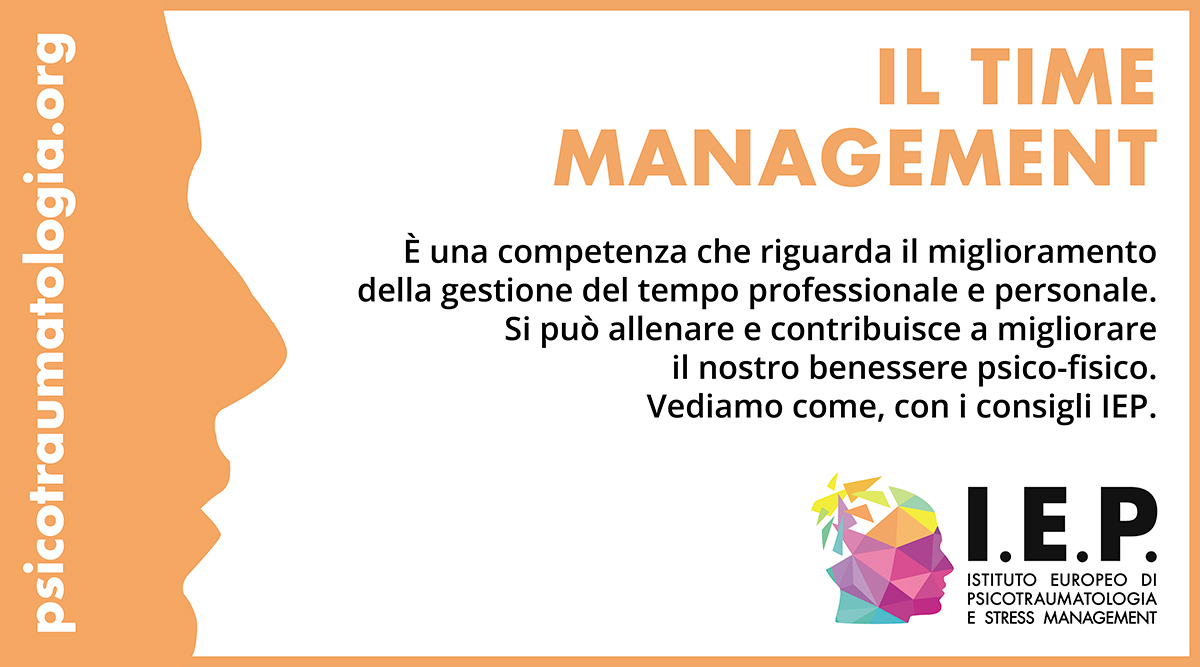
Group factors can have a significant impact on any organisational change. These factors include both the formal and informal members of an organization. Although formal groups can resist change, such as trade unions, informal groups are also strong barriers to change. Changes in group dynamics can have a significant impact on work flow, job design, social organisation, influence systems, and other aspects of the workplace. Changes may also affect communication patterns and status systems. It is crucial to understand these factors and how they can be dealt with in order to successfully implement any change.
Organizational resistance to change
Most people's perception of change is what causes resistance to change within organizations. Mullin states that there are very few things management can do to solve this problem. There are however many solutions. Two perspectives can be used by employees when assessing the impact of organizational change. Firstly, they respond to the change according to what they see or how they perceive it. This view differs from Van Tonder's view, which suggests that people form their responses to organisational change at the employee level.
