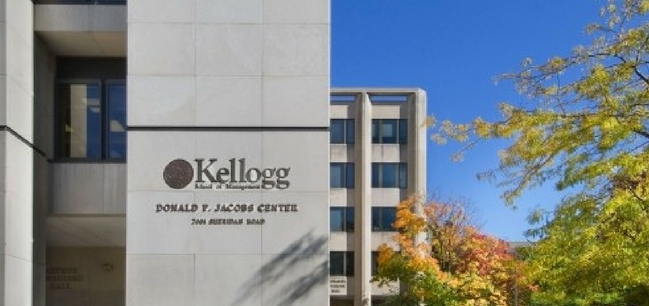
HR systems are vital for any business. But, using a single system is not always the best option. You should consider many factors when selecting a system. These factors include process design, cost, embedded workflows, as well as cost. Here are some tips to help make the right decision.
Process design
Creating an effective process design for HR systems requires careful consideration of the business requirements of the company. When creating an HR system, HR leaders should consider the culture and types of employees. Managers must encourage employee ideas and have a flexible approach to changes. Although the ideal HR system is not the most efficient for a business, managers must be flexible to find the right one for them.
Embedded workflows
Workflows allow HR departments to automate tasks by allowing them to use workflows within their HR systems. HR departments can automate processes to allow them to focus on more difficult tasks, and streamline their HR data. They can store information about employees, including personal information. This data can help HR departments with employee development. They can create an organisational structure that is based on job duties or reporting structures. This allows them to create an organogram that makes it easy for people to see who reports to which person.
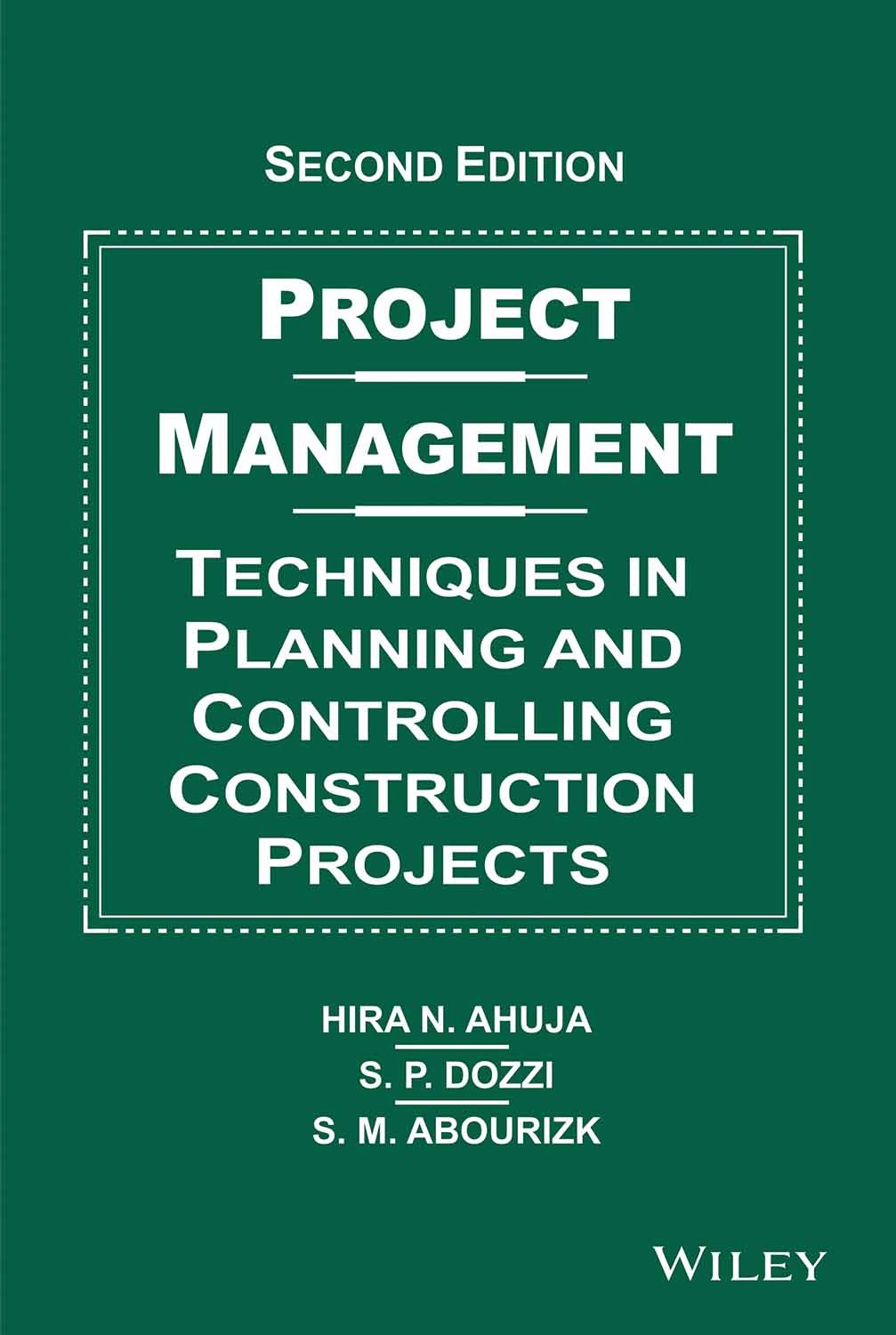
Automated processes
With the help of automation in HR systems, companies can now track data from different HR functions and analyse them to discover trends and patterns. This data can be used to produce actionable items and improve the employee experience. Software that automates HR processes can help companies improve process transparency and make it easier for employees to change benefits and processes.
