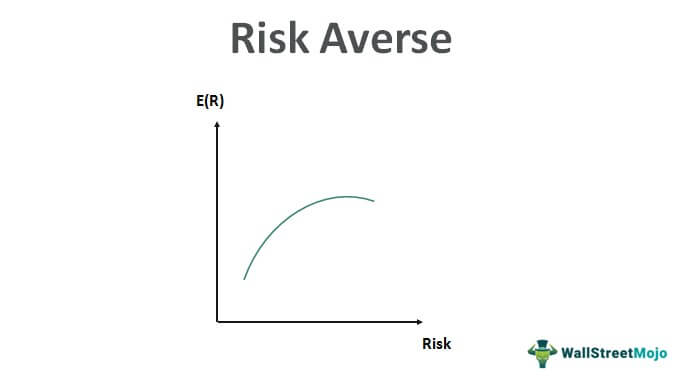
While many employees are open to the idea of change, some resist it. If you've ever run a project and encountered a lot of resistance, don't despair. There are many strategies to combat resistance to change. But first, you need to understand why it occurs. There are many reasons that resistance may occur. These groups can include employees, managers and stakeholders as well the external environment. If you want to increase employee engagement identify the root causes and then find solutions.
Employees
Employee resistance to change management can arise for many reasons. Some will protest change publicly and attempt to stop it becoming a reality. Others might try to resist the change by organizing labor unions, or misinterpreting its direction. It doesn't matter what reason it may be, it is crucial to understand how to deal with employee resistance to change management. These tips will help you deal with employee resistance in positive ways.
Communicate effectively. Employees should be informed about changes to tools and processes when an organization adopts them. Employees can then learn from the company and make the change a success. This helps to reduce resistance by employees to change management. In order to support employees in adapting to new tools or processes, the organization must provide them with adequate information, support, guidance, and training. If employees are not prepared for the change, the transition process may become more difficult and the management may need to go back to its previous process or policy.
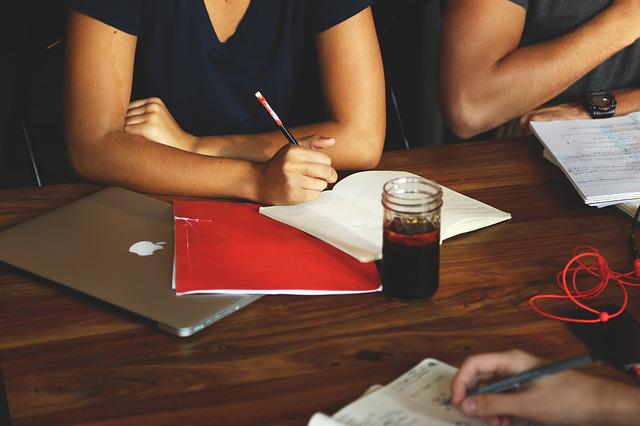
Managers
Managers need to convince workers that their changes are the best. Managers need to convince workers that the changes are worth it. To minimize resistance, the changes should be slowly implemented. They should not compromise the security of workers. Managers need to consider the opinions of all employees in order overcome resistance. Managers must adapt to the changes and give training to employees. They will eventually be able to accept the changes and reduce their resistance.
The resistance to change can be reduced by creating a supportive environment where employees feel involved. Employees who believe that change is necessary and in their best interests will be more open to the idea of change management. Employees will not feel informed about changes if they don't get it. Employees will also be less willing accept changes if they don't have the opportunity to participate in the changing process. They will also have less trust in the management if they are not informed about the changes.
Stakeholders
Stakeholder resistance to change management can have a significant impact on the success of a change management initiative. You can gain stakeholder buy in and reduce resistance by creating an action plan. It is important to note that not all stakeholders will be resistant or have the same reasons for their resistance. Some may be unsure of the change and others may be more concerned. If this is the situation, it is essential to communicate the changes to the stakeholders and work together to alleviate any fears.
While change can be difficult for everyone, it is often necessary in order to implement new initiatives. The stakeholder community will want to get involved regardless of the magnitude of the change. Many employees are reluctant about accepting change. Therefore, the organization needs give them the power and responsibility to make the changes. Software and other technological innovations can help you motivate and engage employees better. With the right tools, stakeholders can also self-engage in change management programs.
