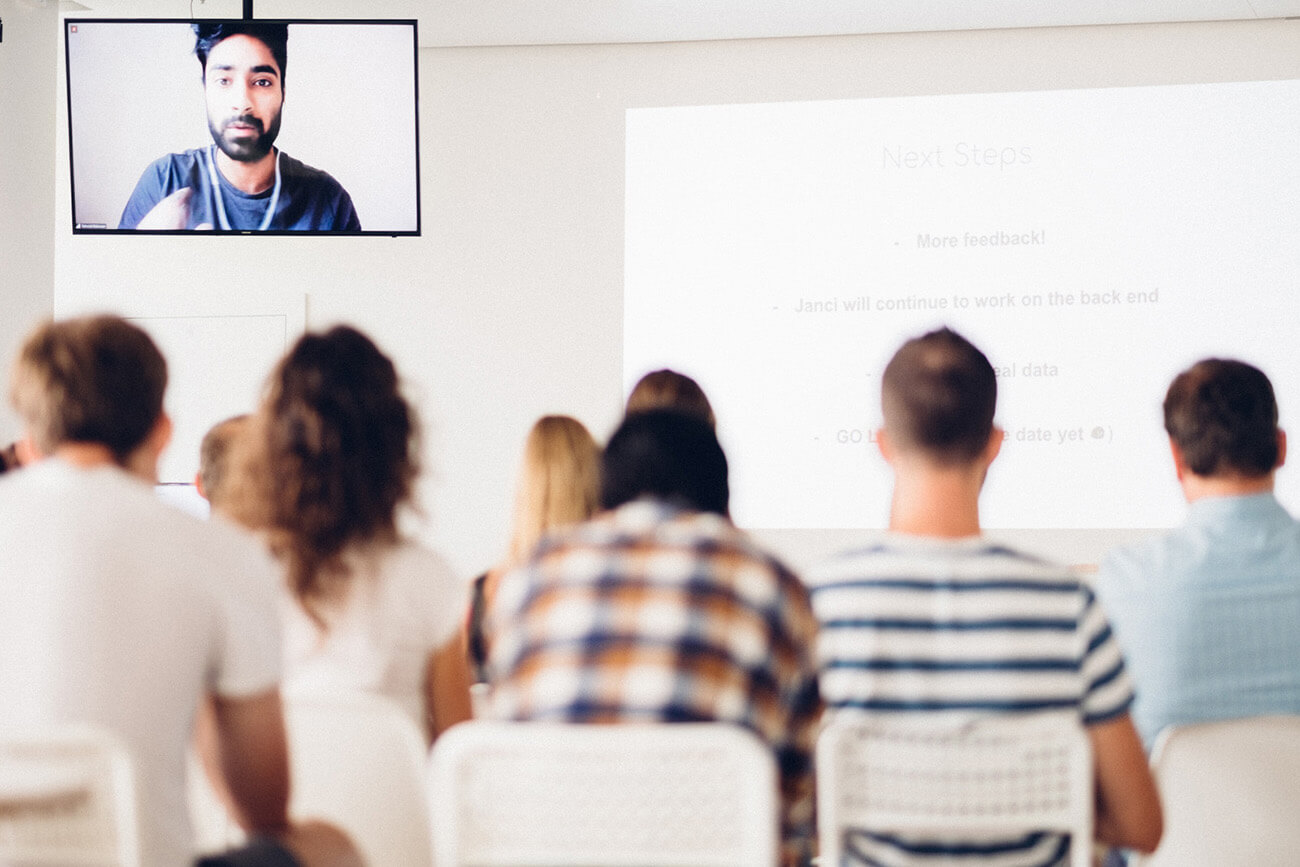
Construction risk management involves taking steps to reduce the likelihood of a project happening. A brainstorming session is necessary to identify risk. Brainstorming sessions do not aim to solve specific problems, but rather to identify possible scenarios that might arise during the project. This session allows the team to use their collective knowledge and expertise as a way to brainstorm potential solutions. A team can also look at past projects to determine risks.
Common factors that increase construction risk
Construction sites can be dangerous. It is important to manage construction sites safely. The manager needs to report risks and take appropriate steps to minimize them. Hazards include falling objects, uneven surfaces, and hazards related to manual handling. Additionally, job sites should be well lit. To minimize the danger of falling and tripping on equipment and cables, they should be located in a high place.
