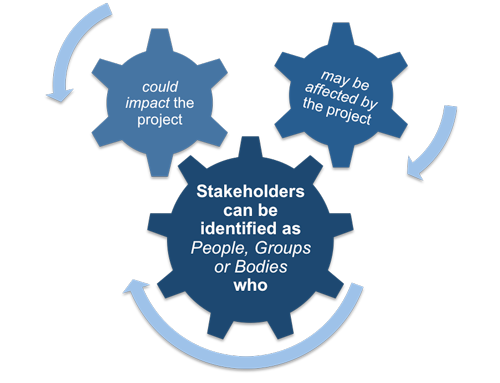
Accenture, one of the leading supply chain consultants worldwide, has acquired GRA logistics and supply-chain consulting firm GRA. Accenture's combination of these services allows it to meet the ever-changing demands of modern supply chains. Accenture's supply chains experts work with clients to deliver positive customer experiences. Accenture acquired Blue Horseshoe Group in addition to Xoomworks Group. In this article, we will explore the role of supply chain capability in modern business strategies.
Accenture's supply chain strategy
Accenture recently completed a global supply chain strategy to MedShare International, an Atlanta-based charity that distributes medical supplies in developing countries. The strategy aimed to optimize the entire supply chain from sourcing and procurement through warehouse operations and customer service. It will be implemented over several consecutive years with the aim of increasing the organization's profitability. MedShare is able to fulfill its mission of helping the poorest in the world and tackling the global crisis of health.
To satisfy the demands of customers, organizations need to redesign their supply chain networks in order for them to be customer-centric. Customer-centricity allows them to create hyper-personalized products and experiences by leveraging it. These networks are essential for a company's bottom line and the world at large. Accenture's supply chain strategy can help organizations accelerate their journey to customer-centricity. It identifies targeted commercial interventions, cash flow, and other ways to increase revenue.
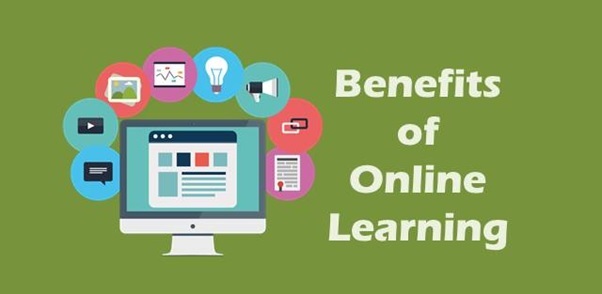
Accenture's acquisition Alfa Consulting
Accenture recently purchased a consulting firm that specializes in capital-intensive industry operations strategy. Alfa is based out of Spain with offices in Portugal and Spain. Alfa's focus is on supply chain management and analytic models for a variety of industries, including tech and energy. With the addition of Alfa to Accenture's growing global practice, it is expected that the company's clients will see increased efficiency and sustainability in their supply chain operations.
Accenture's Supply Chain & Operations team will be incorporating Alfa Consulting. The company helps clients with customer-centric supply chain segmentation, sourcing transformations and sourcing optimizations. Accenture will continue to offer its value-based workforce planning and maintenance practices in addition to Alfa's supply chains consulting services. Accenture's Iberia supply chain capabilities will be enhanced by the acquisition. Accenture is a strong player in the U.S. but Alfa remains a major player in Europe.
Accenture acquires Xoomworks Group
Accenture announced its acquisition of Xoomworks a technology and innovative consultancy. Accenture's Closed Loop Spend Administration capabilities have been strengthened. This gives clients unparalleled visibility and insight across all price classes. It enhances the ecosystem partners' expertise in digital innovation management. With this acquisition, Accenture is adding a new talent pool to its global talent pool. It employs more than 62,000 people around the globe, making it one of the most important consulting firms in the country.
The Xoomworks Group was founded in 2000, and operates two businesses, Xoomworks Procurement and Xoomworks Technology. The company's Procurement division provides digital procurement and sourcing solutions to clients from all industries. Xoomworks Procurement is home to more than 250 employees in the UK and France. Accenture believes the acquisition will enhance its Closed Loop Spend Management capabilities. This allows clients to achieve substantial, sustainable cost savings.
