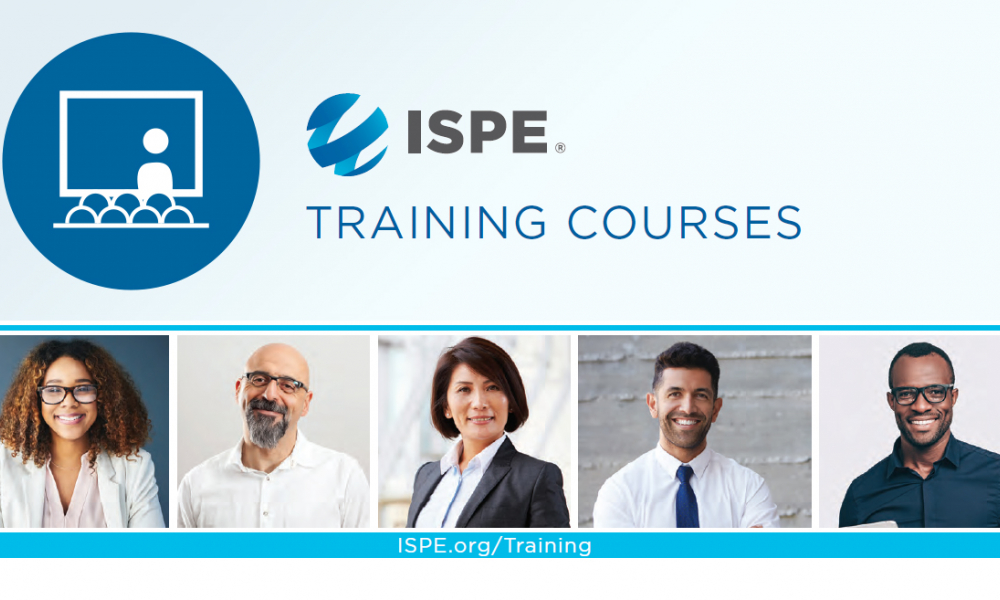
You can pursue a career working in labor relations by becoming a labor relation specialist. This job requires a bachelor's degree. However, you can earn a master's degree. In the job description of a labor relations specialist, it should specify required and preferred qualifications. The job description should include information about the education and certification of a labor relations specialist.
A labor relations specialist has common duties
A labor relations specialist must have experience in human resource management. He or she should also be able to problem-solve and communicate well. A labor relations specialist should be proficient in spreadsheets and technology. It takes just minutes to create a labor relations specialist resume. Our labor relations specialist resume examples can be used as a guide for creating your resume.
A bachelor's degree is the most common requirement for labor relations specialists. Education requirements for labor relations specialists can vary, from a high school diploma up to a master's. Labor relations specialists are responsible for creating a link between workers and managers.
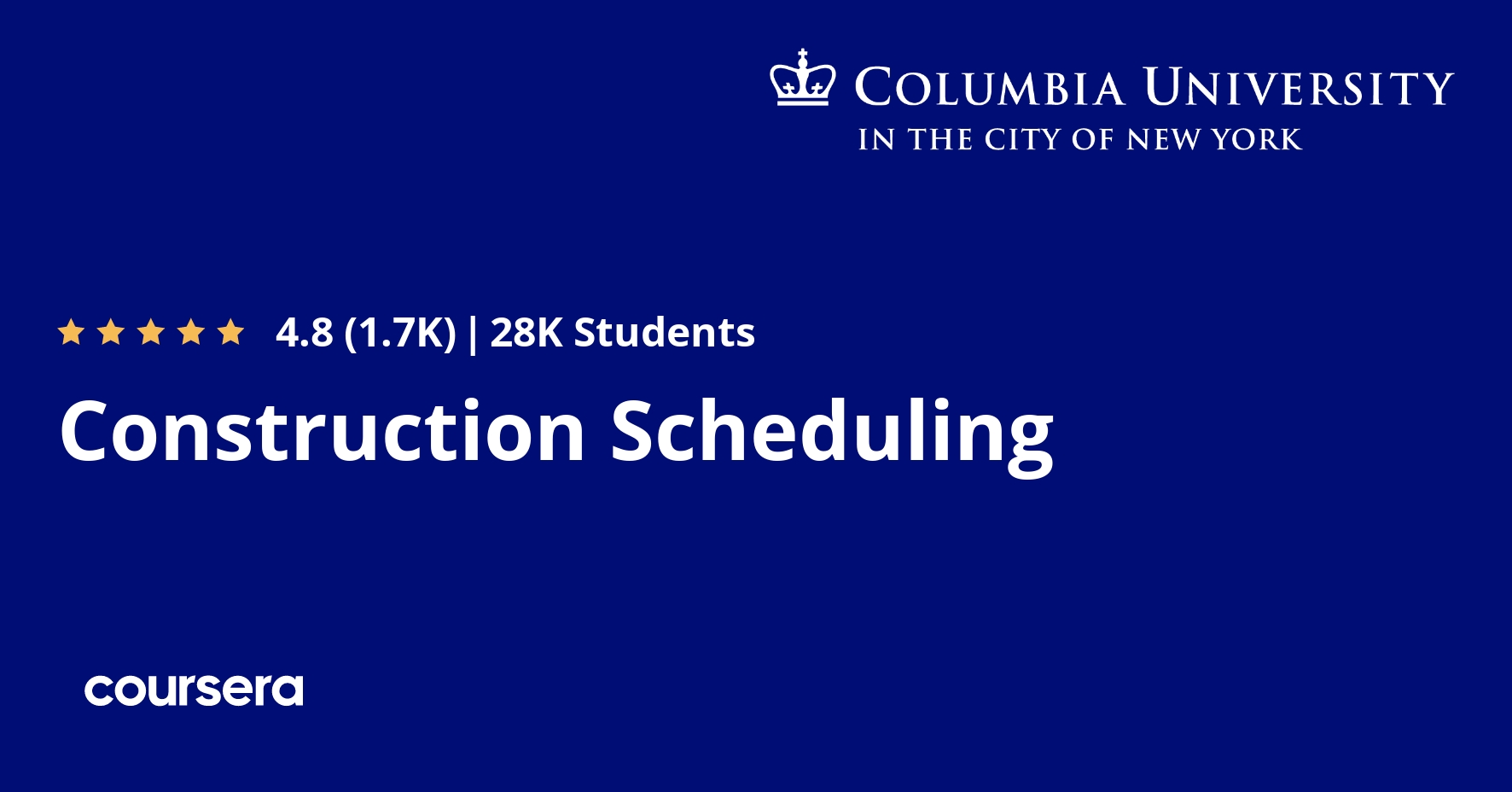
Education necessary
It is crucial to be familiar with the employment laws before you embark on this career path. These laws include the Fair Labor Standards Act (Fair Labor Standards Act) and the National Labor Relations Act (National Labor Relations Act). To become a labor-relations specialist, you must have a good understanding of these laws. You can enroll in both undergraduate and graduate labor law courses. You can also pursue certifications in this field. These certifications are not required, but they will help you gain a better understanding and focus on specific areas.
