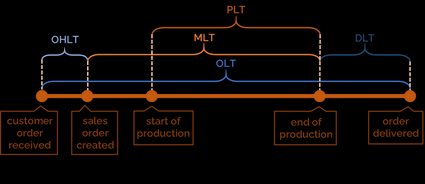
Accenture is the world's largest supply chain consultancy and has acquired GRA, a logistics and supply chains consulting firm. Accenture offers a combination of these services to its clients, helping them meet the growing demands of today's supply chain. Accenture's supply chains experts work with clients to deliver positive customer experiences. Accenture acquired Blue Horseshoe Group in addition to Xoomworks Group. We will discuss the importance supply chain capabilities for modern business strategies.
Accenture's Supply Chain Strategy
Accenture recently completed a global supply chain strategy to MedShare International, an Atlanta-based charity that distributes medical supplies in developing countries. The strategy targeted optimizing the supply chain, including sourcing and procuring, warehouse operations, and customer experience. It will be implemented over several decades with a view towards boosting the organization’s bottom line. MedShare has been able to achieve its mission, which is to address the global healthcare crisis by providing assistance for the most vulnerable people around the globe, through the results of this study.
Organizations must redesign their supply chains to meet consumers' needs. Customers can be personalised experiences and products created by using customer-centricity. These networks are vital for both a company's bottom line as well as the global economy. Accenture's supply-chain strategy allows organizations to accelerate their journey towards customer-centricity through targeted commercial interventions and cash flow.
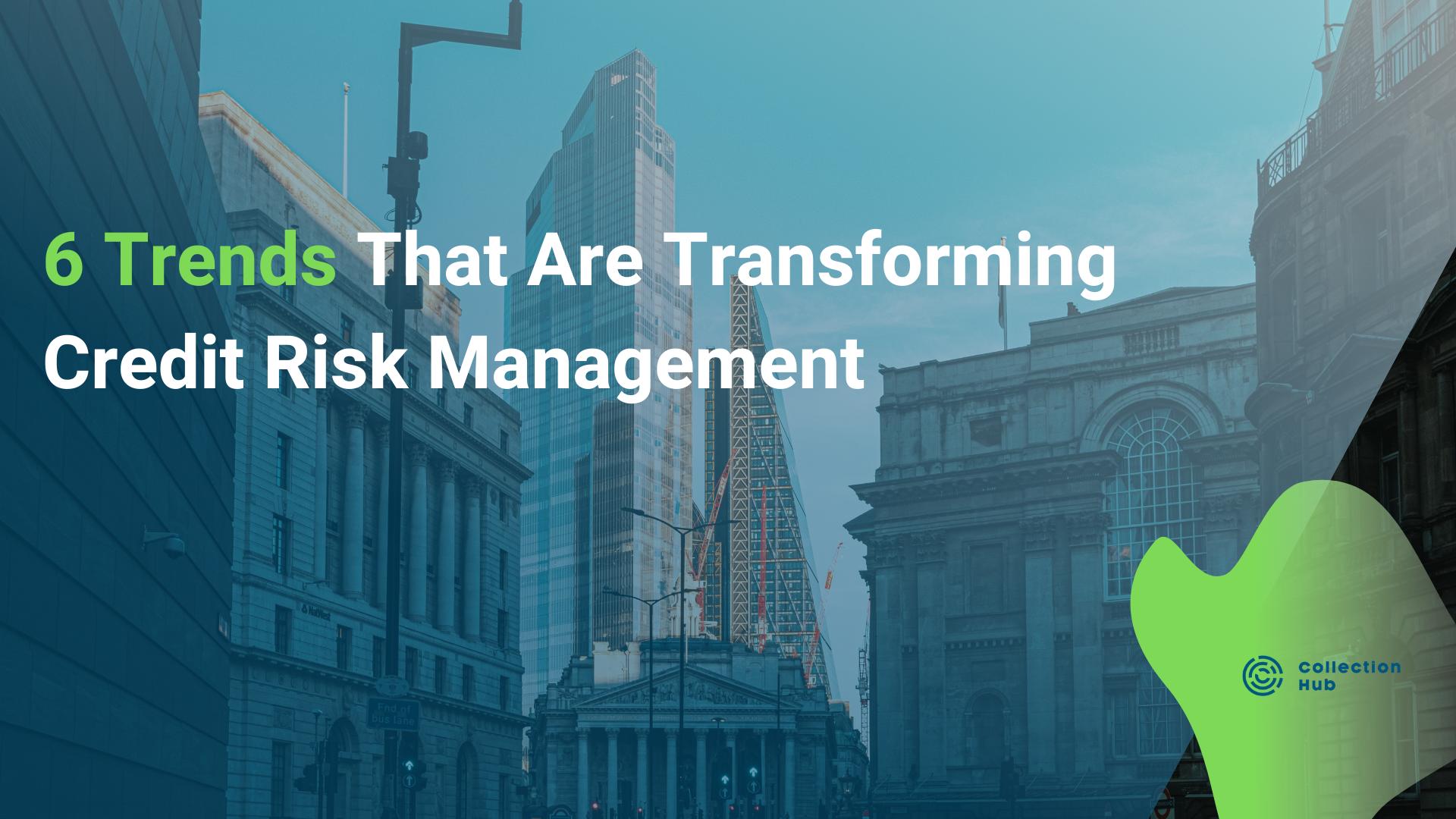
Accenture acquires Alfa Consulting
In a recent acquisition, Accenture has acquired a consulting company that specializes in operations strategy for capital-intensive industries. Alfa, which is based Spain, has offices throughout Spain, Portugal, Spain, as well as Mexico. Alfa's main focus is on supply chains management and analytical models. This includes tech, energy and capital goods. Accenture's global expansion will bring Alfa to clients' supply chain operations, allowing them to be more efficient and sustainable.
