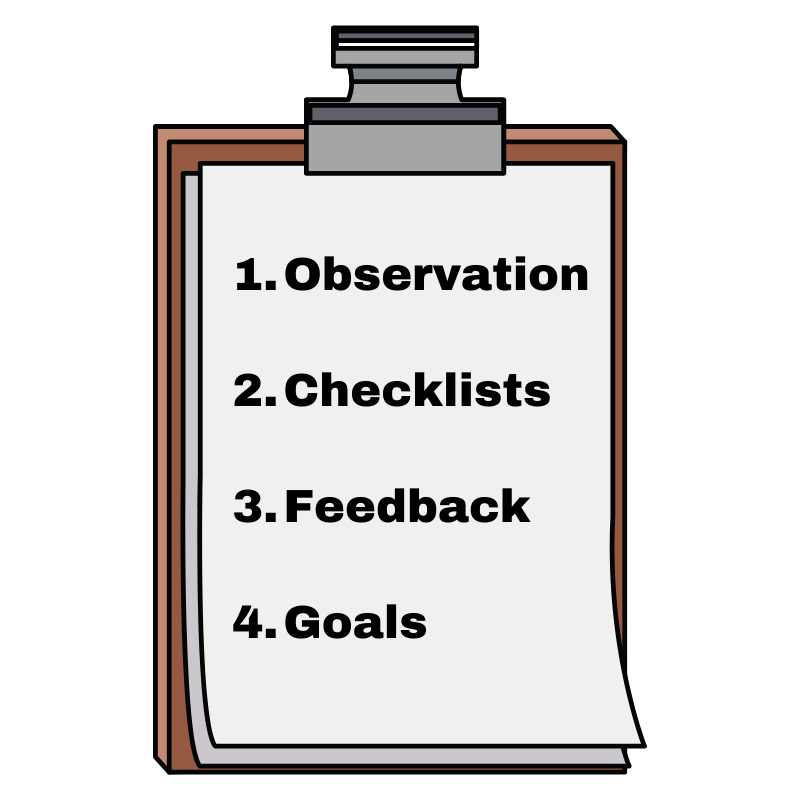
You can use a continuous improvement method to get the desired results over time. This type of methodology consists of iterative processes over several design generations. It is also known under the name Lean Six Sigma. This article will cover one variation of the PDSA method based on SIPOC analysis. Its application will be discussed in the context an engineering design studio.
Lean Six Sigma
Lean Six Sigma, a method for continuous improvement, focuses on making processes more predictable and simpler. The risk of process errors being overlooked is reduced when processes are simplified. This methodology employs statistical process control (SPC), which is a technique to control process variables and improve performance. This methodology can be applied to any product or service. The company must establish clear measurable characteristics and use data to guide the changes.
PDSA
The PDSA continuous improvement method uses a continuous loop that includes process design, analysis, action, and monitoring to improve a company's business processes. The study step in PDSA's initial phase is where the team evaluates and compares the results of an experiment. This step allows the team and the client to evaluate whether the improvement was a significant success. This step will allow the team to conduct analysis. They may use control charts to distinguish expected from special cause variation.
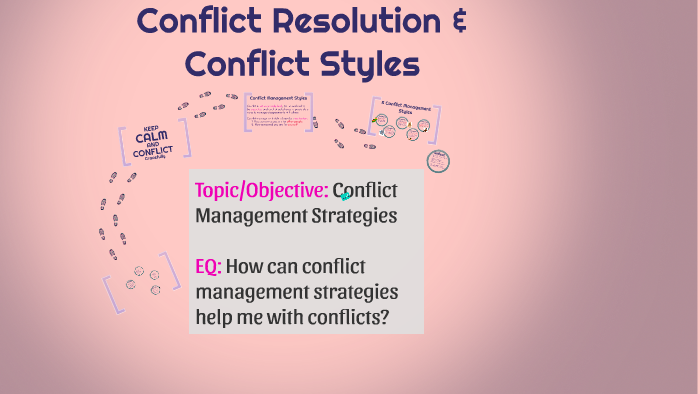
Variation of PDSA
PDSA is a method to continuously improve and solve problems. There are specific goals and a focus. The process begins with careful planning and moves onto effective action. Every idea is then evaluated for sustainability and feasibility. Project team members measure the results to ensure that every change leads to lasting improvements.
PDSA based SIPOC analyses
SIPOC analysis helps to improve business processes. It's an easy way to categorize data into five categories. SIPOC diagrams can help teams better understand their processes by providing a high-level overview of each. They can also be used to help focus discussions.
PDSA based DMAIC
Continuous improvement methodologies that follow the DMAIC process are useful for organizations seeking to improve their processes. These methodologies are straightforward and structured. They help organizations to understand inefficient processes, eliminate them, and achieve measurable and lasting results. Without the use of these tools, organizations may struggle to track which changes have the greatest impact and which ones don't. It can be difficult for them to implement effective controls.
PDSA based off kanban boards
Kanban boards have many great benefits. Kanban boards are a great way to visualize work in process, assign tasks, and attach images or attachments to each task. You can also control how much work is done and when it is finished.
