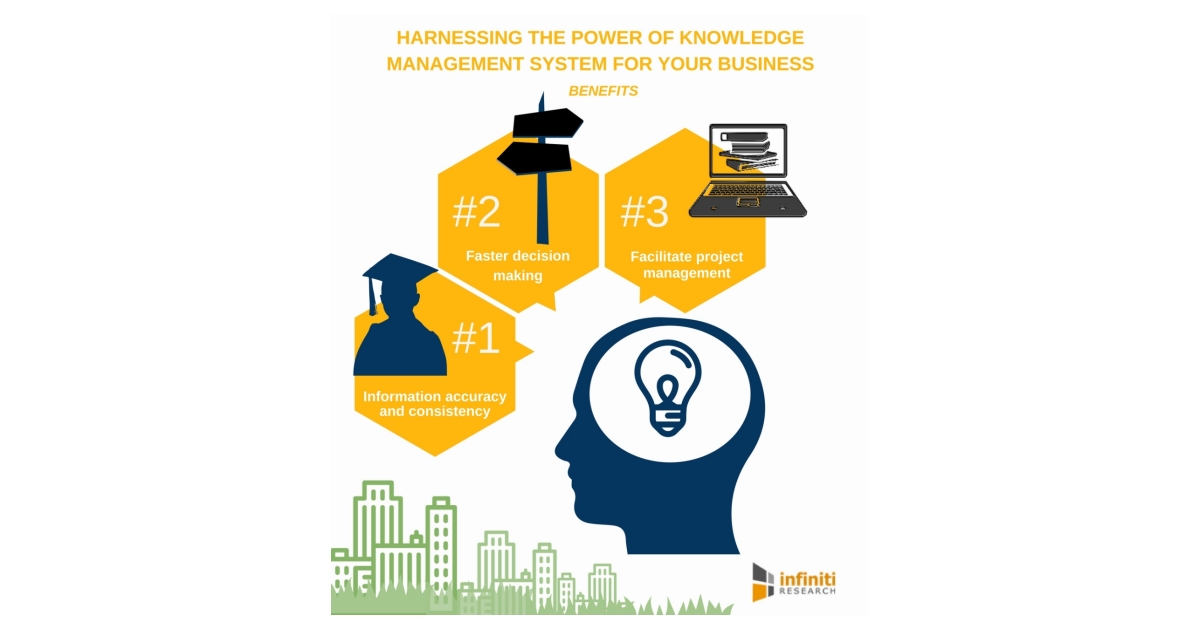
A company must meet 14 elements to be considered a PSM programme. These elements include Process hazard analyses, Permissible exposure limits, Physical data, and Corrosivity data. These elements are essential for the success of a PSM plan. These elements will ensure that your PSM program is compliant. These elements are described and illustrated in the following sections.
Analyses of Process Hazards
A process hazard assessment is an essential component of a safety management plan. It helps to identify potential hazards, and the consequences of their failure. An expert team of employees should perform this analysis. It will include human factors and previous incidents and reviews the siting of the facility. Once the analysis is complete, it must be updated at least every five years. The hazard analysis process must be carried out and maintained as part of a safety-management system.
