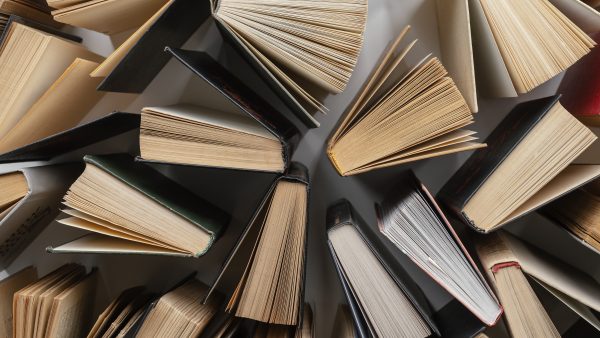
The cost of renting a roll-off container in Klamath Falls is something you might be interested in. Here are a few things to consider when evaluating dumpster rental companies: Dumpster sizes, recycling efforts, and Permit requirements. These questions will help you choose the right dumpster for your project.
Cost of renting a dumpster in Klamath Falls
When you need to rent a dumpster in Klamath Falls, OR, there are several factors that will affect the cost. The first is the size of the dumpster you require. A small home, for instance, does not usually require a large dumpster. A 20-yard dumpster is the best for large house cleanouts. This size dumpster is great for large items such a deck or shed.
You should also consider the time period for which the dumpster will be needed. You can usually use the dumpster rental company's services for a specified number of days. The cost of renting a dumpster will increase the longer you keep it.
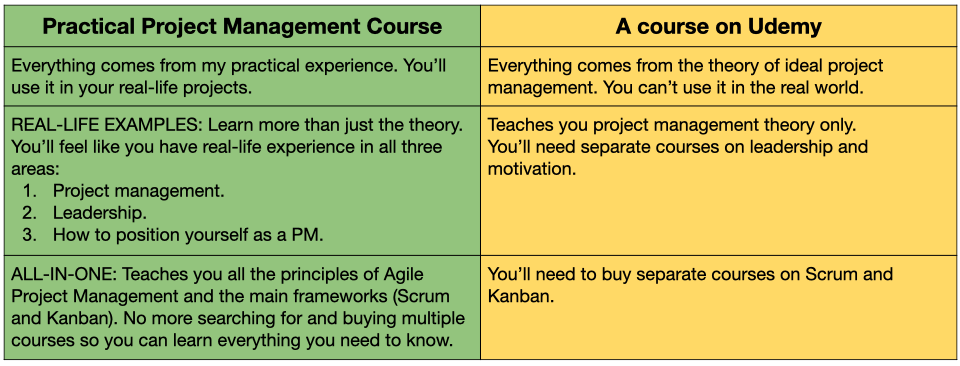
Dumpster sizes
You will need the correct dumpster size to manage your waste, whether it's at home, work, or on public property. An appropriate dumpster size will ensure you have enough room for your waste. A smaller dumpster may make loading or unloading more difficult. You can rent a dumpster for many reasons, including remodeling your home or junk removal.
Asking for quotes from different companies around your area is the best way find a low-cost dumpster rental. It will allow you to compare prices and pick the company that is right for your needs. It is important to remember that not all companies will charge extra for specific services such as pick up and drop off. Make sure to ask for a quote with all the services in order to get the best deal. There may be higher charges if you wish to throw out particular types of materials.
Recycling efforts
Valley Community for Recycling Solutions has a major push to increase recycling awareness, and increase the amount of recyclable materials. This includes the construction of a new drop off facility. Valley Community for Recycling Solutions will increase recycling awareness through education and outreach programs. It is also seeking $1 million in grants to finance the project.
The company is also planning to expand its recycling programs in Klamath Falls. This will be done in partnership with Waste Management and Klamath County Solid Waste. To facilitate the expansion, Reach purchased a recycling sorting line for about $5000 from a Roseburg facility.