Another risk is the inevitable occurrence of change orders. When these are not managed properly, they can cause a huge amount of additional work on a project. In some cases, changing orders could even have an impact on the overall success or failure of the project. A subcontractor might not communicate with others well, and a project may be delayed. This could cause wasteful materials and costly repairs.
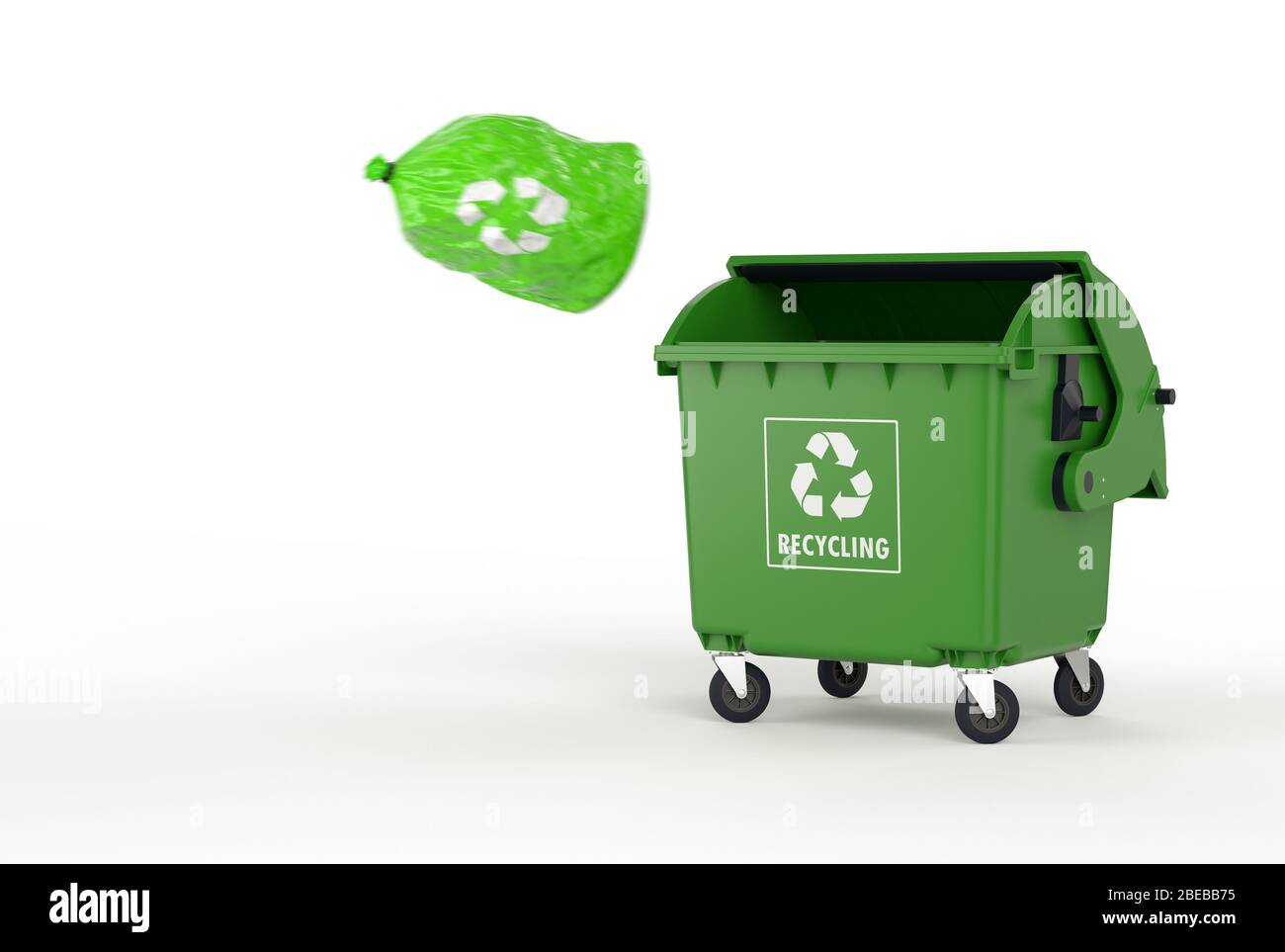
Mitigation strategies
A critical aspect of project management is the creation of mitigation plans. It is vital that project teams devise plans for managing risk and monitor their progress. These plans should take into consideration the unique nature of each project and its specific objectives. Implementing these strategies will allow project teams to protect and minimize the risk of their projects.