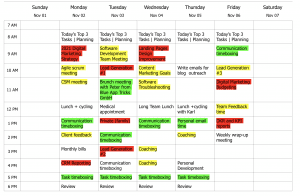
External environment
There are many sources of resistance to change management. People are more inclined to accept changes that will improve their personal lives. These changes may be because they feel that they are beneficial. Others may resist change if they are afraid it will affect their career. It is important that you recognize the causes of resistance so that you can take steps to eliminate them. Resistance to change management can also come from the external environment.
The employees will be affected by changes in the company. Changes in the organization, such as new salespeople or job titles, can make employees feel anxious. In such a case, it is important to set up safe communication channels to enable stakeholders to express their views. This can be a way to overcome structural inertia. These resistances can be overcome by addressing their pain points and ensuring that communication channels are open to all. External environment can also cause resistance when an organization is in transition.
FAQ
How can a manager motivate employees?
Motivation is the desire for success.
It is possible to be motivated by doing something you enjoy.
You can also get motivated by seeing your contribution to the success or the improvement of the organization.
For example: If you want to be a doctor, you might find it more motivating seeing patients than reading medical books all day.
The inner motivation is another type.
You may feel strongly that you are responsible to help others.
Maybe you like working hard.
If you don’t feel motivated, find out why.
You can then think of ways to improve your motivation.
What is the difference in Six Sigma and TQM?
The main difference between these two quality management tools is that six sigma focuses on eliminating defects while total quality management (TQM) focuses on improving processes and reducing costs.
Six Sigma is a method for continuous improvement. This method emphasizes eliminating defects using statistical methods such p-charts, control charts, and Pareto analysis.
This method aims to reduce variation in product production. This is done by identifying root causes and rectifying them.
Total Quality Management involves monitoring and measuring every aspect of the organization. This includes training employees to improve their performance.
It is frequently used as an approach to increasing productivity.
How does Six Sigma work
Six Sigma employs statistical analysis to identify problems, measure them and analyze root causes. Six Sigma also uses experience to correct problems.
The first step to solving the problem is to identify it.
Next, data are collected and analyzed in order to identify patterns and trends.
Next, corrective steps are taken to fix the problem.
Finally, data will be reanalyzed to determine if there is an issue.
This continues until the problem has been solved.
Statistics
- Your choice in Step 5 may very likely be the same or similar to the alternative you placed at the top of your list at the end of Step 4. (umassd.edu)
- The BLS says that financial services jobs like banking are expected to grow 4% by 2030, about as fast as the national average. (wgu.edu)
- Hire the top business lawyers and save up to 60% on legal fees (upcounsel.com)
- Our program is 100% engineered for your success. (online.uc.edu)
- 100% of the courses are offered online, and no campus visits are required — a big time-saver for you. (online.uc.edu)
External Links
How To
How do I do the Kaizen Method?
Kaizen means continuous improvement. This term was first used by Toyota Motor Corporation in the 1950s. It refers to the Japanese philosophy that emphasizes continuous improvement through small incremental changes. It's where people work together in order to improve their processes constantly.
Kaizen is one method that Lean Manufacturing uses to its greatest advantage. This concept requires employees to identify and solve problems during manufacturing before they become major issues. This improves the quality of products, while reducing the cost.
Kaizen is a way to raise awareness about what's happening around you. If something is wrong, it should be corrected immediately so that no problem occurs. So, if someone notices a problem while working, he/she should report it to his/her manager.
There are some basic principles that we follow when doing kaizen. The end product is always our starting point and we work toward the beginning. In order to improve our factory's production, we must first fix the machines producing the final product. We then fix the machines producing components, and the machines producing raw materials. Then, we fix those who work directly with the machines.
This approach is called 'kaizen' because it focuses on improving everything steps by step. Once we have finished fixing the factory, we return to the beginning and work until perfection.
You need to know how to measure the effectiveness of kaizen within your business. There are many ways to tell if kaizen is effective. Another method is to see how many defects are found on the products. Another way to find out how productive your company has been since you implemented kaizen is to measure the increase in productivity.
You can also find out if kaizen works by asking yourself why you decided to implement it. Is it because the law required it or because you want to save money. Did you really think that it would help you achieve success?
Suppose you answered yes to any of these questions, congratulations! You're now ready to get started with kaizen.