices for supplier diversity
Incorporating a supplier diversity program can be a daunting task. While it can be difficult to implement, using diverse suppliers can benefit your business. These are three ways to implement supplier diversity programs effectively. First, find diverse suppliers. Start by looking for diverse vendors with which you are already doing business. Ask them to recommend different vendors. WBENC chapters are another great source for diverse suppliers.
Define clear goals. These goals should be achievable and quantifiable. For example, a goal could be to add two new diverse suppliers every year. Another goal might be to include a requirement for diverse bids in every RFP. These goals should be communicated to all employees and tracked throughout the year.
Customer sentiment drives higher supplier diversity interest
Companies are taking steps to increase supplier diversity as a result of growing customer sentiment. Coca-Cola Company for example has pledged to spend $500 Million with Black-owned Suppliers by 2020, double its previous commitment. These actions demonstrate a growing commitment to supplier diversity by large corporations. This trend is expected to continue as more people demand diverse suppliers.
Supplier diversity programs can help companies fulfill their moral obligations. It allows them to collaborate with a wider variety of suppliers while maintaining high ethical standards. UPS, for instance, started a supplier diversification program in 1992. Today, it spends $2.6B annually with diverse suppliers. There are plans to increase this figure year-over.
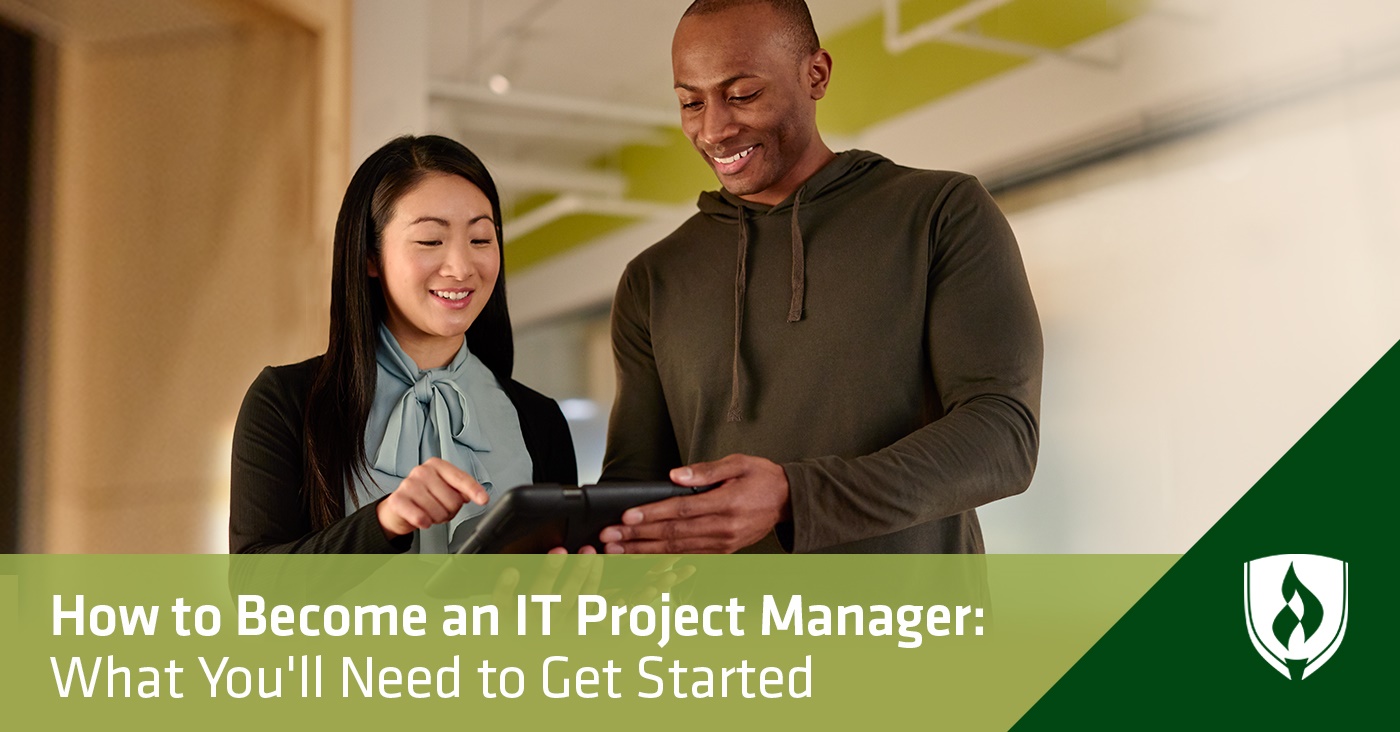
Importance of supplier diversity across the organization
In the past, supplier diversity was heavily focused on facility management, distribution, manufacturing and distribution functions. It is difficult for organizations to find ways to increase their supplier diversity beyond the existing base. Businesses can increase their potential for diversity suppliers by retooling the business strategies they use. This will increase their financial impact and allow them to increase their market share.
Diverse suppliers lower costs, innovate, and increase trust among customers. In addition, they attract top talent to work for the company. Coca-Cola found that consumers trust the brand more when it is inclusive of diverse suppliers. This led to higher brand trust, and consequently, increased sales. Target, Walmart, Target and other companies now prioritize supplier diversity.
FAQ
What is a basic management tool used in decision-making?