It is important to prioritize and identify risks according the likelihood and impact of them. High-impact threats should be addressed first while low-impact issues should be addressed later. High-impact risks, such as material price increases, can have a negative impact on margins. The project could be affected by inclement weather and geological events that have low impact.
Planning
To manage construction risk, it is important to identify the most serious risks early on in a project. This will enable the team to address potential problems as soon as possible. The process is also a great opportunity to involve team members who have different expertise and perspectives. They may be able to identify hidden risks that you might not have otherwise considered. Meetings should be held to discuss new risk as they emerge.
Preplanning looks at the process before and during construction, from the beginning to the end. This process has two main goals: to identify and reduce losses, minimize disruptions, and maximize efficiency. Preplanning can help mitigate and even eliminate certain risks if done properly.

Transferring risk
Transferring construction risks is a great method to reduce exposure for the owner and contractor in the case of an accident. It is crucial to transfer the risk efficiently. There are many methods to achieve this goal, and it is important to begin as soon possible. Continue reading to learn more about risk transfer and how to make your program successful.
Good risk management will assign the project's risks only to those that are most likely to manage them. The majority of risk is assumed by the government agency that owns the construction, while the contractor transfers it to its subcontractors and suppliers.
FAQ
Why is it so hard to make smart business decisions?
Complex systems are often complex and have many moving parts. They require people to manage multiple priorities and deal with uncertainty and complexity.
Understanding the impact of these factors on the system is crucial to making sound decisions.
You need to be clear about the roles and responsibilities of each system. You then need to consider how those individual pieces interact with each other.
It is also worth asking yourself if you have any unspoken assumptions about how you have been doing things. If so, it might be worth reexamining them.
Try asking for help from another person if you're still stuck. You may be able to see things from a different perspective than you are and gain insight that can help you find a solution.
What does Six Sigma mean?
Six Sigma employs statistical analysis to identify problems, measure them and analyze root causes. Six Sigma also uses experience to correct problems.
The first step is identifying the problem.
The next step is to collect data and analyze it in order to identify trends or patterns.
Then, corrective actions can be taken to resolve the problem.
The data are then reanalyzed to see if the problem is solved.
This cycle continues until there is a solution.
What role can a manager fill in a company’s management?
The role of a manager varies from one industry to another.
A manager generally manages the day to-day operations in a company.
He/she ensures the company meets its financial commitments and produces goods/services that customers demand.
He/she makes sure that employees adhere to the rules and regulations as well as quality standards.
He/she designs new products or services and manages marketing campaigns.
Statistics
- The profession is expected to grow 7% by 2028, a bit faster than the national average. (wgu.edu)
- As of 2020, personal bankers or tellers make an average of $32,620 per year, according to the BLS. (wgu.edu)
- 100% of the courses are offered online, and no campus visits are required — a big time-saver for you. (online.uc.edu)
- Our program is 100% engineered for your success. (online.uc.edu)
- UpCounsel accepts only the top 5 percent of lawyers on its site. (upcounsel.com)
External Links
How To
What is Lean Manufacturing?
Lean Manufacturing uses structured methods to reduce waste, increase efficiency and reduce waste. They were developed by Toyota Motor Corporation in Japan during the 1980s. The primary goal was to make products with lower costs and maintain high quality. Lean manufacturing is about eliminating redundant steps and activities from the manufacturing process. It is made up of five elements: continuous improvement, continuous improvement, just in-time, continuous change, and 5S. The production of only what the customer needs without extra work is called pull systems. Continuous improvement refers to continuously improving existing processes. Just-intime refers the time components and materials arrive at the exact place where they are needed. Kaizen means continuous improvement. Kaizen involves making small changes and improving continuously. Last but not least, 5S is for sort. To achieve the best results, these five elements must be used together.
Lean Production System
Six key concepts underlie the lean production system.
-
Flow is about moving material and information as near as customers can.
-
Value stream mapping: This is a way to break down each stage into separate tasks and create a flowchart for the entire process.
-
Five S’s - Sorted, In Order. Shine. Standardize. And Sustain.
-
Kanban - use visual signals such as colored tape, stickers, or other visual cues to keep track of inventory;
-
Theory of constraints - identify bottlenecks during the process and eliminate them with lean tools like Kanban boards.
-
Just-in Time - Send components and material directly to the point-of-use;
-
Continuous improvement: Make incremental improvements to the process instead of overhauling it completely.