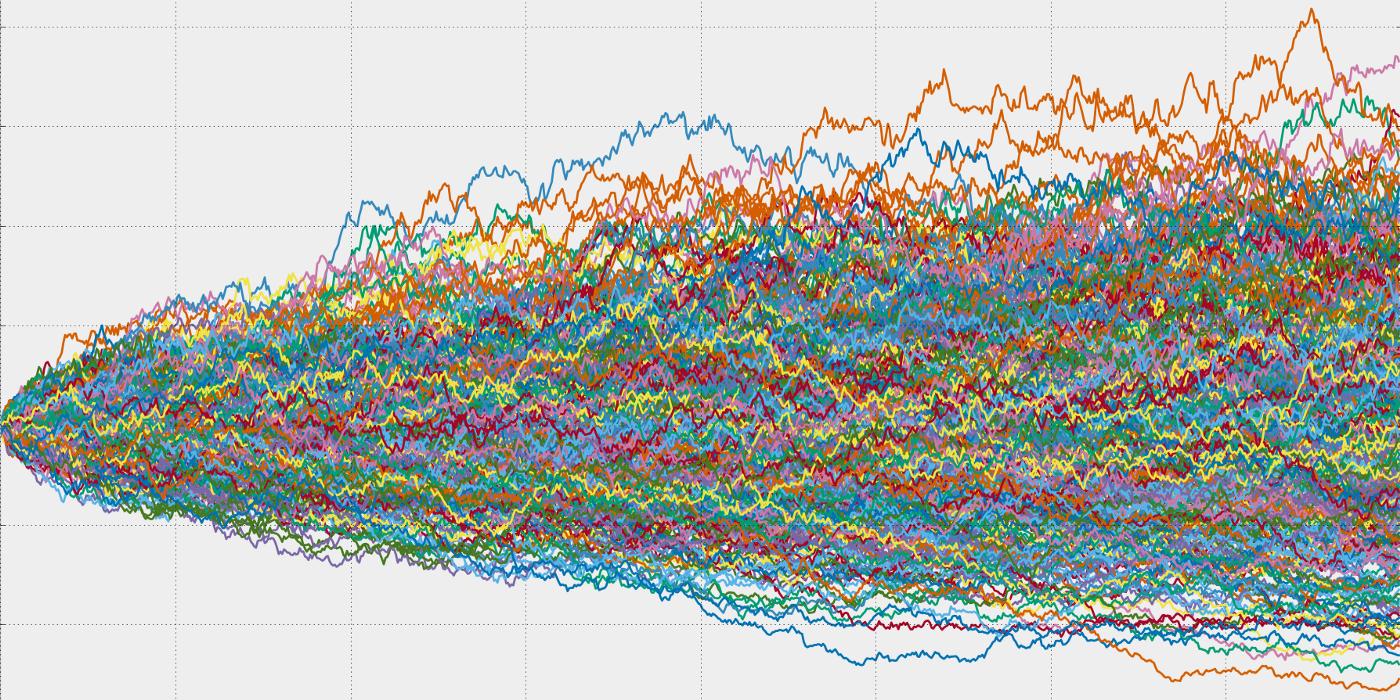
Permissible exposure limits
The OSHA Process Safety Management standard is a set of standards for processes that involve chemicals, gases, or liquids that are classified as hazardous. The standard applies to businesses that produce or process hazardous chemicals. It does not apply to hydrocarbon fuels used solely for workplace use or to retail or oil and gas well drilling. Similarly, it does not apply to remote or normally unoccupied facilities.
Physical data
PSM involves the assessment and management of hazardous products and materials. This includes knowing how to transport, handle, and store hazardous substances safely. This can result in less product waste, and fewer workplace accidents. It simplifies decision-making and makes organizations safer and more productive. PSM is an essential part of a safe workplace. It can help companies prevent costly medical emergencies and save money.
Corrosivity data
The PSM standard sets out requirements for how chemicals and other substances should be stored and handled. The PSM requires periodic compliance audits and includes requirements for emergency plans and permit system. PSM-compliant workplaces will provide safety and protection for employees, no matter how hazardous your organization's production processes are.
Data on thermal stability
OSHA has established a standard that allows for the collection and reporting PSM thermal stability data. The program will ensure that researchers are aware of possible hazards and minimize the effects of accidental release. It will be updated regularly to reflect new research tasks. It will be available to all employees. The PSM program includes information on toxicity, reactivity, corrosivity, and physical properties.
