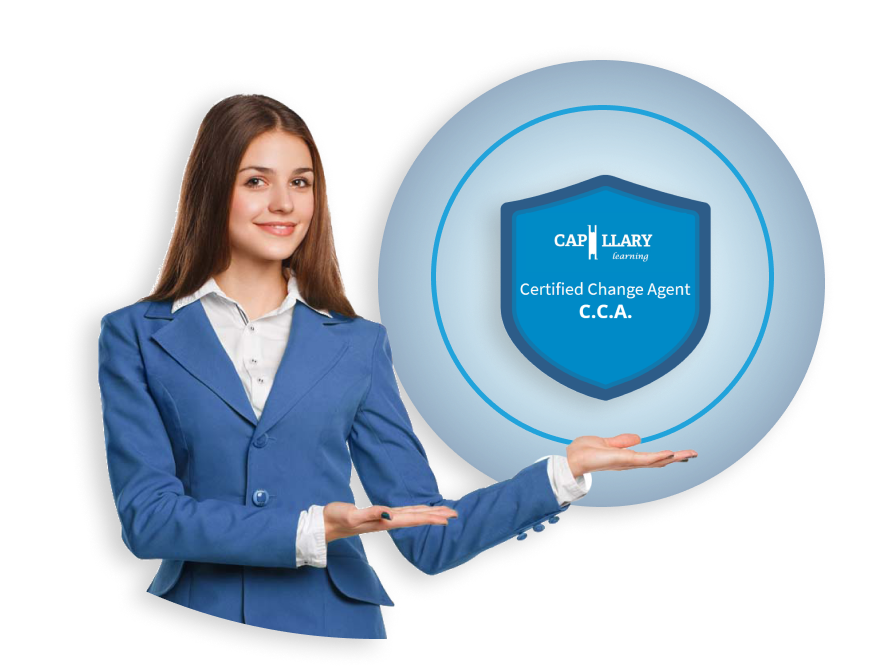
It is possible to achieve the desired results using a continuous improvements methodology. This method involves iterative design processes over multiple generations. It is also known as Lean Six Sigma. This article will cover one variation of the PDSA method based on SIPOC analysis. The application of the PDSA technique is explained in the context a engineering design studio.
Lean Six Sigma
Lean Six Sigma, a method for continuous improvement, focuses on making processes more predictable and simpler. A simpler process will result in fewer errors and lower risk of process failures. The statistical process control (SPC), techniques are used to control process variables. This improves performance. It can be used to improve any process, product, or service. The company must establish clear measurable characteristics and use data to guide the changes.
PDSA
The PDSA continuous-improvement methodology is a loop of process design and analysis that then leads to action to improve a process. The study phase, also known as the initial phase, of PDSA evaluates the effects of an experimental improvement relative to the expected results. This step allows the team to determine if the improvement was a success. This step will allow the team to conduct analysis. They may use control charts to distinguish expected from special cause variation.
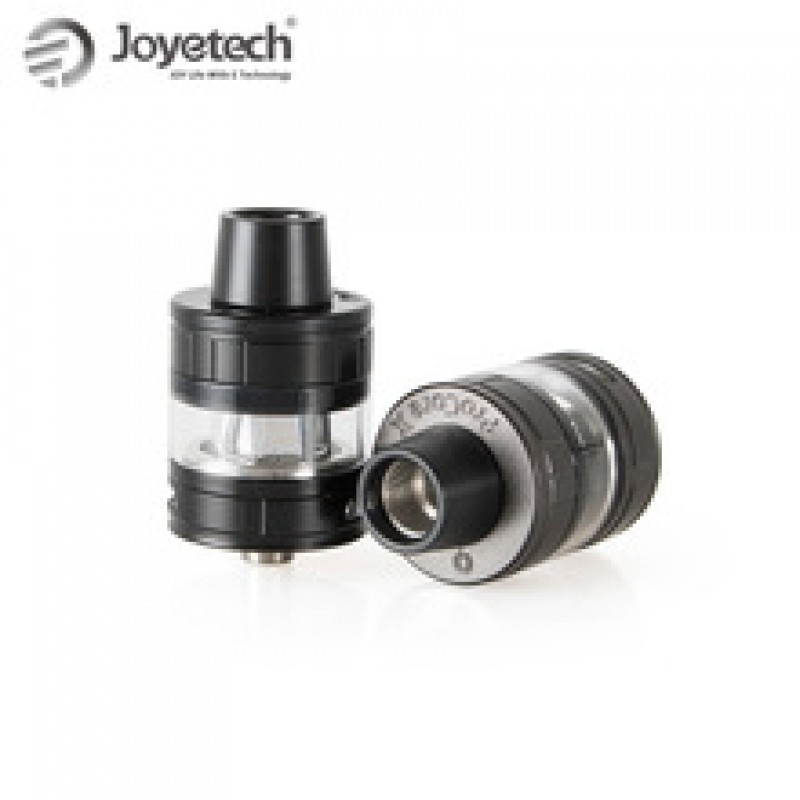
Variation of PDSA
PDSA is a method for continuous improvement and problem solving, with a defined focus and measurable targets. The process starts with careful planning. After that, the next step is to take effective action. Each idea is then tested for feasibility and sustainability. The project team makes sure that any improvement is sustainable by measuring the results.
