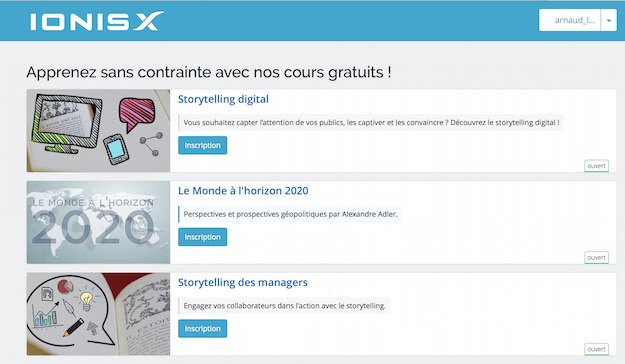
A management strategy for construction risk includes taking steps that reduce the chance of a particular project happening. To identify potential risks, the first step is to hold a brainstorming session. Brainstorming sessions are not intended to resolve specific problems. Instead, they aim to identify possible scenarios during the project. The team can use its collective knowledge and expertise in brainstorming possible solutions. A team can also look at past projects to determine risks.
Common causes of construction risks
Construction sites are filled with hazards, and managing construction sites safely is essential. The manager needs to report risks and take appropriate steps to minimize them. Hazards include uneven surfaces, falling objects, and other hazards associated manual handling. In addition, the job site needs to be well lit and tidy. To minimize the danger of falling and tripping on equipment and cables, they should be located in a high place.
Change orders, which are an inevitable component of construction, pose another major risk. If they aren't managed well, they can lead to a lot of extra work. In some cases, change orders may even affect the overall success of the project. If a subcontractor does not communicate well with the other contractors, a project can be delayed. This can result in wasteful materials and costly reworks.
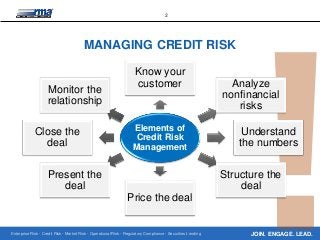
Mitigation strategies
The key part of project management is to create mitigation strategies. Project teams must develop plans to manage risk, monitor and evaluate them. The project's specificity and objectives should be considered when developing these plans. These strategies can help project teams protect their projects and reduce their risk exposure.
The first step in managing construction risk is to identify and prioritize risks based on their likelihood and potential impact. Low-impact risks must be dealt with later. High-impact risk should be addressed first. Materials price increases are one example of high-impact risks that can impact margins. Inclement weather and geological phenomena, which can impact the project's success, are both low-impact and medium-risk.
Preplanning
The best way to minimize construction risk is to plan early. This will allow the team and contractors to avoid potential problems. This is a great way to bring together people with different perspectives and expertise. You may discover hidden risks that you hadn't considered. You should keep the process of risk identification going, and meet with them to discuss new risks as soon as they occur.
Preplanning is the study of the construction process from beginning to end. This process is designed to reduce loss and minimize disruptions while maximising efficiency. Proper planning can reduce and even eliminate certain risk factors.
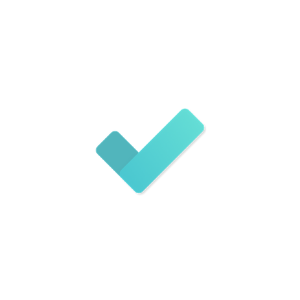
Transferring risk
Transferring construction risk is a great way to reduce the exposure of the contractor and owner in the event of an accident or lawsuit. But it is essential to transfer risk effectively. There are many ways to successfully transfer risk, and it is crucial to do so as soon as possible. Continue reading to learn more about risk transfer and how to make your program successful.
A solid risk management strategy will distribute the project's potential risks to those who are most capable of controlling them. The majority risk will be assumed and transferred to the contractors by the owner of the project, usually a government agency.
FAQ
What are the three basic management styles?
There are three types of management: participative, laissez faire, and authoritarian. Each style has its own strengths and weaknesses. What style do you prefer? Why?
Autoritarian – The leader sets the direction for everyone and expects them to follow. This style is most effective when an organization is large, stable, and well-run.
Laissez-faire – The leader gives each individual the freedom to make decisions for themselves. This approach works best in small, dynamic organizations.
Participative – Leaders are open to suggestions and ideas from everyone. This style works best in smaller organizations where everyone feels valued.
What is a simple management tool that aids in decision-making and decision making?
The decision matrix is a powerful tool that managers can use to help them make decisions. It helps them think systematically about all the options available to them.
A decision matrix represents alternatives in rows and columns. This makes it easy to see how each alternative affects other choices.
In this example, there are four possible options represented by boxes on the left-hand side of the matrix. Each box represents an alternative. The top row displays the current situation, and the bottom row shows what might happen if nothing is done.
The effect of selecting Option 1 is shown in the middle column. In this example, it would lead to an increase in sales of between $2 million and $3 million.
The effects of options 2 and 3 are shown in the next columns. These are both positive changes that increase sales by $1million and $500,000. They also have negative consequences. For instance, Option 2 increases cost by $100 thousand while Option 3 reduces profits by $200 thousand.