A labor relations specialist must have exceptional communication skills, regardless of their education. They should be able to effectively communicate with both managers and employees. They must also have excellent conflict resolution skills. To find the right skills and education required for the labor relations specialist position, it is important to review the job description.
Earning potential
There is an increasing demand for labor relations specialists as the 21st century progresses. There are many opportunities for labor relations specialists every year, even though the profession is losing more people. An estimated 70,000 positions will open between now and 2029. Being a labor relation specialist is a great way to start your career in the field. It is possible to gain work experience from other professions and get a degree. Competitors will be able to communicate effectively with clients and manage negotiations if they are able to do so.
For labor relations specialists, the earning potential ranges between $64,800 to $128,000. Salary depends on experience and location. However, on average, labor relations specialists make $74,877 per year. New Jersey and the Utilities sector are the highest-paying areas for labor relations specialists.
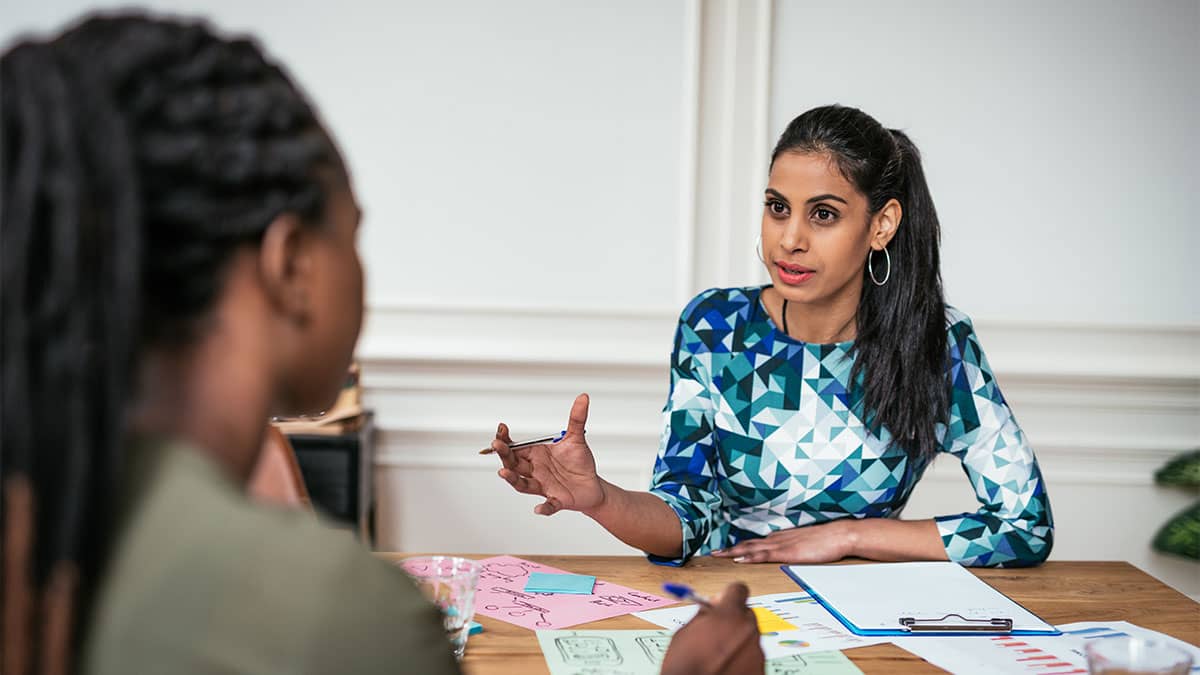
Job outlook
According to U.S. Bureau of Labor Statistics. the job outlook is generally negative for labor relations experts. This is due in part to the decrease in the number and quality of unions. It is likely that this will result in a reduction of employment opportunities. Candidates with specialized certification and higher education should still have the best job chances.