Accenture's Supply Chain & Operations will include Alfa Consulting. This area helps clients to achieve customer-centric supply chains segmentation and sourcing transformations. Accenture will continue to offer its value-based workforce planning and maintenance practices in addition to Alfa's supply chains consulting services. Accenture will have greater supply chain capabilities across Iberia with this acquisition. And while Accenture has a strong presence in the U.S., Alfa is still a significant player in Europe.
Accenture's acquisition by Xoomworks Group
Accenture announced its acquisition of Xoomworks a technology and innovative consultancy. Accenture's Closed Loop Spend Administration capabilities are strengthened by the acquisition of Xoomworks, a technology and innovation consultancy. Clients have unparalleled visibility into all price categories and insights through this system. It enhances the ecosystem partners' expertise in digital innovation management. Accenture will add a new talent source to its global talent pool through this acquisition. It employs more than 62,000 people around the globe, making it one of the most important consulting firms in the country.
The Xoomworks Group was founded in 2000, and operates two businesses, Xoomworks Procurement and Xoomworks Technology. The company's Procurement division offers digital procurement and sourcing solutions for clients across the industry. Xoomworks Procurement is home to more than 250 employees in the UK and France. Accenture states that the acquisition will improve its Closed Loop Spend Management capabilities. Clients can achieve significant, long-term cost savings.
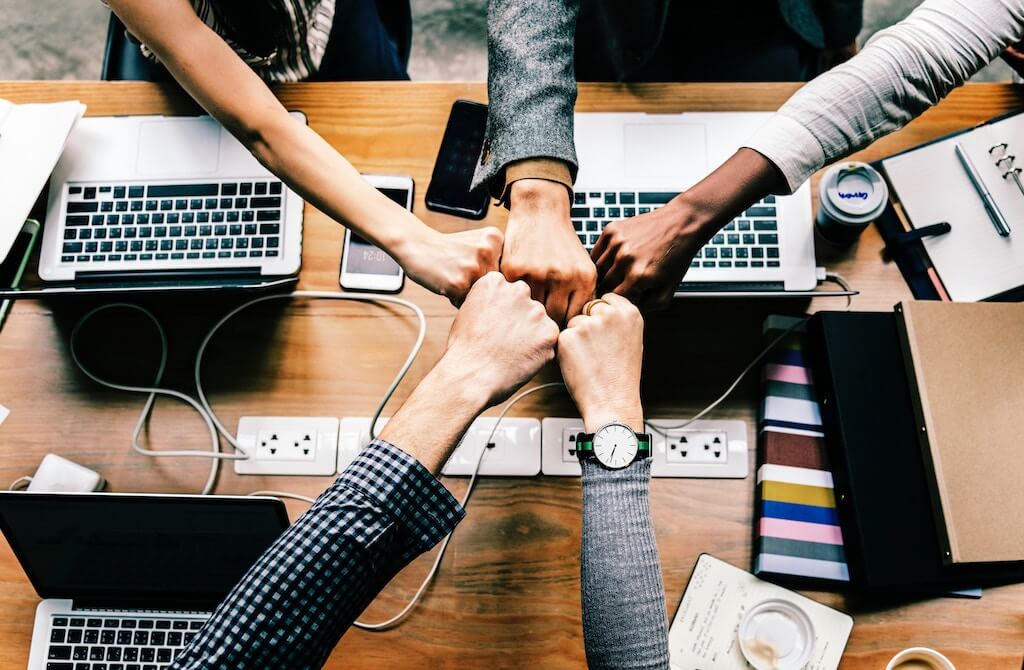
Accenture buys Blue Horseshoe
Accenture recently announced the acquisition of Blue Horseshoe, a supply chain strategy and integration company. Founded in 2001, Blue Horseshoe helps clients in a variety of industries define their enterprise strategies, connect applications, and optimize their supply chain operations. The combined company, which has offices in North Carolina and Ohio, will offer a variety of supply chain solutions. You can read on for more information about the acquisition.