Costs
Investing on HR software can help to save money. It eliminates the need of multiple manual entry steps and eliminates mistakes. It can also increase employee productivity, retention, and engagement. It can be difficult to choose the right system. Before making the investment, it is important to consider your budget and the number of users you'll need.
Modularity
Modularity within HR systems refers to the ability of building HR systems that can scale with your organization. While a typical unified human resource system would require a lot of server space to maintain, a modular one allows for you to only buy what you use as your organization grows.
Recruiting
Although HRMS can be a powerful tool to improve the recruitment process, not all HRMS systems are created equal. Although some systems are more advanced than others, it is important to find the right functionality for your company. You should also consider a HRMS that has robust candidate management capabilities if your company experiences high turnover. Make sure you are able to handle multi-state, international payroll scenarios with the system that you're looking at. An analysis function is another important feature that you should look for in a system. This can help a business plan its workforce.
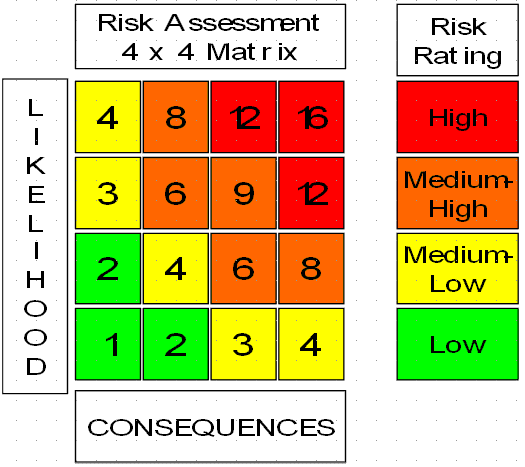
Onboarding
HR systems onboarding software helps HR professionals create engaging onboarding experiences for new hires. These software solutions allow organizations to automate administrative tasks like hiring and training new employees. These systems can either be purchased as a standalone product or part of a complete HR software suite. These systems give employees 24/7 access to their records and information.
FAQ
What is Kaizen?
Kaizen is a Japanese term for "continuous improvement." It encourages employees constantly to look for ways that they can improve their work environment.
Kaizen is founded on the belief of everyone being able to do their job well.
What does "project management" mean?
This refers to managing all activities that are involved in a project's execution.
We include defining the scope of the project, identifying the requirements, preparing the budget, organizing the project team, scheduling the work, monitoring progress, evaluating results, and closing down the project.
What is the difference between management and leadership?
Leadership is about influencing others. Management is about controlling others.
A leader inspires others while a manager directs them.
Leaders motivate people to succeed; managers keep workers on track.
A leader develops people; a manager manages people.
Statistics
- As of 2020, personal bankers or tellers make an average of $32,620 per year, according to the BLS. (wgu.edu)
- This field is expected to grow about 7% by 2028, a bit faster than the national average for job growth. (wgu.edu)
- The average salary for financial advisors in 2021 is around $60,000 per year, with the top 10% of the profession making more than $111,000 per year. (wgu.edu)
- Our program is 100% engineered for your success. (online.uc.edu)
- The profession is expected to grow 7% by 2028, a bit faster than the national average. (wgu.edu)
External Links
How To
What is Lean Manufacturing?
Lean Manufacturing methods are used to reduce waste through structured processes. They were developed in Japan by Toyota Motor Corporation (in the 1980s). The main goal was to produce products at lower costs while maintaining quality. Lean manufacturing is about eliminating redundant steps and activities from the manufacturing process. It is made up of five elements: continuous improvement, continuous improvement, just in-time, continuous change, and 5S. Pull systems allow customers to get exactly what they want without having to do extra work. Continuous improvement means continuously improving on existing processes. Just-in–time refers when components or materials are delivered immediately to their intended destination. Kaizen means continuous improvement. Kaizen involves making small changes and improving continuously. Five-S stands for sort. It is also the acronym for shine, standardize (standardize), and sustain. To achieve the best results, these five elements must be used together.
Lean Production System
Six key concepts form the foundation of the lean production system:
-
Flow - focuses on moving information and materials as close to customers as possible.
-
Value stream mapping - Break down each stage in a process into distinct tasks and create an overview of the whole process.
-
Five S's, Sort, Set in Order, Shine. Standardize. and Sustain.
-
Kanban is a visual system that uses visual cues like stickers, colored tape or stickers to keep track and monitor inventory.
-
Theory of constraints: Identify bottlenecks and use lean tools such as kanban boards to eliminate them.
-
Just-in Time - Send components and material directly to the point-of-use;
-
Continuous improvement - incremental improvements are made to the process, not a complete overhaul.