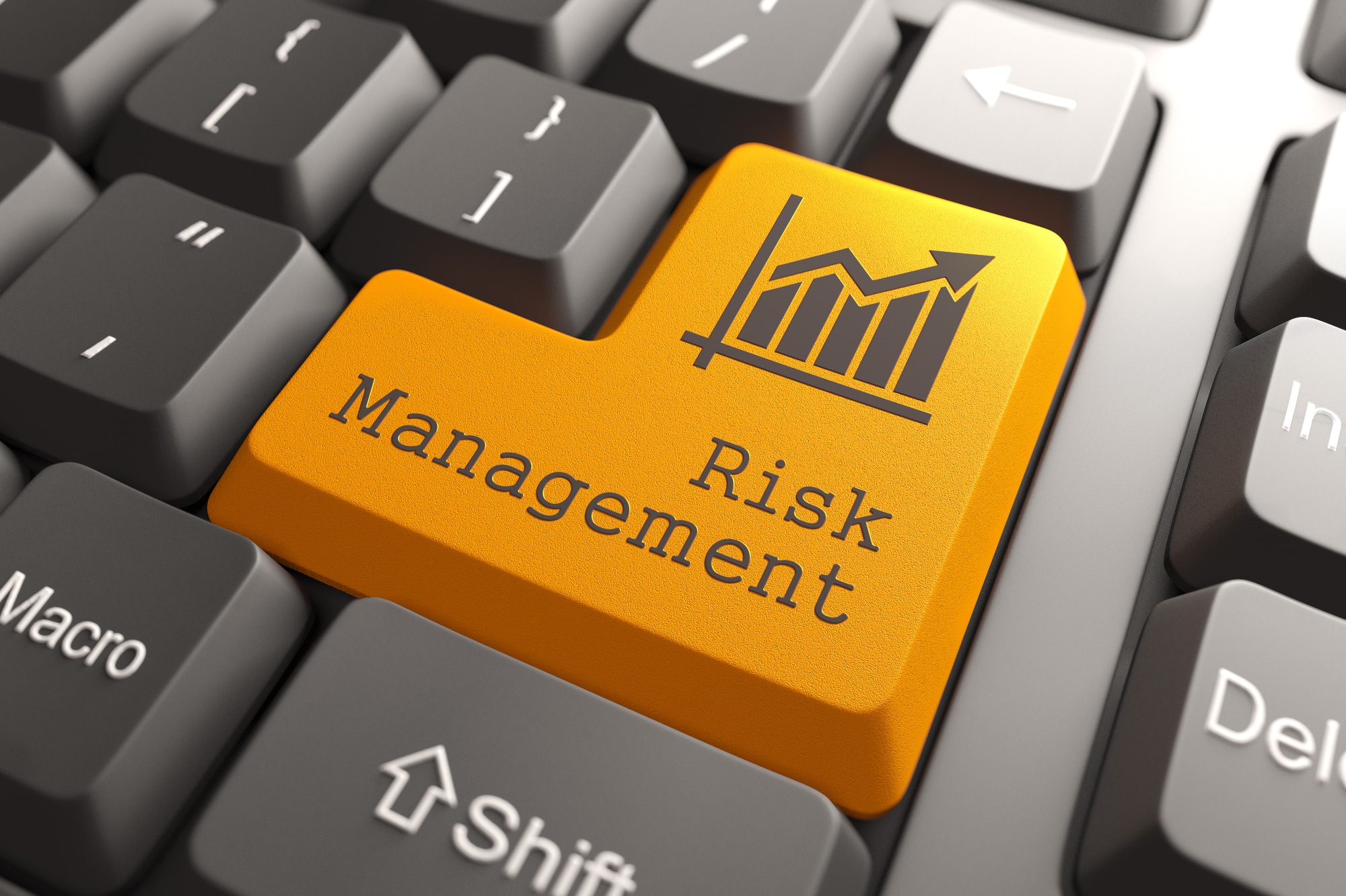
Types and types of organizational change
Organisations are subject to a variety of types of transformations, including structural changes and complete transformations. To remain competitive, organisations must adapt to changing business environments. Adaptive changes are not disruptive. Adaptive change occurs when an organisation strives to improve its processes and strategies. Organizations that are undergoing transformations need to plan for the transition and prepare accordingly. This article will outline the main differences among different types and how they might affect an organisation.
External environment has an influence
The external environment is a complex web of factors that affect the operation of an organisation. These factors aren't deterministic and can change at different speeds. Instead, they are mutually reinforcing and influence one another. Changes in the environment force organizations to adapt and make pro-active changes. This article will focus on the most common external factors that cause change. It is important that you understand the interconnectedness among the external and internal environments of your company.