The acquisition is the latest in a string of recent acquisitions by Accenture. Accenture has been increasingly active in M&A, buying dozens of companies every year. Accenture had previously purchased data analytics companies as well as ad agencies. Recently, however, the company bought LEXTA, a strategic IT consultant. This is the company's third largest deal in its history.
FAQ
What is the difference of a program and project?
A project is temporary while a programme is permanent.
A project has usually a specified goal and a time limit.
This is often done by a group of people who report to one another.
A program typically has a set goal and objective.
It is often done by one person.
Six Sigma is so popular.
Six Sigma is easy to use and can lead to significant improvements. Six Sigma provides a framework to measure improvements and allows companies to focus on the most important things.
What can a manager do to improve his/her management skillset?
Good management skills are essential for success.
Managers should monitor the performance and progress of their subordinates.
If you notice your subordinate isn't performing up to par, you must take action quickly.
You must be able to spot what is lacking and how you can improve it.
How does Six Sigma work?
Six Sigma uses statistical analyses to locate problems, measure them, analyze root cause, fix problems and learn from the experience.
The first step is identifying the problem.
Next, data are collected and analyzed in order to identify patterns and trends.
The problem can then be fixed by taking corrective measures.
Finally, data will be reanalyzed to determine if there is an issue.
This continues until you solve the problem.
Statistics
- The BLS says that financial services jobs like banking are expected to grow 4% by 2030, about as fast as the national average. (wgu.edu)
- 100% of the courses are offered online, and no campus visits are required — a big time-saver for you. (online.uc.edu)
- Your choice in Step 5 may very likely be the same or similar to the alternative you placed at the top of your list at the end of Step 4. (umassd.edu)
- The profession is expected to grow 7% by 2028, a bit faster than the national average. (wgu.edu)
- Our program is 100% engineered for your success. (online.uc.edu)
External Links
How To
How do I do the Kaizen Method?
Kaizen means continuous improvement. This Japanese term refers to the Japanese philosophy of continuous improvement that emphasizes incremental improvements and constant improvement. It's where people work together in order to improve their processes constantly.
Kaizen is one of Lean Manufacturing's most efficient methods. The concept involves employees responsible for manufacturing identifying problems and trying to fix them before they become serious issues. This will increase the quality and decrease the cost of the products.
Kaizen is the idea that every worker should be aware of what is going on around them. So that there is no problem, you should immediately correct it if something goes wrong. Report any problem you see at work to your manager.
Kaizen is based on a few principles. Start with the end product, and then move to the beginning. For example, if we want to improve our factory, we first fix the machines that produce the final product. We then fix the machines producing components, and the machines producing raw materials. We then fix the workers that work with those machines.
This is known as "kaizen", because it emphasizes improving each step. After we're done with the factory, it's time to go back and fix the problem.
To implement kaizen in your business, you need to find out how to measure its effectiveness. There are many ways to tell if kaizen is effective. Another method is to see how many defects are found on the products. Another way to find out how productive your company has been since you implemented kaizen is to measure the increase in productivity.
A good way to determine whether kaizen has been implemented is to ask why. Is it because the law required it or because you want to save money. Did you really believe it would lead to success?
Let's say you answered yes or all of these questions. Congratulations! Now you're ready for kaizen.