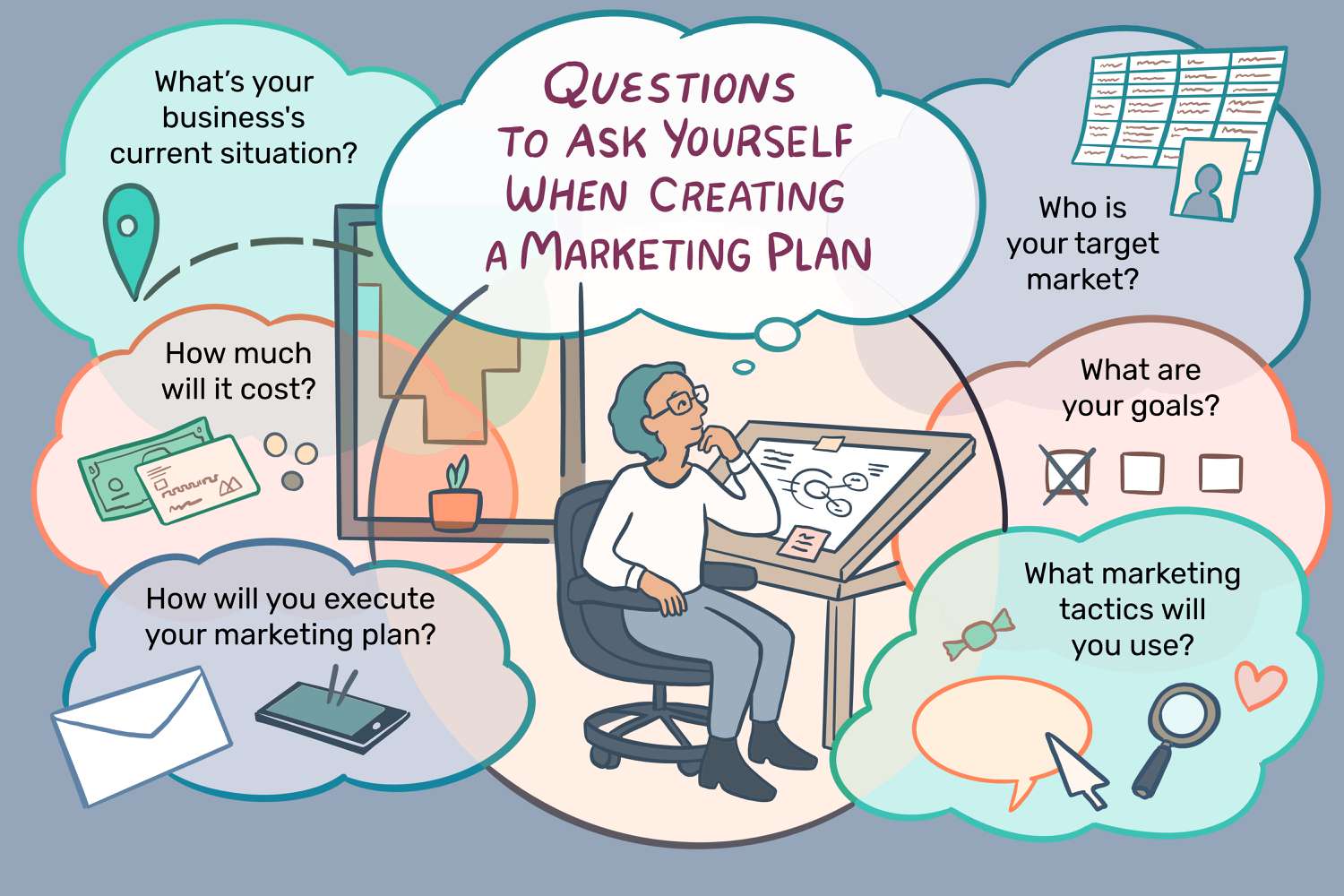
Permit requirements
The City of Klamath Falls’ Solid Waste Division is responsible to collect and dispose of solid waste from both homes and businesses. This division offers litter prevention, recycling, reuse, and recycling programs. Residential garbage customers can bring three bags or a 32 gallons of trash to the service station.
Klamath Falls' requirements for waste disposal vary depending on the type of waste. You may be required to obtain a permit if you're going to dispose of hazardous or putrescible waste. Hazardous waste, such as lead acid batteries, must be properly transported and disposed of. In addition, if you're disposing of hazardous materials, you'll need to follow the Department of Environmental Quality's requirements for hazard-free waste disposal.
FAQ
What are the 3 main management styles?
There are three types of management: participative, laissez faire, and authoritarian. Each style has strengths and flaws. Which style do your prefer? Why?
Authority - The leader is the one who sets the direction and expects everyone in the organization to follow it. This style is most effective when an organization is large, stable, and well-run.
Laissez-faire: The leader lets each person decide for themselves. This style works best when an organization is small and dynamic.
Participative - The leader listens to ideas and suggestions from everyone. This style is best for small organizations where everyone feels valued.
What is a basic management tool used in decision-making?
A decision matrix can be a simple, but effective tool to assist managers in making decisions. It helps them think systematically about all the options available to them.
A decision matrix allows you to represent alternatives as columns and rows. This allows one to see how each alternative impacts other options.
We have four options in this example. They are represented by the boxes to the left of the matrix. Each box represents a different option. The top row shows the status quo (the current situation), and the bottom row shows what would happen if nothing was done at all.