A bachelor's degree is required to work in human resources. This degree focuses both on leadership in business and the effective management employees. It also addresses current trends and issues in the human resource sector, including labor relations.
FAQ
What are the steps involved in making a decision in management?
Managers face complex and multifaceted decision-making challenges. It involves many factors, such as analysis and strategy, planning, execution, measurement, evaluation, feedback etc.
Remember that people are humans just like you, and will make mistakes. This is the key to managing them. There is always room to improve, especially if your first priority is to yourself.
We explain in this video how the Management decision-making process works. We discuss the different types of decisions and why they are important, every manager should know how to navigate them. You'll learn about the following topics:
What is Kaizen?
Kaizen is a Japanese term which means "continuous improvement." This philosophy encourages employees to continually look for ways to improve the work environment.
Kaizen is based upon the belief that each person should be capable of doing his or her job well.
What is Six Sigma?
It's an approach to quality improvement that emphasizes customer service and continuous learning. The goal is to eliminate defects by using statistical techniques.
Motorola developed Six Sigma in 1986 to help improve its manufacturing processes.
The idea quickly spread in the industry. Many organizations today use six-sigma methods to improve product design and production, delivery and customer service.
Why is it important that companies use project management methods?
Project management techniques can be used to ensure smooth project execution and meeting deadlines.
Because most businesses depend heavily on project work to produce goods or services,
These projects must be managed efficiently and effectively by companies.
Companies can lose time, money, and reputation if they don't have a good project management system.
How to manage employees effectively?
Achieving employee happiness and productivity is key to managing them effectively.
It also means having clear expectations of their behavior and keeping track of their performance.
To do this successfully, managers need to set clear goals for themselves and for their teams.
They need to communicate clearly with staff members. They must communicate clearly with staff members.
They must also keep track of the activities of their team. These include:
-
What was accomplished?
-
What was the work involved?
-
Who did it all?
-
What was the moment it was completed?
-
Why was it done?
This information is useful for monitoring performance and evaluating the results.
Statistics
- Our program is 100% engineered for your success. (online.uc.edu)
- This field is expected to grow about 7% by 2028, a bit faster than the national average for job growth. (wgu.edu)
- As of 2020, personal bankers or tellers make an average of $32,620 per year, according to the BLS. (wgu.edu)
- The average salary for financial advisors in 2021 is around $60,000 per year, with the top 10% of the profession making more than $111,000 per year. (wgu.edu)
- 100% of the courses are offered online, and no campus visits are required — a big time-saver for you. (online.uc.edu)
External Links
How To
What is Lean Manufacturing?
Lean Manufacturing techniques are used to reduce waste while increasing efficiency by using structured methods. They were created in Japan by Toyota Motor Corporation during the 1980s. The main goal was to produce products at lower costs while maintaining quality. Lean manufacturing seeks to eliminate unnecessary steps and activities in the production process. It is made up of five elements: continuous improvement, continuous improvement, just in-time, continuous change, and 5S. Pull systems are able to produce exactly what the customer requires without extra work. Continuous improvement is the continuous improvement of existing processes. Just-in time refers to components and materials being delivered right at the place they are needed. Kaizen means continuous improvement. Kaizen involves making small changes and improving continuously. Fifth, the 5S stand for sort, set up in order to shine, standardize, maintain, and standardize. To achieve the best results, these five elements must be used together.
Lean Production System
The lean production system is based on six key concepts:
-
Flow - focus on moving material and information as close to customers as possible;
-
Value stream mapping- This allows you to break down each step of a process and create a flowchart detailing the entire process.
-
Five S's, Sort, Set in Order, Shine. Standardize. and Sustain.
-
Kanban is a visual system that uses visual cues like stickers, colored tape or stickers to keep track and monitor inventory.
-
Theory of constraints - identify bottlenecks in the process and eliminate them using lean tools like kanban boards;
-
Just-in-time delivery - Deliver components and materials right to your point of use.
-
Continuous improvement is making incremental improvements to your process, rather than trying to overhaul it all at once.