
These are the fundamentals of management and organization. They govern how we plan, execute, and measure our efforts. These principles derive from works by classical economists, such as Adam Smith and John Stuart Mill. Several technical innovators also contributed to this field, including Eli Watt and Matthew Boulton.
Managing
Management's role is to ensure that all employees understand what they are doing and that everything runs smoothly. Businesses can succeed regardless of how small or large they are by managing them. This program is intended for middle-level and junior managers in large corporations, small businesses, nonprofits, government services, and other organizations.

Monitoring
Monitoring is an important management technique that includes collecting, analysing, and reporting data in order to improve performance and measure progress. It involves identifying activities and target audiences and then tracking changes over time. This information allows managers to make timely decisions about program success.
Implementing
This paper describes the process of implementing organizational change. Even small changes can be hard to implement, but it is possible to make the change work if everyone involved welcomes the changes. Youker's paper examines change resistance and outlines ways to improve acceptance. The paper also includes an analytical model for the study of change resistance.
Controlling
Management is one of the main functions. This function ensures that the resources of an organization are effectively used and that the organization's objectives are met. It also helps in keeping employees motivated by keeping performance standards high and ensuring that the resources are allocated in an efficient manner.
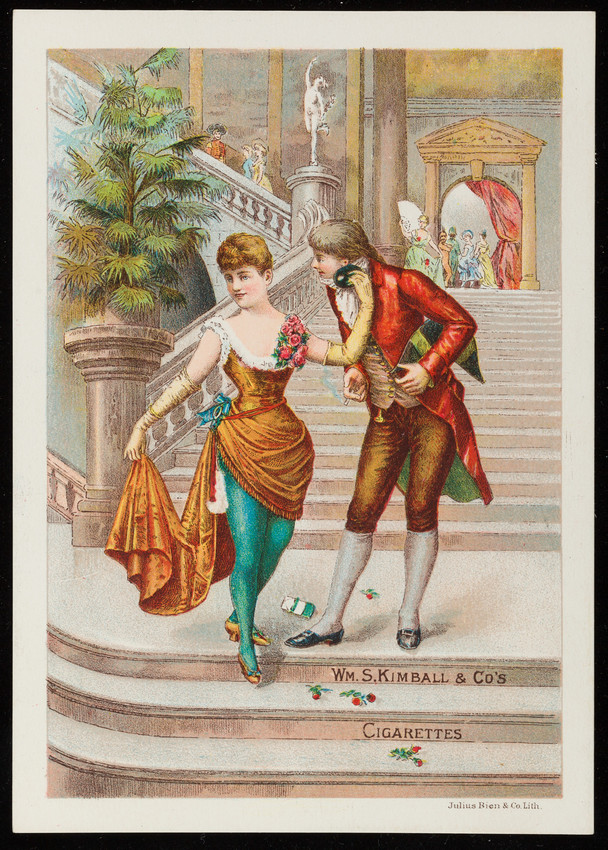
Optimal utilization of resources
Resource management is the process that balances demand with supply to create a more efficient business. It is essential to manage resources properly in order to maximize profits and increase efficiency. Companies can also operate more smoothly and continuously thanks to resource management. In addition, resource management helps businesses rise above their competition.
FAQ
What are the steps in the decision-making process in management?
The decision-making process of managers is complicated and multifaceted. It involves many elements, including analysis, strategy. planning. implementation. measurement. evaluation. feedback.
Management of people requires that you remember that they are just as human as you are, and can make mistakes. You can always improve your performance, provided you are willing to make the effort.
This video shows you how management makes decisions. We'll discuss the different types and reasons they are important. Managers should also know how to navigate them. Here are some topics you'll be learning about:
What are the five management methods?
Each business has five stages: planning, execution and monitoring.
Setting goals for the future is part of planning. It involves setting goals and making plans.
Execution is when you actually execute the plans. These plans must be adhered to by everyone.
Monitoring allows you to monitor your progress towards achieving your goals. This should involve regular reviews of performance against targets and budgets.