The effect of choosing Option 1 can be seen in column middle. It would increase sales by $2 million to 3 million in this instance.
The effects of options 2 and 3 are shown in the next columns. These are positive changes - they increase sales by $1 million and $500 thousand respectively. They also have negative consequences. Option 2, for example, increases the cost by $100 000 while Option 3 decreases profits by $200 000.
The last column shows you the results of Option 4. This will result in sales falling by $1,000,000
A decision matrix has the advantage that you don’t have to remember where numbers belong. You can just glance at the cells and see immediately if one given choice is better.
This is because your matrix has already done the hard work. It is as simple a matter of comparing all the numbers in each cell.
Here is an example how you might use the decision matrix in your company.
Decide whether you want to invest more in advertising. If you do, you'll be able to increase your revenue by $5 thousand per month. But, you will also incur additional expenses of $10 thousand per month.
Look at the cell immediately below the one that states "Advertising" to calculate the net investment in advertising. It's $15,000. Advertising is more valuable than its costs.
What are the five management process?
These five stages are: planning, execution monitoring, review and evaluation.
Planning is about setting goals for your future. It involves setting goals and making plans.
Execution is the actual execution of the plans. You need to make sure they're followed by everyone involved.
Monitoring is the act of monitoring your progress towards achieving your targets. Regular reviews of performance against budgets and targets should be part of this process.
Reviews take place at the end of each year. They give you an opportunity to review the year and assess how it went. If not then, you can make changes to improve your performance next year.
After the annual review, evaluation takes place. It helps to identify what went well and what didn’t. It also gives feedback on how well people did.
Why is Six Sigma so popular?
Six Sigma is easy to use and can lead to significant improvements. It can also be used to help companies identify and focus on the most important aspects of their business.
What is the best way to motivate your employees as a manager?
Motivation refers to the desire to perform well.
Doing something that is enjoyable can help you get motivated.
Or you can get motivated by seeing yourself making a contribution to the success of the organization.
If you are a doctor and want to be one, it will likely be more rewarding to see patients than to read medical books every day.
Another source of motivation is within.
One example is a strong sense that you are responsible for helping others.
Perhaps you enjoy working hard.
Ask yourself why you aren't feeling motivated.
Then think about how you can make your life more motivating.
How do you manage your employees effectively?
The key to effective management of employees is ensuring their happiness and productivity.
It is important to set clear expectations about their behavior and keep track of their performance.
Managers must set clear goals for their employees and themselves to achieve this goal.
They should communicate clearly to staff members. They need to communicate clearly with their staff.
They also need to keep records of their team's activities. These include:
-
What was achieved?
-
How much work did you put in?
-
Who did it?
-
It was done!
-
Why was this done?
This information can be used to monitor performance and evaluate results.
Statistics
- The profession is expected to grow 7% by 2028, a bit faster than the national average. (wgu.edu)
- As of 2020, personal bankers or tellers make an average of $32,620 per year, according to the BLS. (wgu.edu)
- Our program is 100% engineered for your success. (online.uc.edu)
- 100% of the courses are offered online, and no campus visits are required — a big time-saver for you. (online.uc.edu)
- UpCounsel accepts only the top 5 percent of lawyers on its site. (upcounsel.com)
External Links
How To
How can Lean Manufacturing be done?
Lean Manufacturing processes are used to reduce waste and improve efficiency through structured methods. They were created in Japan by Toyota Motor Corporation during the 1980s. The goal was to produce quality products at lower cost. Lean manufacturing focuses on eliminating unnecessary steps and activities from the production process. It is made up of five elements: continuous improvement, continuous improvement, just in-time, continuous change, and 5S. Pull systems are able to produce exactly what the customer requires without extra work. Continuous improvement refers to continuously improving existing processes. Just-intime refers the time components and materials arrive at the exact place where they are needed. Kaizen stands for continuous improvement. Kaizen can be described as a process of making small improvements continuously. The 5S acronym stands for sort in order, shine standardize and maintain. These five elements can be combined to achieve the best possible results.
Lean Production System
Six key concepts form the foundation of the lean production system:
-
Flow - The focus is on moving information and material as close as possible to customers.
-
Value stream mapping - Break down each stage in a process into distinct tasks and create an overview of the whole process.
-
Five S's – Sort, Put In Order Shine, Standardize and Sustain
-
Kanban is a visual system that uses visual cues like stickers, colored tape or stickers to keep track and monitor inventory.
-
Theory of constraints - identify bottlenecks during the process and eliminate them with lean tools like Kanban boards.
-
Just-in-time - deliver components and materials directly to the point of use;
-
Continuous improvement - incremental improvements are made to the process, not a complete overhaul.