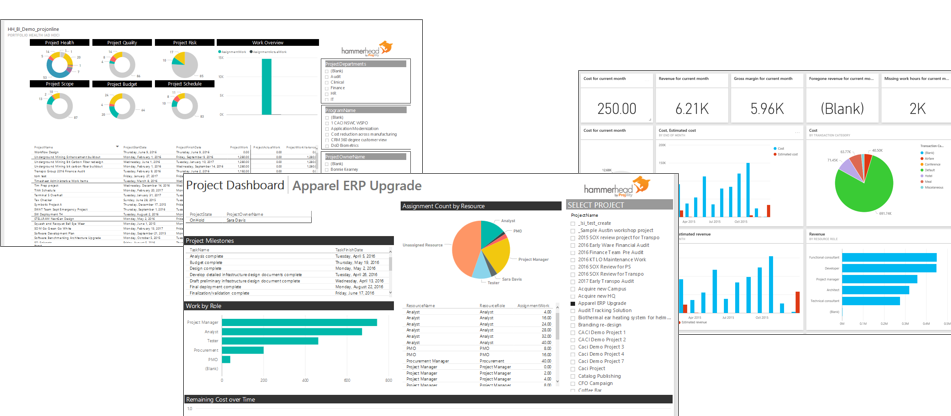
Kaizen is based on SIPOC analysis
The SIPOC model can be used as a powerful framework and concept in process improvement efforts. It helps to identify the process' boundaries, gather relevant information, and present it in a clear, understandable manner. It is useful for identifying process variations that could affect key performance indicators (KVIPs), and it is particularly helpful in the Define phase. It is also useful for teams and other stakeholders to plan improvements to improve processes.
PDSA based upon PDSA Variation
PDSA, a continuous improvement approach, is based on the principle that actual and anticipated results can be compared. The PDSA process measures the actual results of an improvement experiment against the expected results, and the reality of the implementation is compared with the plan. The team then analyses the data to determine if there were any measurable improvements. To distinguish between expected variation from special cause variation, this data is often categorized with a control diagram.
FAQ
What is the main difference between Six Sigma Six Sigma TQM and Six Sigma Six Sigma?
The key difference between the two quality management tools is that while six-sigma focuses its efforts on eliminating defects, total quality management (TQM), focuses more on improving processes and reducing cost.
Six Sigma is an approach for continuous improvement. It emphasizes the elimination and improvement of defects using statistical methods, such as control charts, P-charts and Pareto analysis.
The goal of this method is to reduce variation in product output. This is achieved by identifying and addressing the root causes of problems.
Total quality management includes monitoring and measuring all aspects of an organization's performance. It also involves training employees to improve performance.
It is commonly used as a strategy for increasing productivity.
What kind of people use Six Sigma
Six Sigma is well-known to those who have worked in operations research and statistics. Anybody involved in any aspect or business can benefit.
It requires high levels of commitment and leadership skills to be successful.
What are management principles?
Management concepts are the principles and practices used by managers to manage people, resources. They cover topics such as job descriptions and performance evaluations, human resource policies, training programs, employee motivation, compens systems, organizational structure, among others.
How can we create a culture of success in our company?
A successful company culture is one that makes people feel valued and respected.
It's based on three main principles:
-
Everyone has something valuable to contribute
-
People are treated fairly
-
There is mutual respect between individuals and groups
These values can be seen in the behavior of people. For example, they will treat others with courtesy and consideration.
They will respect other people's opinions.
They will also encourage others to share their ideas and feelings.
In addition, the company culture encourages open communication and collaboration.
People feel safe to voice their opinions without fear of reprisal.
They understand that mistakes can be forgiven as long as they're dealt with honestly.
The company culture promotes honesty, integrity, and fairness.
Everyone understands that the truth is always best.
Everyone understands that there are rules and regulations which apply to them.
Everyone does not expect to receive special treatment.
What is the meaning of "project management?"
Management is the act of managing activities in order to complete a project.
We help you define the scope of your project, identify the requirements, prepare the budget, organize the team, plan the work, monitor progress and evaluate the results before closing down the project.
How does a manager learn to manage?
You can improve your management skills by practicing them at all times.
Managers must monitor the performance of subordinates constantly.
You must act quickly if you notice that your subordinate isn’t performing to their standards.
You must be able to spot what is lacking and how you can improve it.
What is Kaizen?
Kaizen is a Japanese term meaning "continuous improvement." It is a philosophy that encourages employees to constantly look for ways to improve their work environment.
Kaizen is founded on the belief of everyone being able to do their job well.
Statistics
- UpCounsel accepts only the top 5 percent of lawyers on its site. (upcounsel.com)
- The average salary for financial advisors in 2021 is around $60,000 per year, with the top 10% of the profession making more than $111,000 per year. (wgu.edu)
- 100% of the courses are offered online, and no campus visits are required — a big time-saver for you. (online.uc.edu)
- Our program is 100% engineered for your success. (online.uc.edu)
- As of 2020, personal bankers or tellers make an average of $32,620 per year, according to the BLS. (wgu.edu)
External Links
How To
How do I get my Six Sigma license?
Six Sigma can be used to improve quality and efficiency. It is a process that helps businesses achieve consistent results in their operations. The name "Sigmas" comes from the Greek words "sigmas", meaning "six". Motorola created this process in 1986. Motorola realized they needed to standardize the manufacturing processes to produce products faster and cheaper. There were many people doing the work and they had difficulty achieving consistency. To overcome this problem they turned to statistical tools such control charts and Pareto analyses. They would then apply these techniques to all aspects of their operation. So, after applying this technique, they would be able to make changes where there was room for improvement. There are three main steps to follow when trying to get your Six Sigma certification. Find out if you are qualified. Before you take any exams, you'll need to take some classes. After passing the classes, you will be able to take the tests. The class material will be reviewed. After that, you can take the test. If you pass, then you will become certified. Finally, you will be able add your certifications onto your resume.