
Time management is about planning ahead and taking control of your time. Time management is about increasing your efficiency, productivity, and effectiveness. You can do this by planning your day ahead of time, identifying priorities, and setting deadlines. In this article, I'll describe the various methods you can use to improve your time management. Before I start, I'd like to share with my readers a few of the time-management tips I use.
Plan ahead
Planning is crucial to time management. Plan not only for the next week, but also for the days before. This will allow you to divide your tasks into day segments and calculate how long it will take. Every task should also have deadlines. Once you've created your plan, you can then stick to it and make progress in your life. To get started, here are some tips:
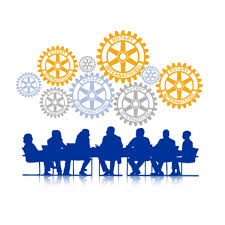
Prioritizing
Succession requires a system to prioritize tasks. They have a system for prioritizing tasks. In contrast, unsuccessful people don't prioritize tasks and waste time procrastinating. They instead miss opportunities to learn new things, make new friends, and meet new people. Prioritizing your tasks will increase your productivity, and you'll spend less time doing the ones that aren’t important.
Setting deadlines
You can use time management tips like setting deadlines for different tasks. Setting a deadline helps you stay on track and will prevent you from becoming distracted by overanalyzing the work. A realistic deadline can improve your mood. It is easier to keep your deadlines on track and accomplish your tasks on time. By setting deadlines early, you will give yourself enough time for your task.
Tidying up
One of the most effective time management techniques is tidying up your workspace. When you do this, you will minimise the number of clean-up tasks you have to do each day. This can be achieved by cleaning your workspace as you go. Keeping your workspace tidy will also improve your motivation and self-esteem. A neat workspace will inspire you to maintain your systems in order to increase productivity. Todoist is a tool that allows you to keep track and manage your tasks.
Reward Points
A great way to motivate your children to adhere to a routine is to give them rewards. It's not necessary to purchase toys; praise, games, or family time can serve as great time management rewards. You can decide what rewards you want as a whole family and think about what your child would enjoy. By setting time management reward, you can turn family time in to a fun activity everyone can enjoy. Here are some great rewards for children who manage their time well.
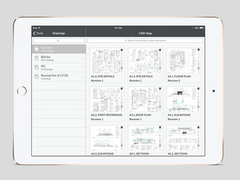
Take a vacation
If you have a packed calendar, taking a break is necessary for time management. Regular timeouts are a great way to improve your focus and productivity. Depending on your health and workload, breaks can be scheduled at regular intervals. Tony Schwartz founded the Energy Project and calls this "pulse/pause" work-break pattern. Kevin Kruse, the author of 15 Secrets to Successful Time Management, believes it is important to take frequent breaks.
FAQ
What are management principles?
Management concepts are the fundamental principles and practices that managers use when managing people and their resources. They cover topics like job descriptions (job descriptions), performance evaluations, training programmes, employee motivation and compensation systems.
What are the main management skills?
Business owners need to have management skills, no matter how small or large they may be. These skills include the ability manage people, finances and resources as well as other factors.
Management Skills are also needed when you're setting goals and objectives, planning strategies, leading teams, motivating employees, resolving problems, creating policies and procedures, and managing change.
You can see that there are many managerial duties.
What role should a manager play within a company
The role of a manager varies from one industry to another.
In general, a manager controls the day-to-day operations of a company.
He/she will ensure that the company fulfills its financial obligations.
He/she is responsible for ensuring that employees comply with all regulations and follow quality standards.
He/she plans new products and services and oversees marketing campaigns.
What is the difference between management and leadership?
Leadership is about being a leader. Management is about controlling others.
A leader inspires followers while a manager directs workers.
A leader inspires others to succeed, while a manager helps workers stay on task.
A leader develops people; a manager manages people.
Statistics
- Our program is 100% engineered for your success. (online.uc.edu)
- This field is expected to grow about 7% by 2028, a bit faster than the national average for job growth. (wgu.edu)
- 100% of the courses are offered online, and no campus visits are required — a big time-saver for you. (online.uc.edu)
- The profession is expected to grow 7% by 2028, a bit faster than the national average. (wgu.edu)
- Your choice in Step 5 may very likely be the same or similar to the alternative you placed at the top of your list at the end of Step 4. (umassd.edu)
External Links
How To
How does Lean Manufacturing work?
Lean Manufacturing uses structured methods to reduce waste, increase efficiency and reduce waste. They were developed in Japan by Toyota Motor Corporation (in the 1980s). The primary goal was to make products with lower costs and maintain high quality. Lean manufacturing focuses on eliminating unnecessary steps and activities from the production process. It includes five main elements: pull systems (continuous improvement), continuous improvement (just-in-time), kaizen (5S), and continuous change (continuous changes). Pull systems are able to produce exactly what the customer requires without extra work. Continuous improvement is constantly improving upon existing processes. Just-in time refers to components and materials being delivered right at the place they are needed. Kaizen refers to continuous improvement. It is achieved through small changes that are made continuously. Fifth, the 5S stand for sort, set up in order to shine, standardize, maintain, and standardize. These five elements are used together to ensure the best possible results.
Lean Production System
Six key concepts form the foundation of the lean production system:
-
Flow - focus on moving material and information as close to customers as possible;
-
Value stream mapping is the ability to divide a process into smaller tasks, and then create a flowchart that shows the entire process.
-
Five S's - Sort, Set In Order, Shine, Standardize, and Sustain;
-
Kanban – visual signals like colored tape, stickers or other visual cues are used to keep track inventory.
-
Theory of constraints: Identify bottlenecks and use lean tools such as kanban boards to eliminate them.
-
Just-in time - Get components and materials delivered right at the point of usage;
-
Continuous improvement - incremental improvements are made to the process, not a complete overhaul.