The last column shows you the results of Option 4. This results in a decrease of sales by $1,000,000
The best thing about a decision matrix is the fact that you don't have to remember which numbers go with what. The best thing about a decision matrix is that you can simply look at the cells, and immediately know whether one option is better or not.
The matrix has already done all of the work. It's simply a matter of comparing the numbers in the relevant cells.
Here's a sample of how you might use decision matrixes in your business.
Advertising is a decision that you make. If you do this, you will be able to increase revenue by $5000 per month. But, you will also incur additional expenses of $10 thousand per month.
The net result of advertising investment can be calculated by looking at the cell below that reads "Advertising." It is 15 thousand. Advertising is more valuable than its costs.
What is the main difference between Six Sigma Six Sigma TQM and Six Sigma Six Sigma?
The main difference between these two quality management tools is that six sigma focuses on eliminating defects while total quality management (TQM) focuses on improving processes and reducing costs.
Six Sigma is a methodology for continuous improvement. It emphasizes the elimination and improvement of defects using statistical methods, such as control charts, P-charts and Pareto analysis.
This method has the goal to reduce variation of product output. This is achieved by identifying and addressing the root causes of problems.
Total quality management refers to the monitoring and measurement of all aspects in an organization. It also includes training employees to improve performance.
It is often used as a strategy to increase productivity.
What are some common mistakes managers make?
Sometimes managers make their job harder than they need to.
They might not give enough support and delegate the right responsibilities to their staff.
Managers often lack the communication skills necessary to motivate and guide their teams.
Managers set unrealistic expectations and make it difficult for their team.
Some managers may try to solve every problem themselves instead of delegating responsibility to others.
How to effectively manage employees
Effectively managing employees requires that you ensure their happiness and productivity.
It is important to set clear expectations about their behavior and keep track of their performance.
To do this successfully, managers need to set clear goals for themselves and for their teams.
They need to communicate clearly and openly with staff members. And they need to ensure that they reward good performance and discipline poor performers.
They must also keep records of team activities. These include:
-
What did you accomplish?
-
How much work was done?
-
Who did it?
-
What was the moment it was completed?
-
Why did it happen?
This data can be used to evaluate and monitor performance.
Statistics
- The profession is expected to grow 7% by 2028, a bit faster than the national average. (wgu.edu)
- As of 2020, personal bankers or tellers make an average of $32,620 per year, according to the BLS. (wgu.edu)
- This field is expected to grow about 7% by 2028, a bit faster than the national average for job growth. (wgu.edu)
- Our program is 100% engineered for your success. (online.uc.edu)
- The BLS says that financial services jobs like banking are expected to grow 4% by 2030, about as fast as the national average. (wgu.edu)
External Links
How To
How do you implement Quality Management Plans (QMPs)?
QMP (Quality Management Plan), introduced in ISO 9001,2008, provides a systematic method for improving processes, products, or services through continuous improvement. It helps to improve customer satisfaction and product/service quality by continuously measuring, analyzing, controlling and improving.
QMP is a standard way to improve business performance. QMP's goal is to improve service delivery and production. QMPs should encompass all three components - Products and Services, as well as Processes. When the QMP includes only one aspect, it is called a "Process" QMP. QMP stands for Product/Service. The QMP that focuses on customer relationships is known as the "Customer" QMP.
There are two key elements to implementing a QMP: Strategy and Scope. These elements are as follows:
Scope: This defines what the QMP will cover and its duration. For example, if you want to implement a QMP that lasts six months, then this scope will outline the activities done during the first six.
Strategy: This describes the steps taken to achieve the goals set out in the scope.
A typical QMP consists of 5 phases: Planning, Design, Development, Implementation, and Maintenance. Below is a description of each phase:
Planning: In this stage the QMP's objectives and priorities are established. In order to fully understand and meet the needs of all stakeholders involved in this project, they are consulted. Once the objectives and priorities have been identified, it is time to plan the strategy to achieve them.
Design: In this stage, the design team designs the vision and mission, strategies, as well as the tactics that will be required to successfully implement the QMP. These strategies are implemented by the development of detailed plans and procedures.
Development: Here, the development team works towards building the necessary capabilities and resources to support the implementation of the QMP successfully.
Implementation: This refers to the actual implementation or the use of the strategies planned.
Maintenance: This is an ongoing procedure to keep the QMP in good condition over time.
Additionally, the QMP should include additional items:
Stakeholder Involvement: Stakeholders are important for the success of the QMP. They should be involved in planning, design, development and implementation of the QMP.
Project Initiation: The initiation of any project requires a clear understanding of the problem statement and the solution. Also, the initiator should understand why they are doing it and what they expect.
Time frame: The QMP's timeframe is critical. A simple version is fine if you only plan to use the QMP for a brief period. However, if you have a long-term commitment, you may require more elaborate versions.
Cost Estimation. Cost estimation is another crucial component of QMP. You cannot plan without knowing how much money you will spend. It is therefore important to calculate the cost before you start the QMP.
QMPs should not be considered a static document. It changes with the company. It should be reviewed on a regular basis to ensure that it is still meeting the company's needs.