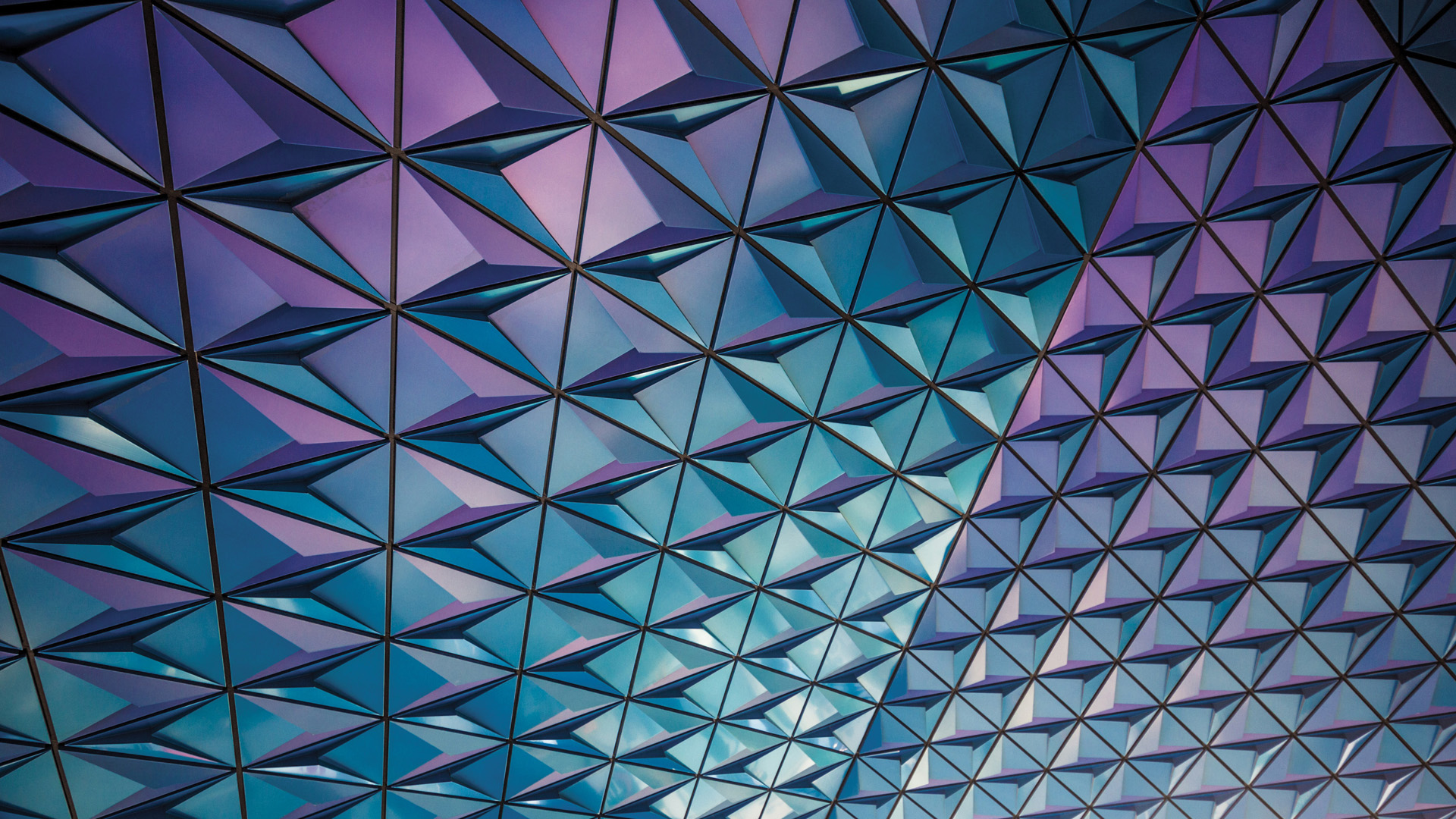
Employee participation clause
Process Safety Management is an analytical system that prevents process accidents from highly hazardous chemicals (HHC). It is an important step in improving process safety and must be implemented at all levels, including maintenance and production. It includes 14 elements, which should all be implemented, as well as employee participation clauses. Here are some examples of elements and requirements.
FAQ
What are the most common errors made by managers?
Sometimes managers make their job harder than they need to.
They may not assign enough responsibilities to staff members and provide them with inadequate support.
A majority of managers lack the communication skills needed to motivate their team and lead them.
Managers can set unrealistic expectations for their employees.
Managers may choose to solve every problem all by themselves, instead of delegating to others.
What is the main difference between Six Sigma Six Sigma TQM and Six Sigma Six Sigma?
The main difference between these two quality management tools is that six sigma focuses on eliminating defects while total quality management (TQM) focuses on improving processes and reducing costs.
Six Sigma is an approach for continuous improvement. This method emphasizes eliminating defects using statistical methods such p-charts, control charts, and Pareto analysis.
This method aims to reduce variation in product production. This is achieved by identifying and addressing the root causes of problems.