A decision matrix is an easy but powerful tool to aid managers in making informed decisions. It helps them to think strategically about all options.
A decision matrix represents alternatives in rows and columns. This makes it easy for you to see how each option affects other options.
In this example, there are four possible options represented by boxes on the left-hand side of the matrix. Each box represents a different option. The top row shows the status quo (the current situation), and the bottom row shows what would happen if nothing was done at all.
The middle column shows the effect of choosing Option 1. In this case, it would mean increasing sales from $2 million to $3 million.
The following columns illustrate the impact of Options 2 and 3. These are both positive changes that increase sales by $1million and $500,000. These changes can also have negative effects. Option 2 increases the cost of goods by $100,000. Option 3 decreases profits and makes them less attractive by $200,000.
The last column displays the results of selecting Option 4. This means that sales will decrease by $1 million.
The best thing about a decision matrix is the fact that you don't have to remember which numbers go with what. You can just glance at the cells and see immediately if one given choice is better.
The matrix has already done all of the work. It's simply a matter of comparing the numbers in the relevant cells.
Here's an example of how you might use a decision matrix in your business.
You need to decide whether to invest in advertising. By doing so, you can increase your revenue by $5 000 per month. However, this will mean that you'll have additional expenses of $10,000.
The net result of advertising investment can be calculated by looking at the cell below that reads "Advertising." It is 15 thousand. Advertising is a worthwhile investment because it has a higher return than the costs.
What is Kaizen?
Kaizen refers to a Japanese term that stands for "continuous improvements." It is a philosophy which encourages employees in continuously improving their work environment.
Kaizen is a belief that everyone should have the ability to do their job well.
What are some common mistakes managers make when managing people?
Sometimes, managers make their job more difficult than it is.
They may not assign enough responsibilities to staff members and provide them with inadequate support.
Additionally, many managers lack communication skills that are necessary to motivate and direct their teams.
Some managers set unrealistic expectations for their staff.
Managers may attempt to solve all problems themselves, rather than delegating it to others.
What is TQM and how can it help you?
The industrial revolution led to the birth and growth of the quality movement. Manufacturing companies realized they couldn't compete solely on price. They needed to improve quality and efficiency if they were going to remain competitive.
In response to this need for improvement, management developed Total Quality Management (TQM), which focused on improving all aspects of an organization's performance. It involved continuous improvement, employee participation, and customer satisfaction.
What are the 3 main management styles?
There are three types of management: participative, laissez faire, and authoritarian. Each style is unique and has its strengths as well as weaknesses. Which style do you prefer? Why?
Authoritarian – The leader sets a direction and expects everyone follows it. This style works best in large organizations that are stable and well-organized.
Laissez-faire – The leader gives each individual the freedom to make decisions for themselves. This style is best when the organization has a small but dynamic group.
Participative - The leader listens to ideas and suggestions from everyone. This style works best in smaller organizations where everyone feels valued.
What is the best way to motivate your employees as a manager?
Motivation can be defined as the desire to achieve success.
Engaging in something fun can be a great way to get motivated.
You can also be motivated by the idea of making a difference to the success and growth of your organization.
You might find it more rewarding to treat patients than to study medical books if you plan to become a doctor.
Another type of motivation comes from within.
You might feel a strong sense for responsibility and want to help others.
You might even enjoy the work.
If you don’t feel motivated, find out why.
Then try to think about ways to change your situation to be more motivated.
Statistics
- Our program is 100% engineered for your success. (online.uc.edu)
- The BLS says that financial services jobs like banking are expected to grow 4% by 2030, about as fast as the national average. (wgu.edu)
- As of 2020, personal bankers or tellers make an average of $32,620 per year, according to the BLS. (wgu.edu)
- Hire the top business lawyers and save up to 60% on legal fees (upcounsel.com)
- The average salary for financial advisors in 2021 is around $60,000 per year, with the top 10% of the profession making more than $111,000 per year. (wgu.edu)
External Links
How To
How can Lean Manufacturing be done?
Lean Manufacturing uses structured methods to reduce waste, increase efficiency and reduce waste. They were created in Japan by Toyota Motor Corporation during the 1980s. The aim was to produce better quality products at lower costs. Lean manufacturing seeks to eliminate unnecessary steps and activities in the production process. It has five components: continuous improvement and pull systems; just-in time; continuous change; and kaizen (continuous innovation). It is a system that produces only the product the customer requests without additional work. Continuous improvement is the continuous improvement of existing processes. Just-in time refers to components and materials being delivered right at the place they are needed. Kaizen means continuous improvement, which is achieved by implementing small changes continuously. Fifth, the 5S stand for sort, set up in order to shine, standardize, maintain, and standardize. These five elements are combined to give you the best possible results.
Lean Production System
Six key concepts underlie the lean production system.
-
Flow - focuses on moving information and materials as close to customers as possible.
-
Value stream mapping- This allows you to break down each step of a process and create a flowchart detailing the entire process.
-
Five S’s - Sorted, In Order. Shine. Standardize. And Sustain.
-
Kanban - use visual signals such as colored tape, stickers, or other visual cues to keep track of inventory;
-
Theory of constraints - identify bottlenecks in the process and eliminate them using lean tools like kanban boards;
-
Just-intime - Order components and materials at your location right on the spot.
-
Continuous improvement is making incremental improvements to your process, rather than trying to overhaul it all at once.