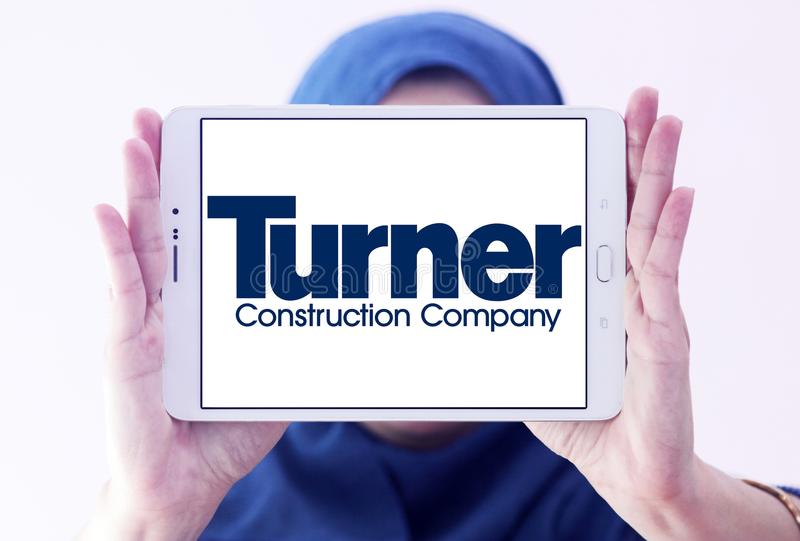
Accenture's acquisition of Blue Horseshoe
Accenture recently announced the acquisition of Blue Horseshoe, a supply chain strategy and integration company. Blue Horseshoe was founded in 2001 and helps clients in many industries to define their enterprise strategies, connect their applications, and optimize their supply chains. The company will combine offices in North Carolina (Ohio) and Estonia to offer a wide range supply chain solutions. You can read on for more information about the acquisition.
Accenture has made a number of acquisitions in recent years. This acquisition is just the latest. Accenture, which is a consulting firm, has been increasingly active within the M&A market. It acquires numerous companies each year. Accenture had previously purchased data analytics companies as well as ad agencies. Recently, however, the company bought LEXTA, a strategic IT consultant. Its most recent deal is the third largest ever in Accenture's history.
FAQ
What does it mean to say "project management"
That is the management of all activities associated with a project.
We include defining the scope of the project, identifying the requirements, preparing the budget, organizing the project team, scheduling the work, monitoring progress, evaluating results, and closing down the project.
What are the 3 main management styles?
The three basic management styles are: authoritarian, laissez-faire, and participative. Each style has its own strengths and weaknesses. Which style do you prefer? Why?
Autoritarian – The leader sets the direction for everyone and expects them to follow. This style works best in large organizations that are stable and well-organized.
Laissez-faire: The leader lets each person decide for themselves. This style is most effective when the organization's size and dynamics are small.
Participative – The leader listens and takes in ideas from all. This style works best in smaller organizations where everyone feels valued.
What are management concepts?
Management concepts are the principles and practices used by managers to manage people, resources. They cover topics like job descriptions (job descriptions), performance evaluations, training programmes, employee motivation and compensation systems.
Statistics
- Hire the top business lawyers and save up to 60% on legal fees (upcounsel.com)
- The BLS says that financial services jobs like banking are expected to grow 4% by 2030, about as fast as the national average. (wgu.edu)
- The profession is expected to grow 7% by 2028, a bit faster than the national average. (wgu.edu)
- 100% of the courses are offered online, and no campus visits are required — a big time-saver for you. (online.uc.edu)
- Our program is 100% engineered for your success. (online.uc.edu)
External Links
How To
How can you implement the Kaizen technique?
Kaizen means continuous improvement. The term was coined in the 1950s at Toyota Motor Corporation and refers to the Japanese philosophy emphasizing constant improvement through small incremental changes. It's a team effort to continuously improve processes.
Kaizen is one the most important methods of Lean Manufacturing. Employees responsible for the production line should identify potential problems in the manufacturing process and work together to resolve them. This way, the quality of products increases, and the cost decreases.
Kaizen is the idea that every worker should be aware of what is going on around them. So that there is no problem, you should immediately correct it if something goes wrong. It is important that employees report any problems they see while on the job to their managers.
Kaizen follows a set of principles. Always start with the end product in mind and work our way back to the beginning. To improve our factory, for example, we need to fix the machines that produce the final product. First, we fix machines that produce components. Next, we fix machines that produce raw material. Finally, we repair the workers who are directly involved with these machines.
This approach is called 'kaizen' because it focuses on improving everything steps by step. When we are done fixing the whole factory, we go back to the beginning and continue until we reach perfection.
Before you can implement kaizen into your business, it is necessary to learn how to measure its effectiveness. There are many ways you can determine if kaizen has been implemented well. Another method is to see how many defects are found on the products. Another way is to check how much productivity has grown since kaizen was implemented.
If you want to find out if your kaizen is actually working, ask yourself why. Was it just because it was the law or because you wanted to save money? Did you really think that it would help you achieve success?
Let's say you answered yes or all of these questions. Congratulations! You're ready to start kaizen.