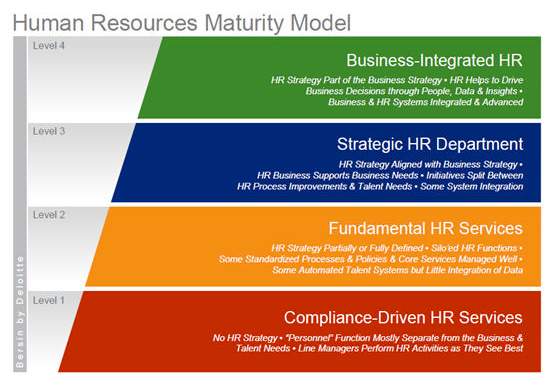
It is important to maintain consistency between contracts in construction projects that involve multiple parties. Prime contracts often contain provisions that are passed on to subcontractors and other sub-subcontractors. Parties to a project should obtain a copy to verify that all agreements are in compliance.
Job order
Job order contractual (JOC) can be used to manage project costs and time. It can also be used to quickly respond to ongoing projects and clear any deferred maintenance. JOC contracts are more flexible than traditional contracting methods.
With job order contracting, the project owner and contractor are more transparent from day one. They are familiar with each other's work history and background, and they can trust one another. This can reduce the number and complexity of change orders. Contractor and owner can develop a better relationship by understanding each other during contracting. This also helps to avoid many changes due to miscommunications or errors.
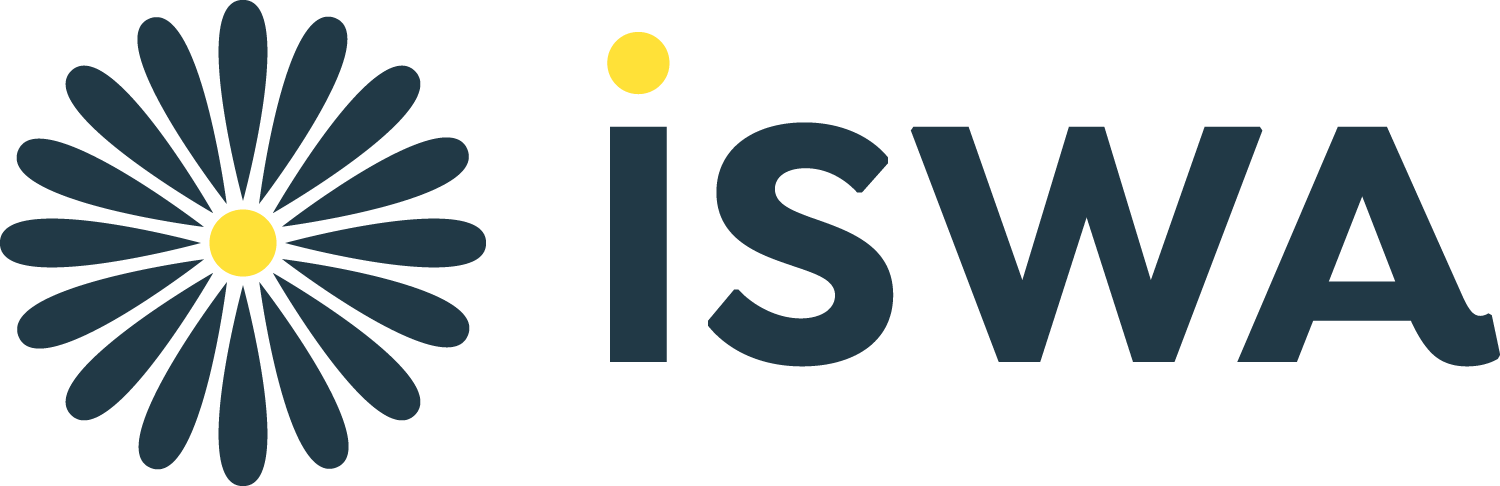
Incentive
Incentive contracting is a form of collaboration between a construction contractor and the client. The goal of incentive contracting is to maximize value for money. A share formula and a target cost are the two major components of an incentive contract. After a competitive process, the target cost should be agreed upon. It should also reflect the most accurate estimate for the project's eventual costs. The contractor gets paid a fee that covers their overheads. The share formula determines how the target cost savings should go between the parties and is what creates the incentive in the contract.
Incentive contracts offer a great opportunity to create an atmosphere of accountability, transparency, and cooperation. Contractors are more likely to update owners with the status of work in progress if they are informed by all parties. These updates encourage closer cooperation and allow for more skilled personnel assignments.
Lump-sum
Lump sum contracting in construction refers to a type of contracting, in which a fixed amount has been agreed upon. This contract has a fixed input, target, and output. This type is best used when the project requirements are clear and well-defined. There are disadvantages to lump sum contracting.
This is because contractors have the option of hiding their profit margins. Contractors are not required by law to give detailed bills of costs and quotes to their owners. One disadvantage to lump-sum contracts are that they can be subject to disputes or claims arising from poor contract terms. For example, in some cases, the contractor may submit an unbalanced quote, in which the unit prices are increased to cover items that will be used later on the project. This could lead to disputes about payment rates.