PDSA based SIPOC analysis
SIPOC analysis can be a valuable tool to improve business processes. It's an easy way to categorize data into five categories. SIPOC diagrams provide an overview of all the processes and help teams to understand them better. They can also be used to help focus discussions.
PDSA based DMAIC
Businesses looking to improve the efficiency of their processes will benefit from continuous improvement techniques that follow DMAIC. These methodologies are straightforward and structured. They help organizations to understand inefficient processes, eliminate them, and achieve measurable and lasting results. Organizations may not be able to identify which changes have the greatest impact on their bottom line. They may also have difficulty implementing effective controls.
PDSA based on kanban board
Kanban boards have many great benefits. For example, they allow you to visualize work in progress, assign tasks to different team members, and include attachments or images for each task. You can also control how much work is done and when it is finished.
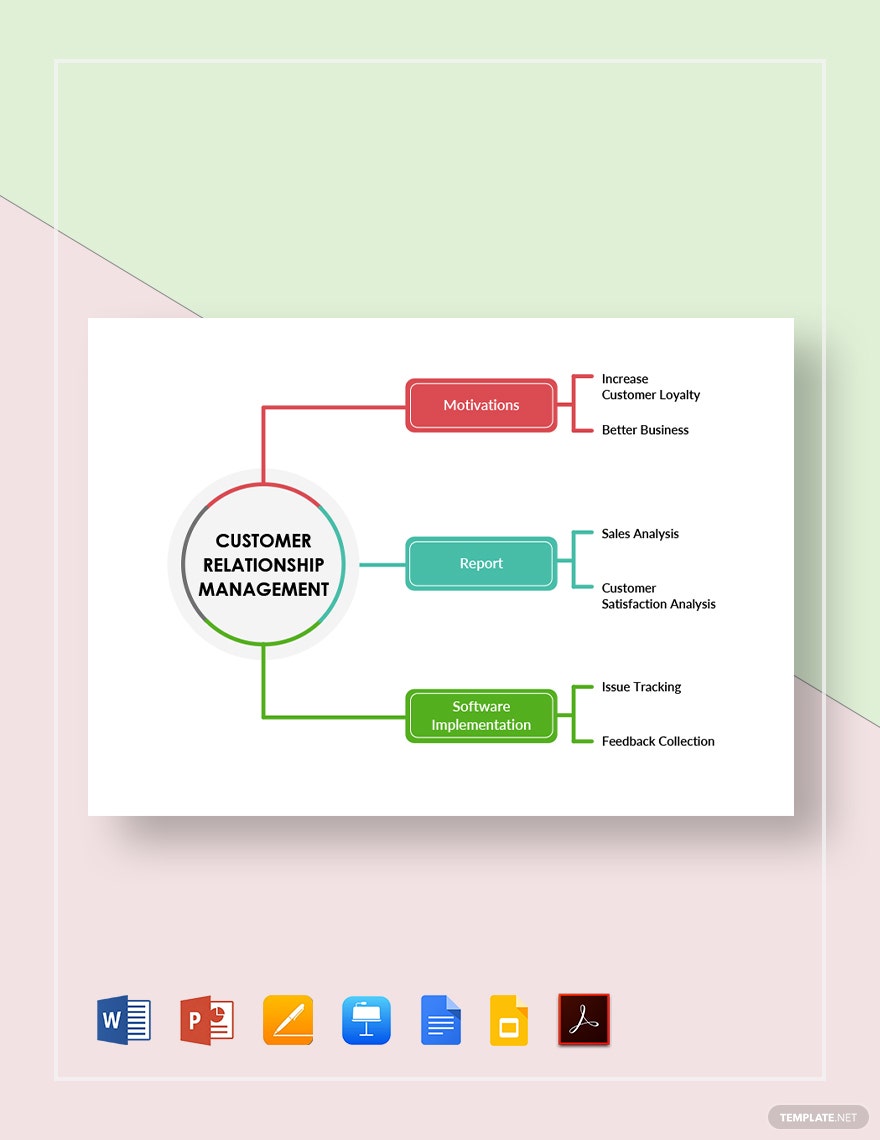
Kaizen based SIPOC analysis
The SIPOC structure is a powerful tool for improving process performance. It can help define the boundaries of a project, gather information, and then present that information in a simple and understandable way. It is often used to identify process variations that affect KVIPs, or key performance indicators, and is especially useful in the Define phase of DMAIC methodologies. It aids teams and stakeholders in planning improvements to improve processes.
