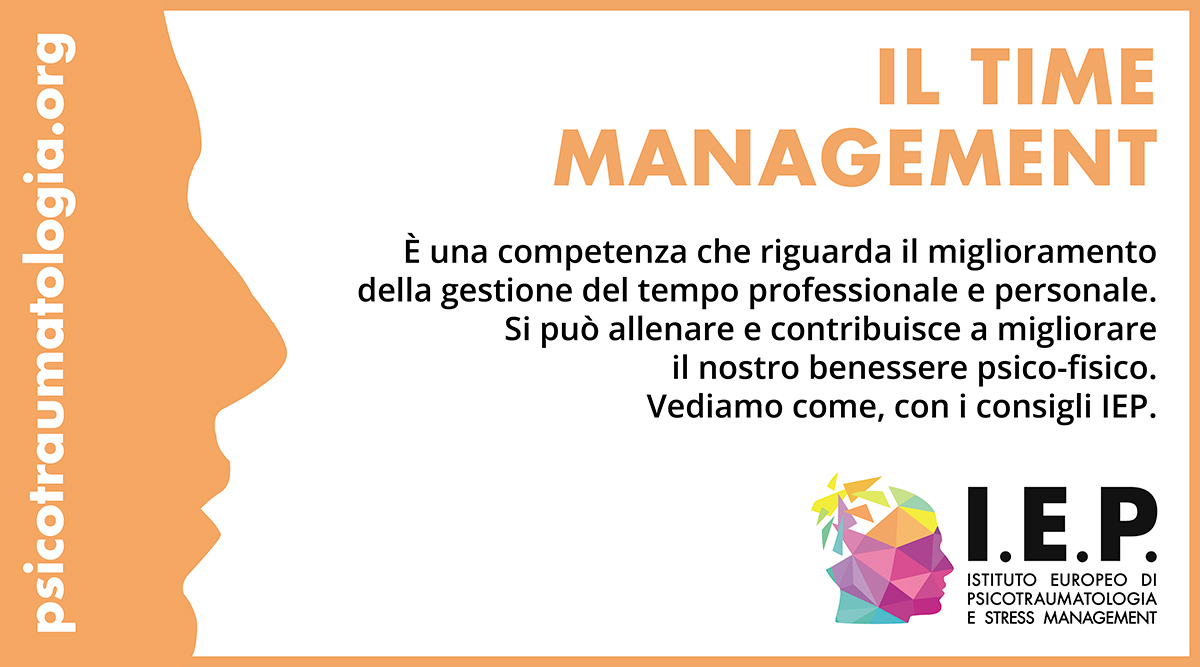
There are four stages that a person who is going through a transformation will experience. These are: Rejection, Resistance and Exploration. And finally, Commitment. Each stage has its own challenges. These stages can be difficult to navigate. You need to identify what you're replacing and what you keep. These will help you work through the transition process.
Denialism
The four stages of change we experience are usually denial, acceptance, commitment and shock. The Stage of Shock can be described as a brief-term reaction. It involves a dip in productivity as the mind processes the news and reality. The next stage is called the Stage of Denial, which can last for a long time. If you're unable to move on from this stage, it can lead to an eventual loss of touch with reality.
This phase is when people are trying to maintain the status quo and avoid the possibility of change. People may feel angry or sad as their energy fluctuates and performance is affected. It's essential to have effective support structures during this phase. But, when you face the fact that you will be changing, you need to be strong enough to take control of your future.

Resistance
It was necessary to study the influence of temperature on the resistance for a nickel alloy at the ferromagnetic stage transition. A large hydrostatic cubic multiple-anvil pressure chamber was used to measure the nickel resistance at 25 and 45 Kbar. This enabled the creation of a computerized, real time measurement system. These measurements revealed a high level of agreement between resistance measurements at atmospheric pressure and high pressure measurements. In addition, they showed that the critical temperature, Tc, increases with pressure at a rate of 0.193+-0.013 K/kbar.
These measurements have revealed that the resistance in phase transitions is a result of the T-dependent gap function. This resistance is constant if the temperature is sufficiently low. When the temperature is above the critical temperature, however, the resistance in intergranular regions increases. This feature's sensitiveness shows that resistive features at the junction are SNS.
Exploration
The Exploration Phase of a Transition is an important time to increase organizational capacity and learn about new programs or practices. This phase involves engaging community stakeholders and professionals in the implementation process. The purpose of this phase is to identify the specific needs of the program/practice, and then develop solutions. The Exploration Phase is where you identify the most important components and define the scope of the transition.
A team called the Implementation Team is responsible for creating, scaling up, and maintaining usable innovations. These teams integrate drivers, stages, and improvement cycles into a holistic process. This could be a single person that brings new ways to work to the company. But it could also include the formation of a team that can be key to the sustainability process.
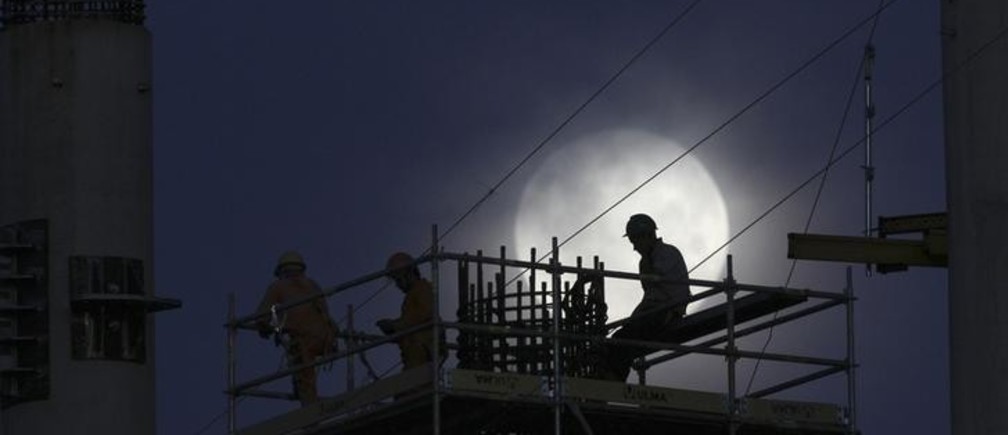
Commitment
Many phases accompany the commitment to a change effort. These phases are characterized by a lack of setting and skills, and by an insufficient capacity for the changes being initiated. These phases will pass and people will either move to a new stage or continue in the current situation. Individuals will make more progress if they are committed to a change initiative.