Process-oriented changes
Process-oriented change in an organisation refers to changes that have an impact on workflow, productivity, and group cohesion. The examples of process-oriented innovation include robots in manufacturing facilities and laser-scanning checkout machines at supermarkets. Both types of change affect the culture of an organisation in different ways, and the kind of change that is most beneficial for your company will depend on the culture it exists in. This article will cover the benefits and differences between process-oriented, and other types or change that may occur within an organization.
Structural change
The key component to organisational development is change management. Although small changes in policies and tools may have an impact on a company, they can also have a profound effect on the company's performance. However, larger-scale changes can transform a company. The strategy chosen is crucial to the success of such transformations. It is important to plan well and prepare for the change to be a success. The ultimate goal should be identified, and a plan developed to reach it. For a new strategy to succeed, it is important to manage change continuously.
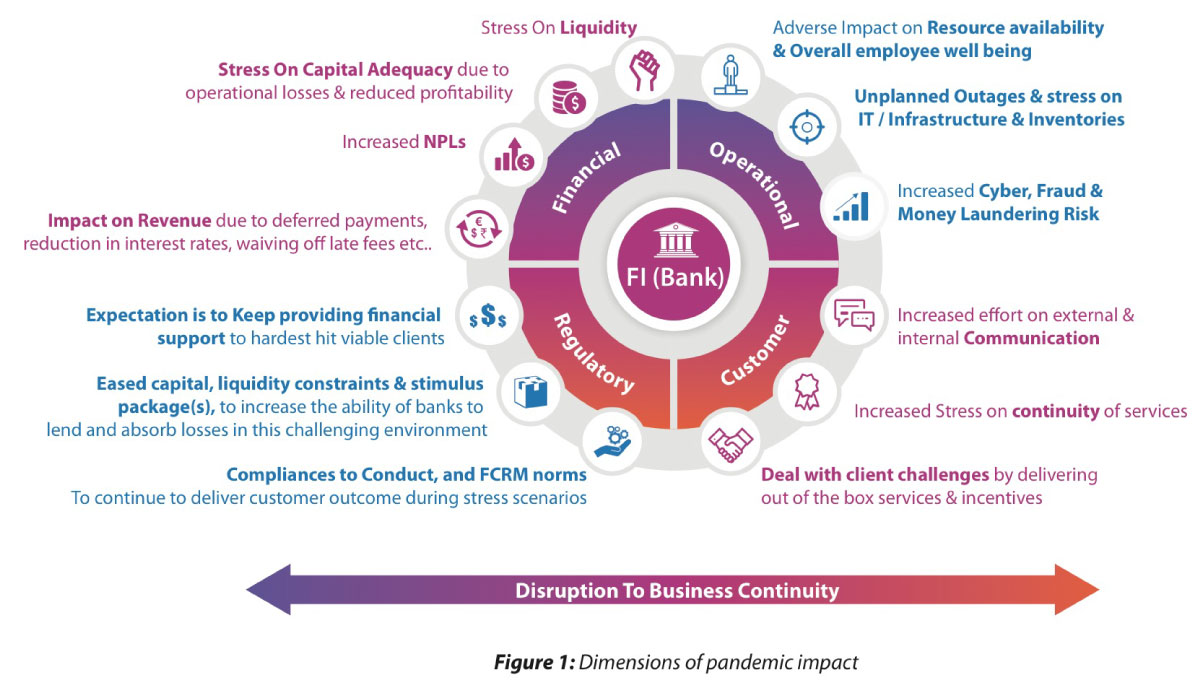
Technological changes
Technology change management is the process of identifying new technologies which can benefit an organisation. Technology change management involves planning and defining requirements, estimating benefits and life spans, identifying appropriate technology sources, and documenting the results. A process to select technologies for an organisation is documented in a technology change management policy and procedure. This document documents and documents potential challenges and solutions as well as acquisitions and requests to acquire new technologies.