Total quality management involves measuring and monitoring all aspects of the organization. This includes training employees to improve their performance.
It is frequently used as an approach to increasing productivity.
How can a manager enhance his/her leadership skills?
You can improve your management skills by practicing them at all times.
Managers need to monitor their subordinates' performance.
You must act quickly if you notice that your subordinate isn’t performing to their standards.
You should be able pinpoint what needs to improve and how to fix it.
What is TQM?
When manufacturing companies realized that price was not enough to compete, the industrial revolution brought about the quality movement. They needed to improve the quality and efficiency of their products if they were to be competitive.
In response to this need for improvement, management developed Total Quality Management (TQM), which focused on improving all aspects of an organization's performance. It included continuous improvement, employee involvement and customer satisfaction.
What is a simple management tool that aids in decision-making and decision making?
A decision matrix can be a simple, but effective tool to assist managers in making decisions. They can think about all options and make informed decisions.
A decision matrix is a way of representing alternatives as rows and columns. This allows one to see how each alternative impacts other options.
The boxes on the left hand side of this matrix represent four possible choices. Each box represents an option. The top row shows the status quo (the current situation), and the bottom row shows what would happen if nothing was done at all.
The middle column shows the effect of choosing Option 1. In this case, it would mean increasing sales from $2 million to $3 million.
The effects of options 2 and 3 are shown in the next columns. These are both positive changes that increase sales by $1million and $500,000. But, they also have some negative consequences. For instance, Option 2 increases cost by $100 thousand while Option 3 reduces profits by $200 thousand.
The final column shows the results for Option 4. This results in a decrease of sales by $1,000,000
A decision matrix has the advantage that you don’t have to remember where numbers belong. You can just glance at the cells and see immediately if one given choice is better.
The matrix has already done all of the work. It's simply a matter of comparing the numbers in the relevant cells.
Here is an example how you might use the decision matrix in your company.
You need to decide whether to invest in advertising. If you do this, you will be able to increase revenue by $5000 per month. You will still have to pay $10000 per month in additional expenses.
By looking at the cell just below "Advertising", the net result can be calculated as $15 thousand. Therefore, you should choose to invest in advertising since it is worth more than the cost involved.
What do we mean when we say "project management"?
We mean managing the activities involved in carrying out a project.
We include defining the scope of the project, identifying the requirements, preparing the budget, organizing the project team, scheduling the work, monitoring progress, evaluating results, and closing down the project.
Statistics
- As of 2020, personal bankers or tellers make an average of $32,620 per year, according to the BLS. (wgu.edu)
- The average salary for financial advisors in 2021 is around $60,000 per year, with the top 10% of the profession making more than $111,000 per year. (wgu.edu)
- Your choice in Step 5 may very likely be the same or similar to the alternative you placed at the top of your list at the end of Step 4. (umassd.edu)
- Our program is 100% engineered for your success. (online.uc.edu)
- Hire the top business lawyers and save up to 60% on legal fees (upcounsel.com)
External Links
How To
How can you apply 5S to your office?
Your workplace will be more efficient if you organize it properly. A clean desk, a tidy room, and a well-organized workspace help everyone stay productive. To ensure space is efficiently used, the five S's (Sort Shine, Sweep Separate, Store and Separate) are all essential. These steps will be covered one-by-one and how they can work in any kind of setting.
-
Sort.Put away papers and clutter so that you don't waste valuable time searching for something that you know is there. This means putting things where you use them most often. If you find yourself frequently referring to something, place it near the location where you do your research. It is important to consider whether or not you actually need something. If it does not serve a purpose, get rid of it.
-
Shine. Anything that could cause harm or damage to others should be thrown out. Find a safe way to store pens that you don't want anyone else to see. A pen holder is a great investment as you won't lose your pens.
-
Sweep. You should clean your surfaces often to prevent dirt and grime from building up. A dusting machine is a great investment to keep your surfaces clean. You can even set aside a specific area for sweeping and dusting to keep your workstation looking tidy.
-
Separate. You will save time when disposing of trash by separating it into separate bins. Trash cans are usually placed strategically throughout the office so that you can easily throw out the garbage without searching for it. Make sure that you take advantage of this location by placing trash bags next to each bin so that you don't have to dig through piles of trash to find what you need.