At the end of every year, reviews take place. These reviews allow you to evaluate whether the year was successful. If not, it is possible to make improvements for next year.
After the annual review, evaluation takes place. It helps identify what worked well and what didn't. It also provides feedback regarding how people performed.
What is the difference between leadership and management?
Leadership is about influence. Management is about controlling others.
A leader inspires his followers while a manager directs the workers.
A leader inspires others to succeed, while a manager helps workers stay on task.
A leader develops people; a manager manages people.
What are some of the common mistakes made by managers?
Sometimes, managers make their job more difficult than it is.
They may not be able to delegate enough responsibility to staff or provide adequate support.
A majority of managers lack the communication skills needed to motivate their team and lead them.
Managers sometimes set unrealistic expectations of their teams.
Managers may choose to solve every problem all by themselves, instead of delegating to others.
Six Sigma is so well-known.
Six Sigma is easy to use and can lead to significant improvements. Six Sigma provides a framework to measure improvements and allows companies to focus on the most important things.
What is the difference in Six Sigma and TQM?
The main difference in these two quality management tools lies in the fact that six sigma is focused on eliminating defects and total quality management (TQM), emphasizes improving processes and reducing costs.
Six Sigma is a method for continuous improvement. This method emphasizes eliminating defects using statistical methods such p-charts, control charts, and Pareto analysis.
This method aims to reduce variation in product production. This is accomplished by identifying the root cause of problems and fixing them.
Total Quality Management involves monitoring and measuring every aspect of the organization. It also involves training employees to improve performance.
It is often used as a strategy to increase productivity.
It seems so difficult sometimes to make sound business decisions.
Complex systems are often complex and have many moving parts. The people who run them must juggle multiple priorities at once while also dealing with uncertainty and complexity.
Understanding how these factors impact the whole system is key to making informed decisions.
This requires you to think about the purpose and function of each component. It's important to also consider how they interact with each other.
Also, you should ask yourself if there have been any assumptions in your past behavior. If not, you might want to revisit them.
For help, ask someone else if you're still stumped after all the above. You may be able to see things from a different perspective than you are and gain insight that can help you find a solution.
Statistics
- UpCounsel accepts only the top 5 percent of lawyers on its site. (upcounsel.com)
- Hire the top business lawyers and save up to 60% on legal fees (upcounsel.com)
- Our program is 100% engineered for your success. (online.uc.edu)
- As of 2020, personal bankers or tellers make an average of $32,620 per year, according to the BLS. (wgu.edu)
- 100% of the courses are offered online, and no campus visits are required — a big time-saver for you. (online.uc.edu)
External Links
How To
What is Lean Manufacturing?
Lean Manufacturing processes are used to reduce waste and improve efficiency through structured methods. They were developed in Japan by Toyota Motor Corporation (in the 1980s). The aim was to produce better quality products at lower costs. Lean manufacturing seeks to eliminate unnecessary steps and activities in the production process. It includes five main elements: pull systems (continuous improvement), continuous improvement (just-in-time), kaizen (5S), and continuous change (continuous changes). Pull systems involve producing only what the customer wants without any extra work. Continuous improvement involves constantly improving upon existing processes. Just-in-time is when components and other materials are delivered at their destination in a timely manner. Kaizen means continuous improvement, which is achieved by implementing small changes continuously. Finally, 5S stands for sort, set in order, shine, standardize, and sustain. These five elements can be combined to achieve the best possible results.
The Lean Production System
Six key concepts form the foundation of the lean production system:
-
Flow is about moving material and information as near as customers can.
-
Value stream mapping - Break down each stage in a process into distinct tasks and create an overview of the whole process.
-
Five S's - Sort, Set In Order, Shine, Standardize, and Sustain;
-
Kanban is a visual system that uses visual cues like stickers, colored tape or stickers to keep track and monitor inventory.
-
Theory of constraints: Identify bottlenecks and use lean tools such as kanban boards to eliminate them.
-
Just-in time - Get components and materials delivered right at the point of usage;
-
Continuous improvement - make incremental improvements to the process rather than overhauling it all at once.