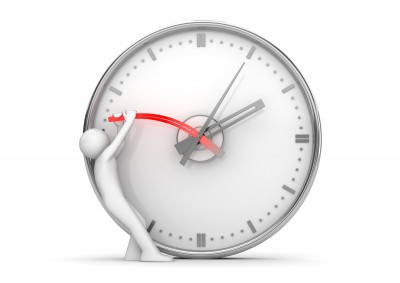
Delivery of integrated project services
Integrated Project Delivery, also known as IPD, is a new delivery method for construction projects. It seeks to eliminate the obstacles that hinder effective project performance and aligns stakeholders around a common goal. It helps increase the probability that projects will be successful. Implementing IPD means a change in traditional project management techniques and increased planning. Legal concerns, mistrust among key stakeholders, and lack of owner will are some of the main barriers to IPD. Many professionals and organizations working in the built environment are now aware of the benefits IPD has and are starting to implement the concept in smaller projects.
The advantages of IPD include the ability to complete projects faster and reduce costs. The IPD method allows all stakeholders the freedom to concentrate on what they do best. This in turn results in better client satisfaction.
FAQ
How do you define Six Sigma?
People who have worked with statistics and operations research will usually be familiar with the concepts behind six sigma. It can be used by anyone in any business aspect.
It requires high levels of commitment and leadership skills to be successful.
Six Sigma is so popular.
Six Sigma is easy to use and can lead to significant improvements. Six Sigma provides a framework to measure improvements and allows companies to focus on the most important things.
What are the steps involved in making a decision in management?
The decision-making process of managers is complicated and multifaceted. It involves many elements, including analysis, strategy. planning. implementation. measurement. evaluation. feedback.
It is important to remember that people are human beings, just like you. They make mistakes. There is always room to improve, especially if your first priority is to yourself.
This video shows you how management makes decisions. We will explain the importance of different types decisions and how every manager can make them. The following topics will be covered.
How can we make our company culture successful?
A company culture that values and respects its employees is a successful one.
It is founded on three basic principles:
-
Everybody has something of value to share
-
People are treated fairly
-
Individuals and groups can have mutual respect
These values are reflected by the way people behave. They will treat others with kindness and consideration.
They will respect other people's opinions.
They encourage others to express their feelings and ideas.
A company culture encourages collaboration and communication.
People feel free to express their views openly without fear of reprisal.
They understand that errors will be tolerated as long they are corrected honestly.
Finally, the company culture promotes honesty and integrity.
Everybody knows they have to tell the truth.
Everyone understands there are rules that they must follow.
Nobody expects to be treated differently or given favors.
What is TQM and how can it help you?
The industrial revolution saw the realization that prices alone were not sufficient to sustain manufacturing companies. This led to the birth of quality. They needed to improve quality and efficiency if they were going to remain competitive.
Management developed Total Quality Management to address the need for improvement. It focused on all aspects of an organisation's performance. It included continuous improvement, employee involvement and customer satisfaction.
Statistics
- The profession is expected to grow 7% by 2028, a bit faster than the national average. (wgu.edu)
- UpCounsel accepts only the top 5 percent of lawyers on its site. (upcounsel.com)
- The BLS says that financial services jobs like banking are expected to grow 4% by 2030, about as fast as the national average. (wgu.edu)
- This field is expected to grow about 7% by 2028, a bit faster than the national average for job growth. (wgu.edu)
- Our program is 100% engineered for your success. (online.uc.edu)
External Links
How To
How can Lean Manufacturing be done?
Lean Manufacturing processes are used to reduce waste and improve efficiency through structured methods. They were created in Japan by Toyota Motor Corporation during the 1980s. The aim was to produce better quality products at lower costs. Lean manufacturing focuses on eliminating unnecessary steps and activities from the production process. It includes five main elements: pull systems (continuous improvement), continuous improvement (just-in-time), kaizen (5S), and continuous change (continuous changes). It is a system that produces only the product the customer requests without additional work. Continuous improvement means continuously improving on existing processes. Just-in-time is when components and other materials are delivered at their destination in a timely manner. Kaizen stands for continuous improvement. Kaizen can be described as a process of making small improvements continuously. Finally, 5S stands for sort, set in order, shine, standardize, and sustain. These five elements are used together to ensure the best possible results.
Lean Production System
The lean production system is based on six key concepts:
-
Flow - focuses on moving information and materials as close to customers as possible.
-
Value stream mapping- This allows you to break down each step of a process and create a flowchart detailing the entire process.
-
Five S’s - Sorted, In Order. Shine. Standardize. And Sustain.
-
Kanban is a visual system that uses visual cues like stickers, colored tape or stickers to keep track and monitor inventory.
-
Theory of constraints - identify bottlenecks in the process and eliminate them using lean tools like kanban boards;
-
Just-in-time delivery - Deliver components and materials right to your point of use.
-
Continuous improvement - make incremental improvements to the process rather than overhauling it all at once.