PDSA based PDSA variant
Continuous improvement methodology PDSA uses the principle of continuous comparison between actual and expected results. The PDSA process measures the actual results of an improvement experiment against the expected results, and the reality of the implementation is compared with the plan. The data is then analyzed by the team to determine if the experiment resulted in measurable improvements. This data is usually categorized using a chart called a "control chart", to help distinguish between expected variations and special causes.
FAQ
What are the steps of the management decision-making process?
Managers face complex and multifaceted decision-making challenges. It includes many factors such as analysis, strategy planning, implementation and measurement. Evaluation, feedback and feedback are just some of the other factors.
It is important to remember that people are human beings, just like you. They make mistakes. As such, there are always opportunities for improvement, especially when you put in the effort to improve yourself.
This video explains the process of decision-making in Management. We will discuss the various types of decisions, and why they are so important. Every manager should be able to make them. The following topics will be covered.
How does a manager develop his/her management skills?
Through demonstrating good management skills at every opportunity
Managers must monitor the performance of subordinates constantly.
It is important to take immediate action if your subordinate doesn't perform as expected.
You should be able pinpoint what needs to improve and how to fix it.
What are the 4 major functions of management
Management is responsible to plan, organize, direct, and control people and resources. It includes creating policies and procedures, as well setting goals.
Management assists an organization in achieving its goals by providing direction, coordination and control, leadership, motivation, supervision and training, as well as evaluation.
Management has four primary functions:
Planning - Planning refers to deciding what is needed.
Organizing: Organizing refers to deciding how things should work.
Directing - Directing is when you get people to do what you ask.
Controlling - This is the ability to control people and ensure that they do their jobs according to plan.
What are management concepts?
Management concepts are the principles and practices used by managers to manage people, resources. These include topics such as human resource policies and job descriptions, performance assessments, training programs and employee motivation.
Which kind of people use Six Sigma
Six Sigma will most likely be familiar to people who have worked in statistics and operations research. Anyone involved in business can benefit.
This requires a lot of dedication, so only people with great leadership skills can make the effort to implement it.
What is Six Sigma?
It's a method for quality improvement that focuses on customer service as well as continuous learning. The goal is to eradicate defects through statistical techniques.
Motorola created Six Sigma as part of their efforts to improve manufacturing processes in 1986.
The idea spread quickly throughout the industry, and today, many organizations are using six sigma methods to improve product design, production, delivery, and customer service.
What are the 5 management processes?
The five stages of a business include planning, execution (monitoring), review, evaluation, and review.
Planning is about setting goals for your future. It involves setting goals and making plans.
Execution occurs when you actually carry out the plans. It is important to ensure that everyone follows the plans.
Monitoring is the act of monitoring your progress towards achieving your targets. Regular reviews of performance against budgets and targets should be part of this process.
Reviews take place at the end of each year. They allow for an assessment of whether all went well throughout the year. If not, then it may be possible to make adjustments in order to improve performance next time.
Evaluation takes place after the annual review. It helps identify what worked well and what didn't. It also provides feedback on how well people performed.
Statistics
- The profession is expected to grow 7% by 2028, a bit faster than the national average. (wgu.edu)
- 100% of the courses are offered online, and no campus visits are required — a big time-saver for you. (online.uc.edu)
- Your choice in Step 5 may very likely be the same or similar to the alternative you placed at the top of your list at the end of Step 4. (umassd.edu)
- Our program is 100% engineered for your success. (online.uc.edu)
- UpCounsel accepts only the top 5 percent of lawyers on its site. (upcounsel.com)
External Links
How To
How do you use the 5S in your office?
To make your workplace more efficient, organize everything. A tidy desk, a clean room and a well-organized workspace will help everyone be more productive. The five "S"'s (Sort. Shine. Clean. Separate. And Store) help to maximize space and ensure efficiency. These steps will be covered one-by-one and how they can work in any kind of setting.
-
Sort. Don't waste your time looking for things you already know are there. This means that you should put things where they are most useful. If you frequently refer back to something, put it near the place where you look up information or do research. Also, consider whether you really need it. If it isn't useful, get rid!
-
Shine. Do not keep anything that could possibly cause damage or injury to others. It is possible to have too many pens around and not be able to safely store them. It might mean investing in a pen holder, which is a great investment because you won't lose pens anymore.
-
Sweep. You should clean your surfaces often to prevent dirt and grime from building up. You might want to purchase dusting equipment in order to make sure that every surface is as clean as possible. To keep your workstation tidy, you can set aside an area for dusting and sweeping.
-
Separate. It will help you save time and make it easier to dispose of your trash. Trash cans are usually placed strategically throughout the office so that you can easily throw out the garbage without searching for it. You can take advantage of this location and place trash bags near each bin to make it easy to find what you are looking for.