The Contact Stage is where employees are exposed to the new initiative. This stage is where employees are first exposed to the change initiative. This exposure may be in the form of a poor financial statement, a meeting with the CEO, or a meeting with senior staff.
FAQ
What is a simple management tool that aids in decision-making and decision making?
The decision matrix is a powerful tool that managers can use to help them make decisions. It allows them to think through all possible options.
A decision matrix represents alternatives in rows and columns. This allows you to easily see how each choice affects others.
This example shows four options, each represented by the boxes on either side of the matrix. Each box represents a different option. The top row represents the current state of affairs, and the bottom row is indicative of what would happen in the event that nothing were done.
The middle column shows the effect of choosing Option 1. In this example, it would lead to an increase in sales of between $2 million and $3 million.
The following columns illustrate the impact of Options 2 and 3. These positive changes result in increased sales of $1 million and $500,000. However, these also involve negative consequences. Option 2 increases the cost of goods by $100,000. Option 3 decreases profits and makes them less attractive by $200,000.
Finally, the last column shows the results of choosing Option 4. This results in a decrease of sales by $1,000,000
A decision matrix has the advantage that you don’t have to remember where numbers belong. You can just glance at the cells and see immediately if one given choice is better.
This is because the matrix has done all the hard work. Simply compare the numbers within the cells.
Here's an example showing how you might use a Decision Matrix in your business.
It is up to you to decide whether to spend more money on advertising. You'll be able increase your monthly revenue by $5000 if you do. You will still have to pay $10000 per month in additional expenses.
If you look at the cell that says "Advertising", you can see the number $15,000. Advertising is worth much more than the investment cost.
How can a manager enhance his/her leadership skills?
Good management skills are essential for success.
Managers must continuously monitor the performance levels of their subordinates.
You must quickly take action if your subordinate fails to perform.
You should be able pinpoint what needs to improve and how to fix it.
What is TQM and how can it help you?
When manufacturing companies realized that price was not enough to compete, the industrial revolution brought about the quality movement. They needed to improve quality and efficiency if they were going to remain competitive.
Management developed Total Quality Management to address the need for improvement. It focused on all aspects of an organisation's performance. It included continual improvement processes, employee involvement, customer satisfaction, and customer satisfaction.
What are the 3 main management styles?
These are the three most common management styles: participative (authoritarian), laissez-faire (leavez-faire), and authoritarian. Each style has its advantages and disadvantages. Which style do your prefer? Why?
Authority - The leader is the one who sets the direction and expects everyone in the organization to follow it. This style works best if the organization is large and stable.
Laissez-faire: The leader lets each person decide for themselves. This style works best when an organization is small and dynamic.
Participative – Leaders are open to suggestions and ideas from everyone. This approach works best in small organizations where everyone feels valued.
Statistics
- UpCounsel accepts only the top 5 percent of lawyers on its site. (upcounsel.com)
- The average salary for financial advisors in 2021 is around $60,000 per year, with the top 10% of the profession making more than $111,000 per year. (wgu.edu)
- The BLS says that financial services jobs like banking are expected to grow 4% by 2030, about as fast as the national average. (wgu.edu)
- As of 2020, personal bankers or tellers make an average of $32,620 per year, according to the BLS. (wgu.edu)
- This field is expected to grow about 7% by 2028, a bit faster than the national average for job growth. (wgu.edu)
External Links
How To
How can Lean Manufacturing be done?
Lean Manufacturing techniques are used to reduce waste while increasing efficiency by using structured methods. They were created in Japan by Toyota Motor Corporation during the 1980s. The primary goal was to make products with lower costs and maintain high quality. Lean manufacturing eliminates unnecessary steps and activities from a production process. It is composed of five fundamental elements: continuous improvement; pull systems, continuous improvements, just-in–time, kaizen, continuous change, and 5S. It is a system that produces only the product the customer requests without additional work. Continuous improvement means continuously improving on existing processes. Just-in–time refers when components or materials are delivered immediately to their intended destination. Kaizen means continuous improvement. Kaizen involves making small changes and improving continuously. Finally, 5S stands for sort, set in order, shine, standardize, and sustain. These five elements work together to produce the best results.
Lean Production System
The lean production system is based on six key concepts:
-
Flow - focus on moving material and information as close to customers as possible;
-
Value stream mapping: This is a way to break down each stage into separate tasks and create a flowchart for the entire process.
-
Five S's: Sort, Shine Standardize, Sustain, Set In Order, Shine and Shine
-
Kanban – visual signals like colored tape, stickers or other visual cues are used to keep track inventory.
-
Theory of constraints: identify bottlenecks in your process and eliminate them using lean tools, such as kanban board.
-
Just-in time - Get components and materials delivered right at the point of usage;
-
Continuous improvement - incremental improvements are made to the process, not a complete overhaul.