FAQ
Six Sigma is so beloved.
Six Sigma is easy to implement and can produce significant results. It can also be used to help companies identify and focus on the most important aspects of their business.
How do we create a company culture that is productive?
A company culture that values and respects its employees is a successful one.
It's based on three main principles:
-
Everybody has something of value to share
-
People are treated fairly
-
Individuals and groups can have mutual respect
These values are reflected in the way people behave. They will treat others with consideration and courtesy.
They will respect the opinions of others.
And they will encourage others to share ideas and feelings.
In addition, the company culture encourages open communication and collaboration.
People feel free to express their views openly without fear of reprisal.
They know that they will not be judged if they make mistakes, as long as the matter is dealt with honestly.
Finally, the company culture promotes honesty and integrity.
Everyone knows that they must always tell the truth.
Everyone understands that there are rules and regulations which apply to them.
Nobody expects to be treated differently or given favors.
What's the difference between leadership & management?
Leadership is about being a leader. Management is all about controlling others.
A leader inspires followers while a manager directs workers.
Leaders motivate people to succeed; managers keep workers on track.
A leader develops people; a manager manages people.
What kind people use Six Sigma?
Six Sigma is well-known to those who have worked in operations research and statistics. However, anyone involved in any aspect of business can benefit from using it.
Because it requires a high degree of commitment, only leaders with strong leadership skills can implement it successfully.
What is Six Sigma?
It's an approach to quality improvement that emphasizes customer service and continuous learning. The objective is to eliminate all defects through statistical methods.
Motorola invented Six Sigma in 1986 as part its efforts to improve manufacturing.
The idea spread quickly in the industry. Today many organizations use six-sigma techniques to improve product design.
What is TQM and how can it help you?
The quality movement was born during the industrial revolution when manufacturing companies realized they could not compete on price alone. If they wanted to stay competitive, they needed to improve their quality and efficiency.
Management developed Total Quality Management to address the need for improvement. It focused on all aspects of an organisation's performance. It included continuous improvement processes, employee involvement, and customer satisfaction.
Statistics
- The average salary for financial advisors in 2021 is around $60,000 per year, with the top 10% of the profession making more than $111,000 per year. (wgu.edu)
- The BLS says that financial services jobs like banking are expected to grow 4% by 2030, about as fast as the national average. (wgu.edu)
- Our program is 100% engineered for your success. (online.uc.edu)
- 100% of the courses are offered online, and no campus visits are required — a big time-saver for you. (online.uc.edu)
- Your choice in Step 5 may very likely be the same or similar to the alternative you placed at the top of your list at the end of Step 4. (umassd.edu)
External Links
How To
How can you implement the Kaizen technique?
Kaizen means continuous improvement. This Japanese term refers to the Japanese philosophy of continuous improvement that emphasizes incremental improvements and constant improvement. It is a process where people come together to improve their processes.
Kaizen is one of Lean Manufacturing's most efficient methods. The concept involves employees responsible for manufacturing identifying problems and trying to fix them before they become serious issues. This way, the quality of products increases, and the cost decreases.
Kaizen is about making everyone aware of the world around them. So that there is no problem, you should immediately correct it if something goes wrong. Report any problem you see at work to your manager.
Kaizen is based on a few principles. Start with the end product, and then move to the beginning. For example, if we want to improve our factory, we first fix the machines that produce the final product. Next, we fix the machines which produce components. Finally, we repair the workers who are directly involved with these machines.
This is known as "kaizen", because it emphasizes improving each step. We finish fixing the factory and then go back to the beginning. This continues until we achieve perfection.
You need to know how to measure the effectiveness of kaizen within your business. There are many ways you can determine if kaizen has been implemented well. Another method is to see how many defects are found on the products. Another way is determining how much productivity increased after implementing kaizen.
Another way to know whether kaizen is working is to ask yourself why did you decide to implement kaizen. Did you do it because it was legal or to save money? It was a way to save money or help you succeed.
If you answered yes to any one of these questions, congratulations! You are ready to start kaizen.